CAC Foil for Rigid Circuit Boards
CAC foil for rigid circuit boards is a copper aluminum composite plate that directly combines semi molten aluminum with copper through casting and rolling process to obtain 100% composite degree, high bonding strength, low oxidation and low eutectic layer at the interface. After that, copper aluminum composite foil is rolled by finishing mill. The material has excellent mechanical, conductive, thermal conductivity, bending resistance and tear resistance. In addition to the low melting point caused by the characteristics of aluminum and the conductivity slightly lower than that of copper, the comprehensive performance is basically equivalent to that of calendered copper foil.
Since the positive collector of lithium battery must be aluminum and the negative collector must be copper, the connection between copper and aluminum must be involved in the series boost in the module. Because welding must be used to ensure conductivity, the use of copper aluminum composites can greatly reduce the difficulty of copper aluminum connection.
Large electromechanical equipment, such as wind power generator set, has many conductive components and wires inside. There are aluminum and copper. If copper and aluminum are directly connected mechanically, due to their different potentials, it is very easy to cause electrochemical corrosion of aluminum and affect the service life of equipment. Such problems can be avoided by using copper aluminum composites.
In order to reduce the material cost, the majority of circuit board production related industries will use relatively cheap aluminum foil instead of copper foil when the demand for conductivity is not high. But the fatal problem of aluminum is that it is difficult to solder. CAC foil for rigid circuit boards has high adhesion (≥ 100MPa), which can meet the required welding strength of electronic components. The welding performance and strength are consistent with that of copper, but the cost is lower.
Due to the low heat capacity of aluminum radiator, the temperature relative to the environment will be higher, so as to obtain higher heat dissipation efficiency. In addition, the cost of aluminum with the same volume is much lower than that of copper, and the weight is much smaller, so most radiators use aluminum. However, the use of pure aluminum radiator, after all, gives up the higher thermal conductivity when copper is in contact with the heat source. Therefore, in the use of fully metallurgical bonded copper aluminum composites, the thermal conductivity of copper layer materials can be brought into full play, and the advantages of copper and aluminum materials can be truly taken into account; The experimental results also prove the high efficiency of copper aluminum composite radiator. The copper thermal conductivity is 401 (w / MK), the aluminum thermal conductivity is 237 (w / MK), the copper aluminum composite (20% copper layer) thermal conductivity is 580 (w / MK), the specific heat capacity (unit mass) is 683.6kj / (kg · K), and the density is only 3.94g/cm ³; And less copper is used in the material to reduce the cost, which can realize large sheet size and easy to carry out large-scale continuous production.
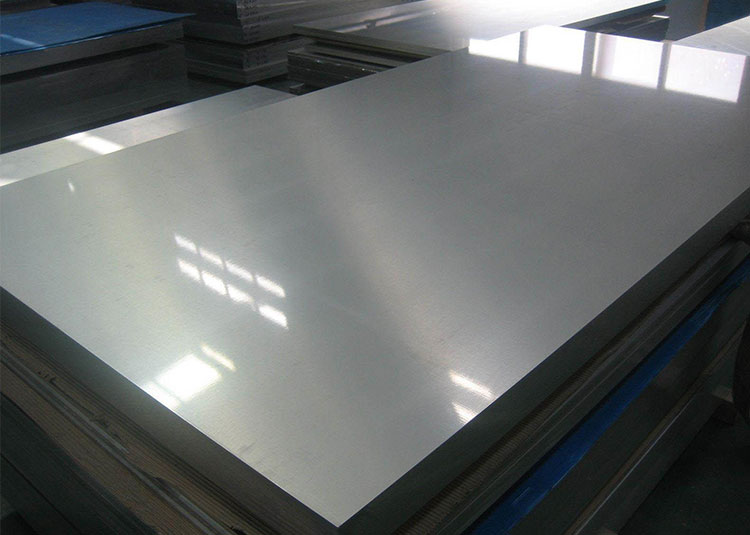
Aluminium Sheets
View Details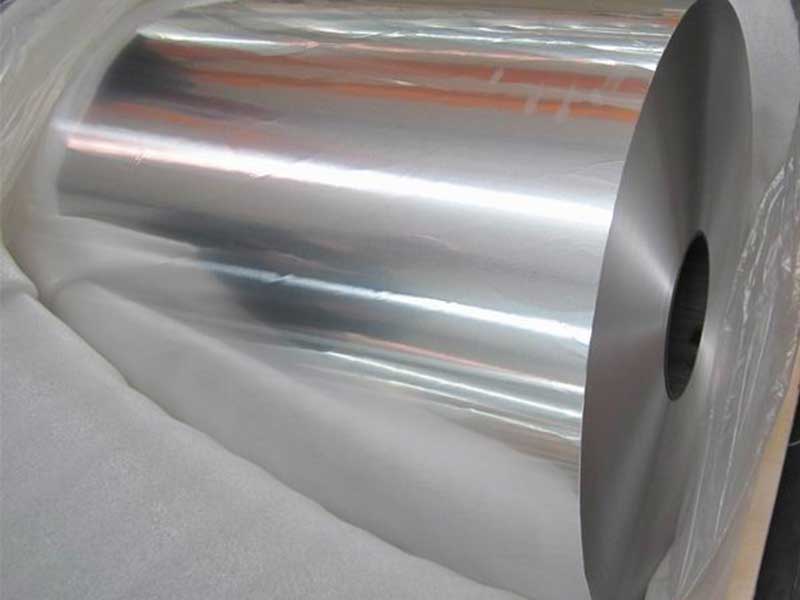
Aluminium Coils
View Details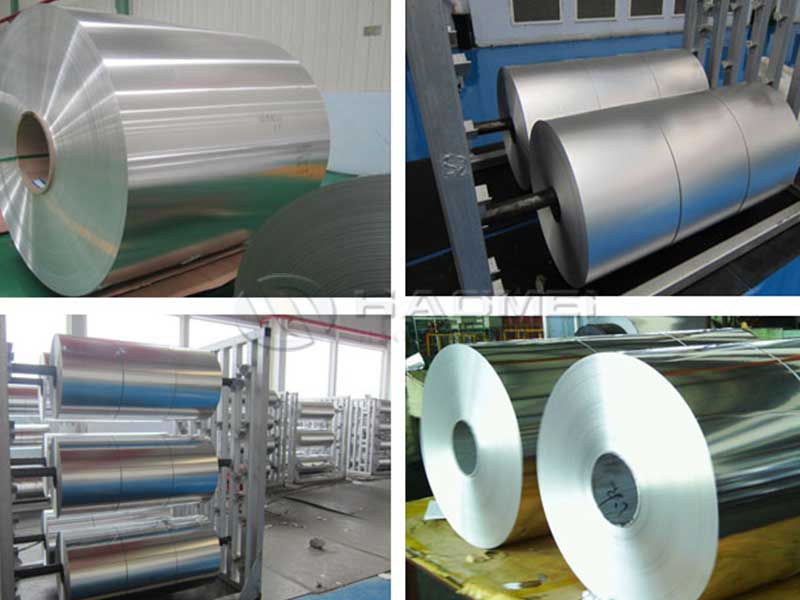
Aluminium Foils
View Details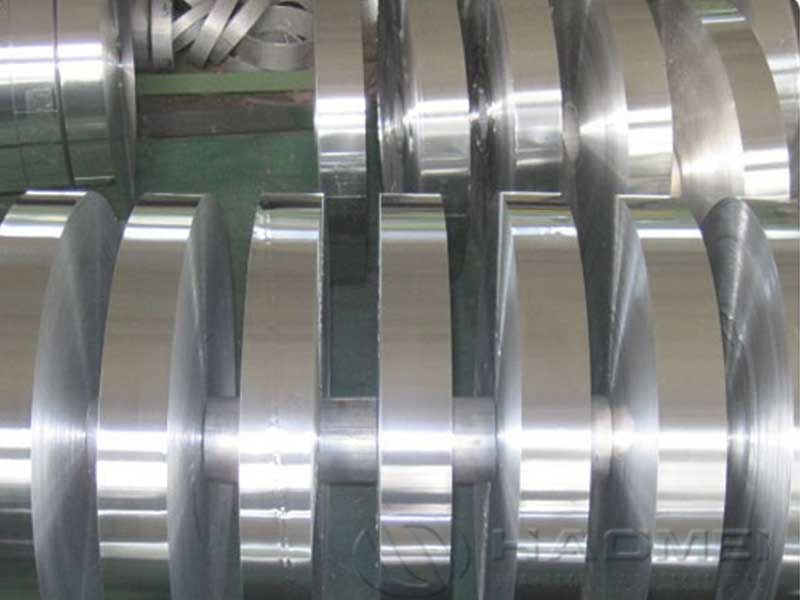
Aluminium Strips
View Details
Aluminium Circles
View Details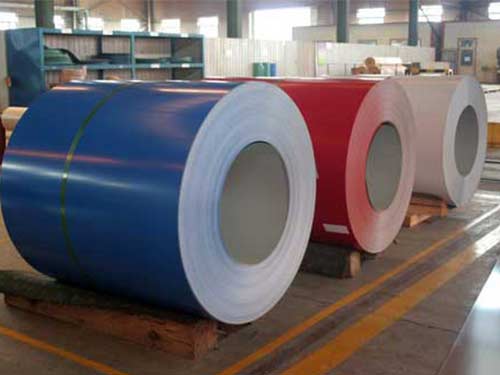
Coated Aluminium
View Details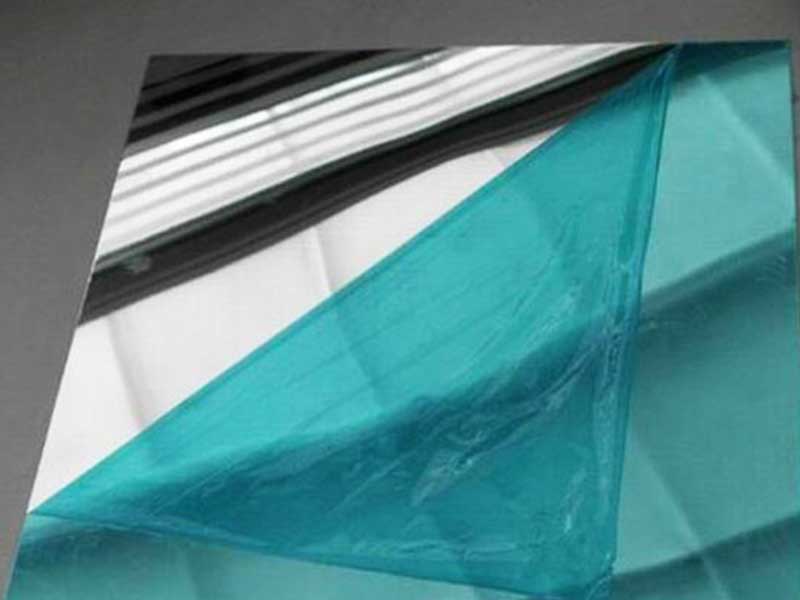
Mirror Aluminum
View Details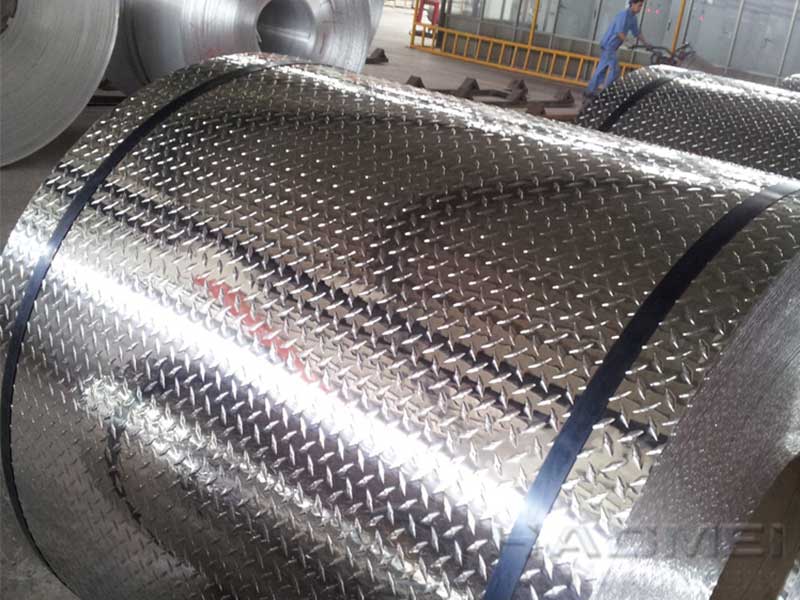
Stucco Embossed Aluminum
View DetailsAluminum
- Mirror aluminum sheet for ligh...
- Explosion welding metal plates
- 4004 H18 aluminium foil for va...
- Custom Aluminum Metal Signs
- Coated Aluminum Coil,Decorativ...
- 4032 Aluminum bar stock
- 7021 Aluminum Block
- The manufacturing principle of...
- 2024 5052 6061 7075 aviation a...
- 7075 aluminum hex bar
- 8079 Aluminium coil
- Introduction to the type of al...
- 5754 Aluminum Circle
- 7010 aluminum block
- What issues pay attention to p...
- Main differences between 7075...
- Aluminum circle blanks sheets
- anodized aluminum sign blanks
- Aluminum circle blanks for tra...
- Prebake anode carbon for elect...