Three kinds of manufacturing process for polished mirror aluminum plate sheet
1. mechanical polishing
Mechanical polishing is the mechanical process of improving the surface light zero of the metal products by grinding the polishing wheel with the polishing paste and the grinding stone of the parts. In fact, it is a physical method to make some physical properties of aluminum fully displayed. The friction of the high-speed rotating metal surface of the polishing wheel and the polishing wheel produces high temperature to make the metal surface plastic. On the other hand, the surface of the metal is removed from the micro convex part of the gold surface by the cutting effect of the abrasive; the other side is the other side. The surface of the surface produces metal slip under the action of grinding, thus reducing the roughness of the surface of the mirror polish aluminum sheet, so as to achieve the purpose of exquisite exterior decoration.
2. chemical polishing
The chemical polishing of aluminum plate is the process of chemical treatment of products in a certain temperature and composition of acid and alkali solution to improve the surface brightness. The basic principle is that the dissolving products are easily accumulated in the surface depression, which is quickly passivated, resulting in a considerable difference in the dissolution of metal in the convex and concave sectors.
Chemical polishing is one of the most common polishing processes in industrial applications. Chemical polishing equipment is simple, saving power, high efficiency and low cost. It avoids the cumbersome steps of the assembly, and is not restricted by the shape and size of the parts. Especially when the parts with small size and complex shape can't be mechanically polished, the chemical polishing can get the uniform surface and show the advantages of chemical polishing.
3. electrolytic polishing
Electrolytic polishing refers to the anodic dissolution of the metal work piece in a certain electrolytic solution, which reduces the roughness of the surface and increases the gloss of the metal. The technology has been widely applied in metal static machining, metal products equipment and surface quality and finish.
Electrolytic polishing is the best quality in polishing process. Electrolytic polishing plays an important role in surface finishing.
