carbon steel aluminum sheets
During the process, element diffusion is more likely to occur in the interface area of the steel/aluminum composite plate, which promotes the metallurgical bonding between the matrix layers, but the interface area often forms a layer of transition structure with different compositions and structures, which has an important impact on the service behavior of the composite plate. . Therefore, it is necessary to conduct in-depth research on the structure evolution law and mechanical response mechanism of the metal layered composite material, and provide an accurate model for the optimization and control of the mechanical properties of the composite plate.
Researchers have carried out a series of studies on the preparation technology and microstructure properties of carbon steel aluminum sheets, revealing the microstructure evolution law of the composite interface. Xu Wei et al. found that the titanium/aluminum composite plate prepared by explosive welding has a wavy interface, and there are a small amount of intermetallic compounds and other island-shaped inclusions in the interface area, resulting in periodic cracks along the interface during subsequent rolling of the composite plate. Research by Liu Xinghai et al. showed that the steel/aluminum composite plate prepared by hot-rolling at a temperature above 550 ℃ will form discontinuous intermetallic compounds and microvoids in the interlayer interface zone, which restricts the interface bonding strength and bending forming of the composite plate. performance. TALEBIAN et al. found that when the annealing temperature is higher than 500 ℃, after 30 minutes of heat preservation treatment, a large number of intermetallic compounds and diffusion holes will be generated at the steel/aluminum composite interface, resulting in high brittleness and fracture separation of the steel/aluminum interface.
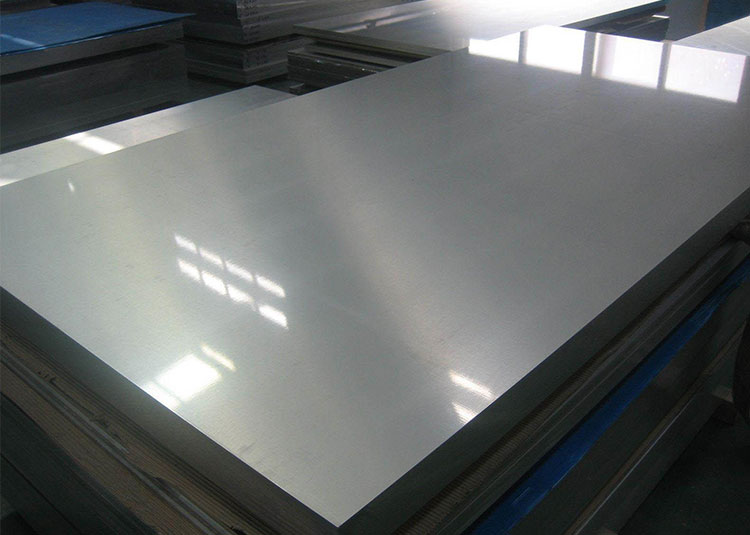
Aluminium Sheets
View Details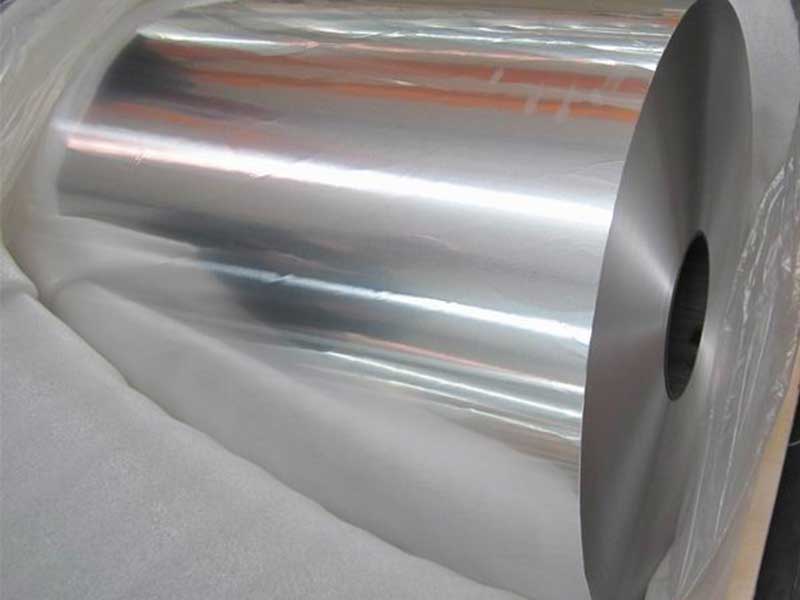
Aluminium Coils
View Details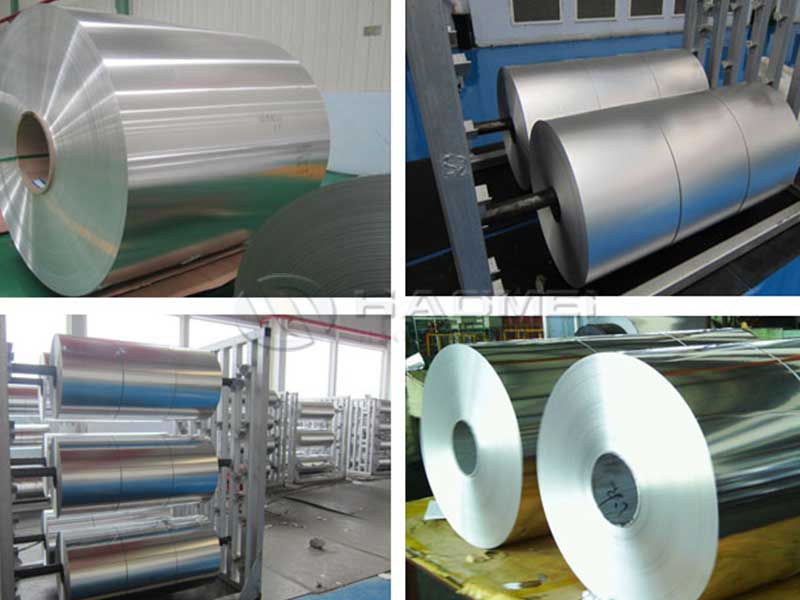