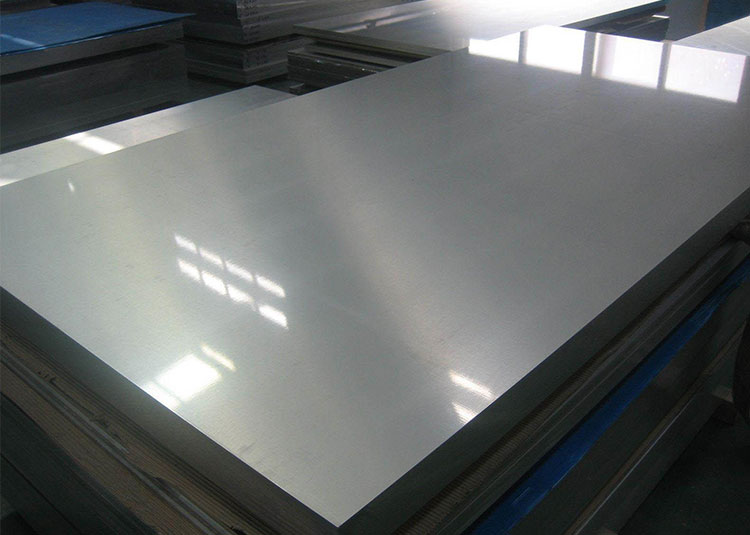
Aluminium Sheets
View Details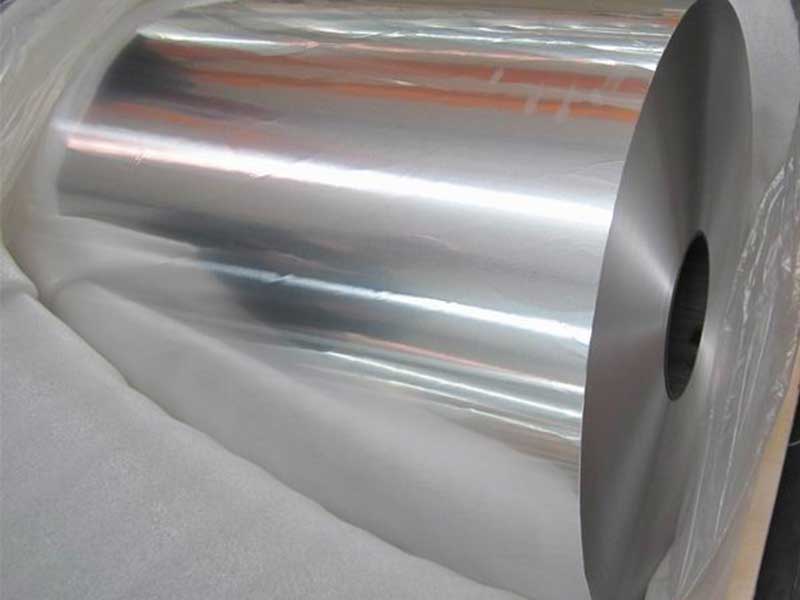
Aluminium Coils
View Details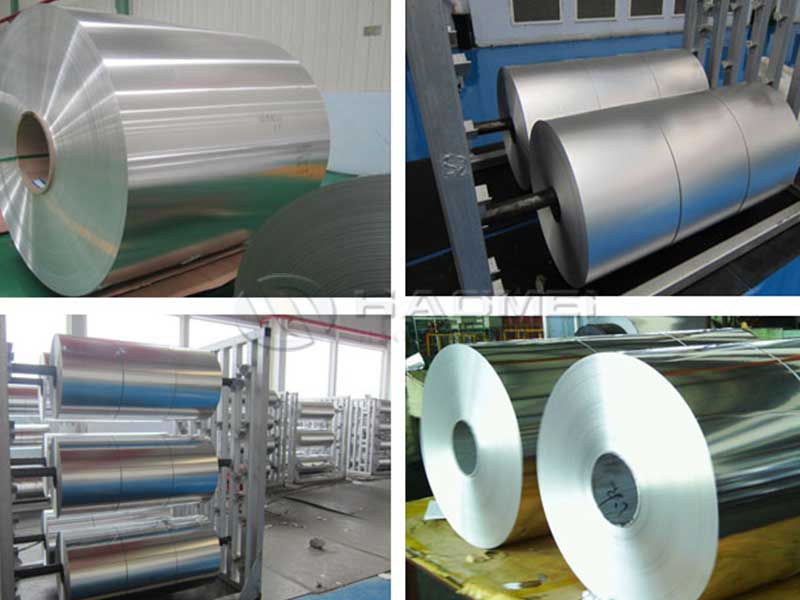
Aluminium Foils
View Details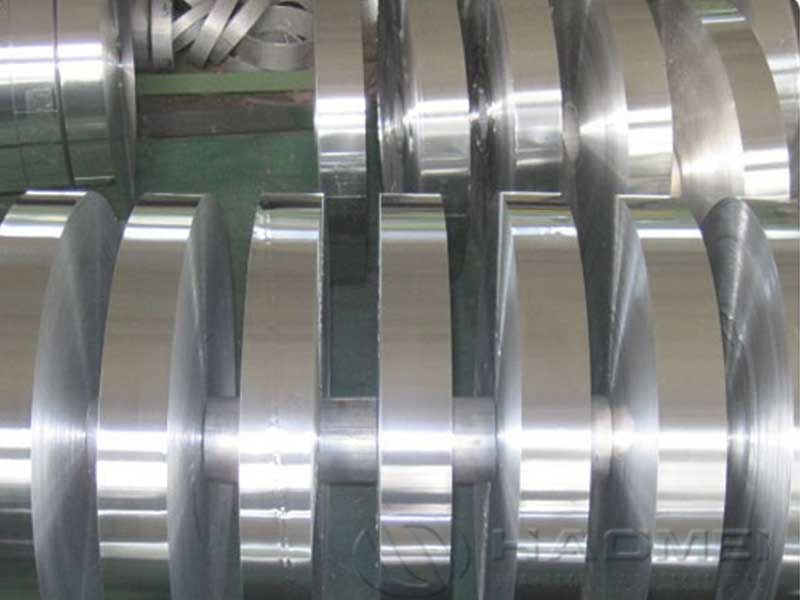
Aluminium Strips
View Details
Aluminium Circles
View Details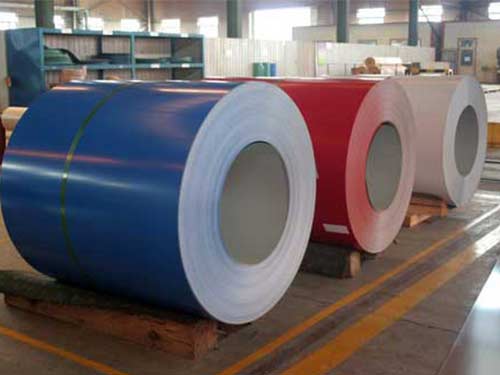
Coated Aluminium
View Details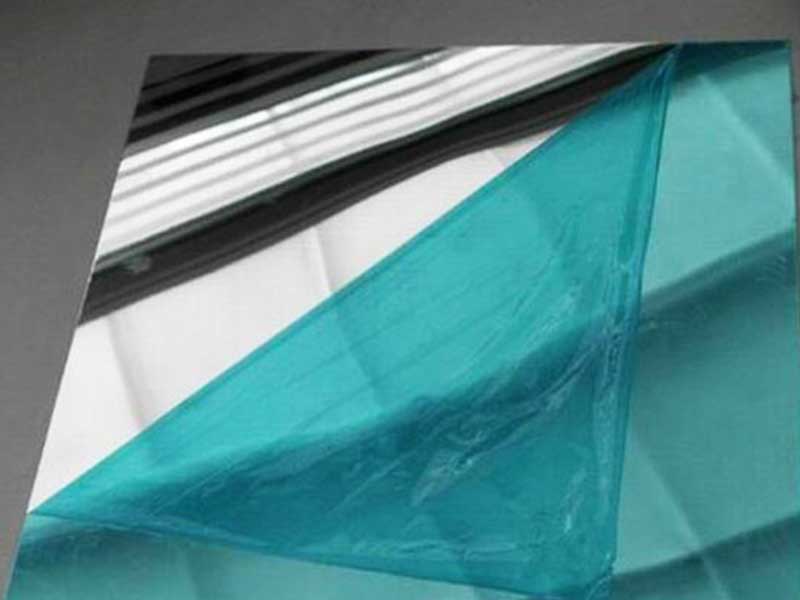
Mirror Aluminum
View Details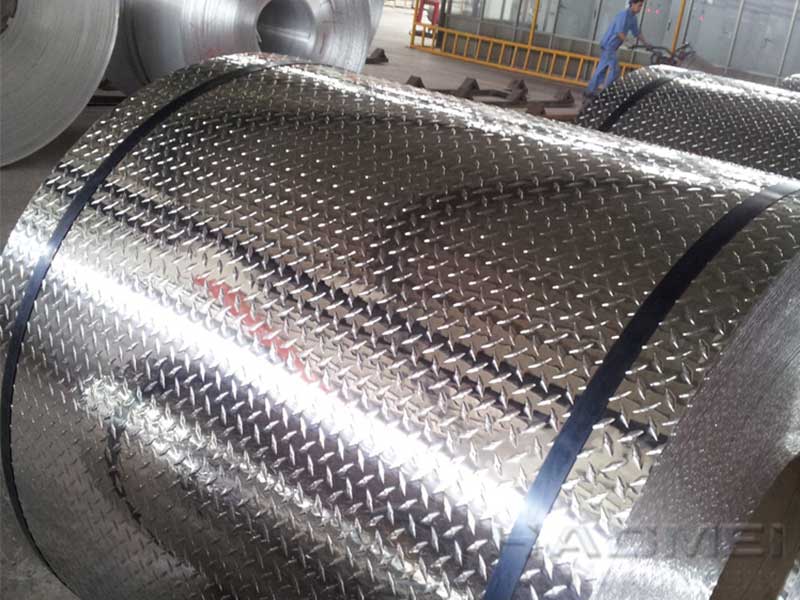
Stucco Embossed Aluminum
View DetailsAluminum
- PVDF Coated aluminium coil 310...
- 1100 aluminum sheet,1100 alumi...
- 0.5mm aluminum jacketing
- circular metal disc
- Embossing Pvc aluminized film...
- 6082 hexagonal aluminum bar ro...
- Aluminum foil composite packag...
- 3104 Aluminum SQUARE Rectangul...
- Insulation aluminum coil jacke...
- blank metal discs
- 1050 aluminum square bar block...
- Aluminum parking sign blanks
- Color coated Color coated insu...
- Flat bimetal bimetallic tube s...
- Aluminum circle plate for traf...
- Custom Aluminum Metal Signs
- Aluminum Disc with hole
- Alloy 3003 aluminum circle for...
- Aluminium 6 series aluminum p...
- 7050 Aluminum Coil