Aluminium Foils
View Details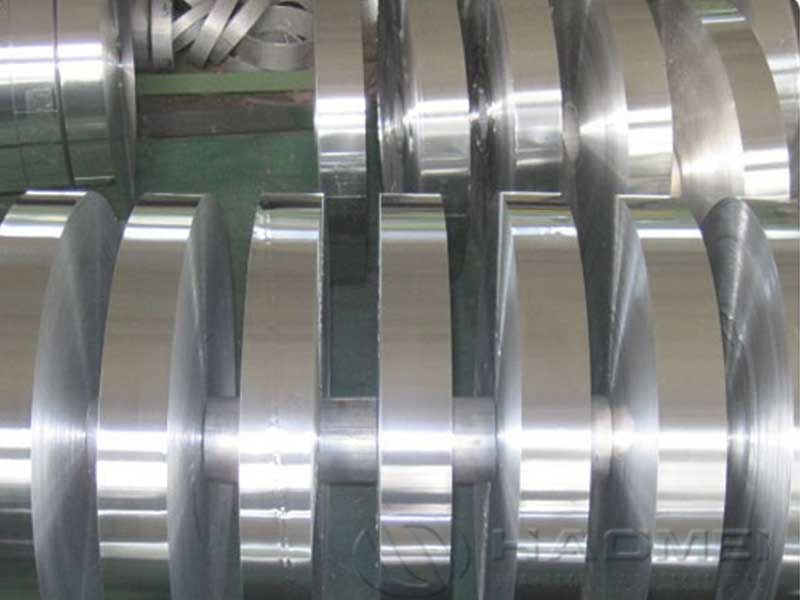
Aluminium Strips
View Details
Aluminium Circles
View Details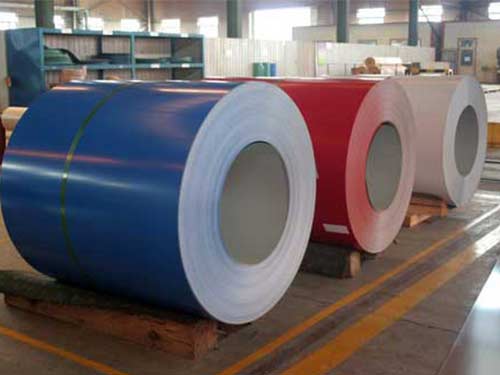
Coated Aluminium
View Details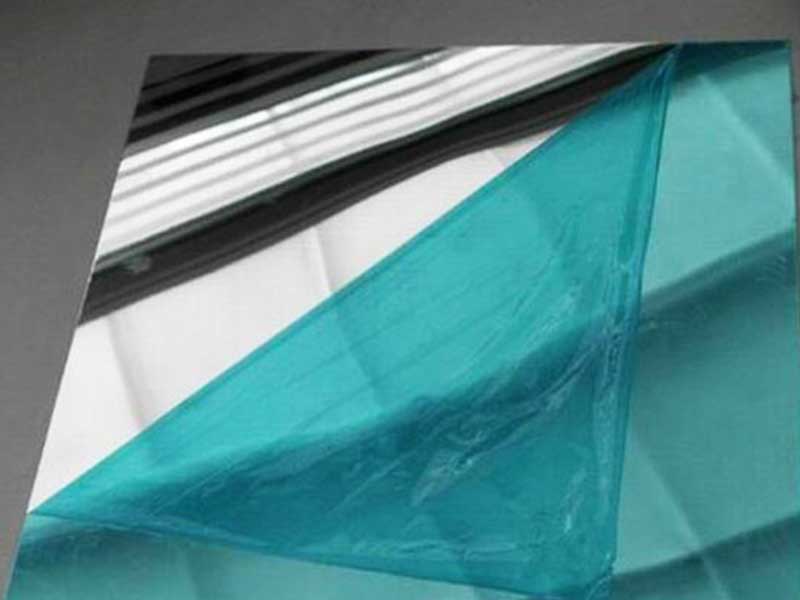
Mirror Aluminum
View Details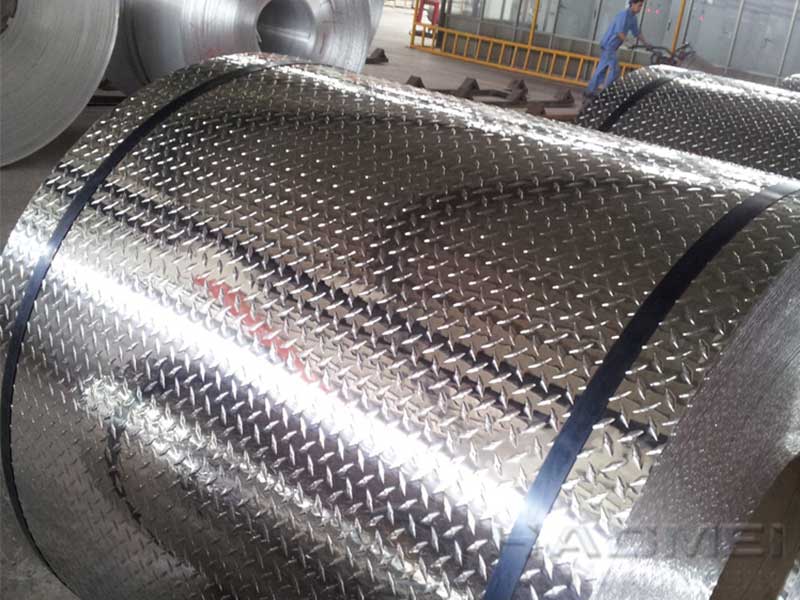
Stucco Embossed Aluminum
View DetailsSteel
- stainless steel clad steel she...
- Aluminum Steel Electrical Tran...
- Copper clad stainless steel pl...
- Brass copper clad steel sheet...
- Three-layer copper stainless s...
- Electrolytic steel claw
- Ti Titanium clad steel plate
- copper clad steel sheet and st...
- aluminum steel transition join...
- Anodized steel jaw for electro...
- Aluminum Electrolyzer Anode St...
- Aluminimun and steel bi metal...
- Explosive production process o...
- aluminum steel triclad transit...
- Prebaked anode steel yoke
- Aluminum steel transition bloc...
- Aluminum rod for Steel Plant D...
- Anode steel claws
- Copper Steel Copper three laye...
- echnical Requirements For Clad...