Why do aluminum alloys need to be processed into anodised alu
Aluminum and aluminum alloys naturally form an oxide film in the atmosphere, but the film is thin (40-50 A) and loose and porous. It is amorphous, uneven and continuous, and cannot be used as a reliable protective decoration.
With the continuous development of the aluminum product processing industry, anodizing or chemical oxidation is widely used in the industry to form an oxide film on the surface of aluminum and aluminum alloy parts to achieve the purpose of protection and decoration.
The oxide film obtained by chemical oxidation is generally 0.3~4um thick, and the softness, wear resistance and corrosion resistance are lower than that of the anodized film. Therefore, it is rarely used alone except for special purposes. However, it has a good adsorption capacity and is repainted on its surface, which can effectively improve the corrosion resistance and decorativeness of aluminum products. The thickness of the oxide film obtained by anodizing is generally 5-20v m, and the thickness of the hard anodized film can reach 60-2500m. Its film also has similar characteristics:(1070 anodised aluminium)
(1) The hardness of aluminum processing is high.
(2) Aluminum processing has high corrosion resistance.
(3) Aluminum processing has strong adsorption capacity.
(4) Aluminum processing has good insulation properties.
(5) Strong heat insulation and heat resistance.
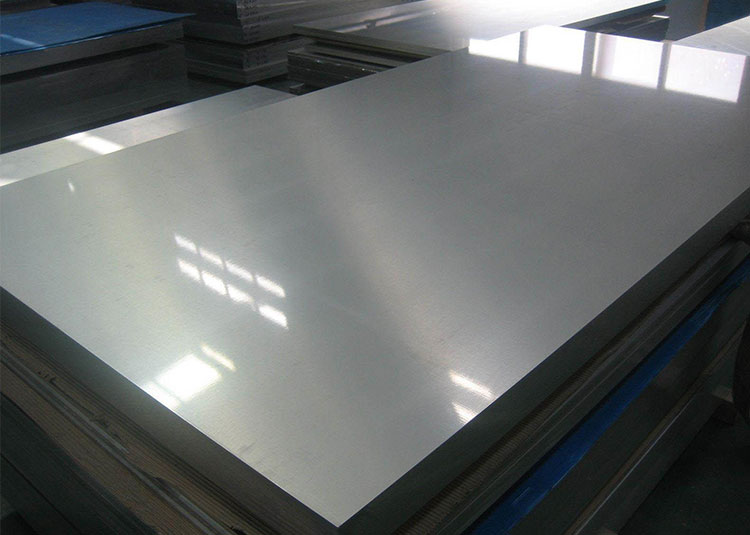
Aluminium Sheets
View Details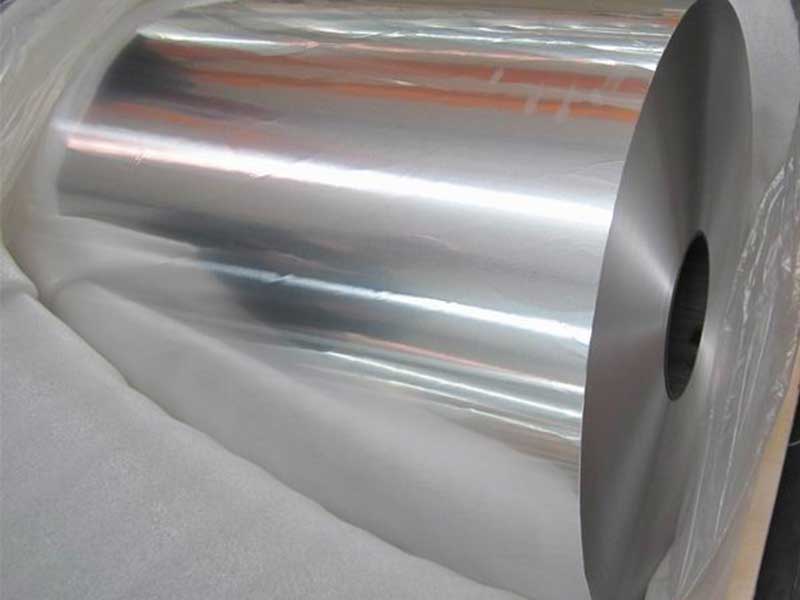
Aluminium Coils
View Details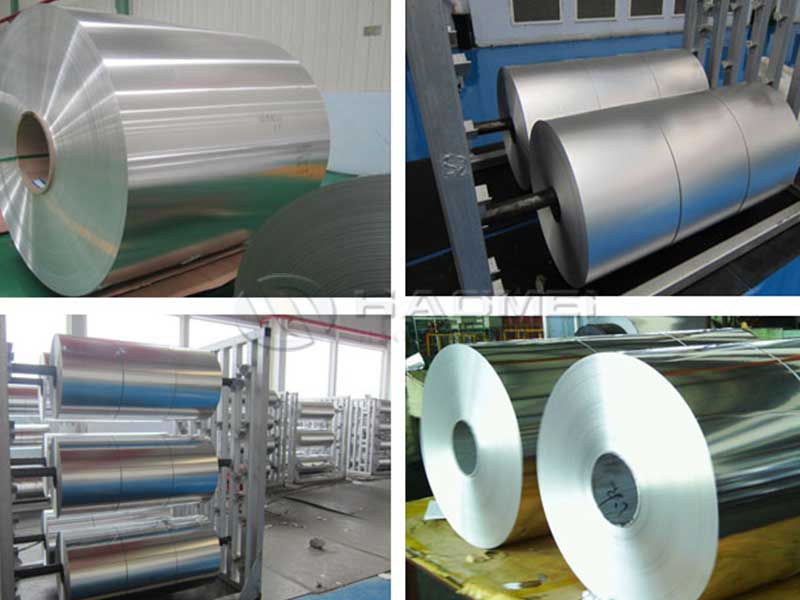
Aluminium Foils
View Details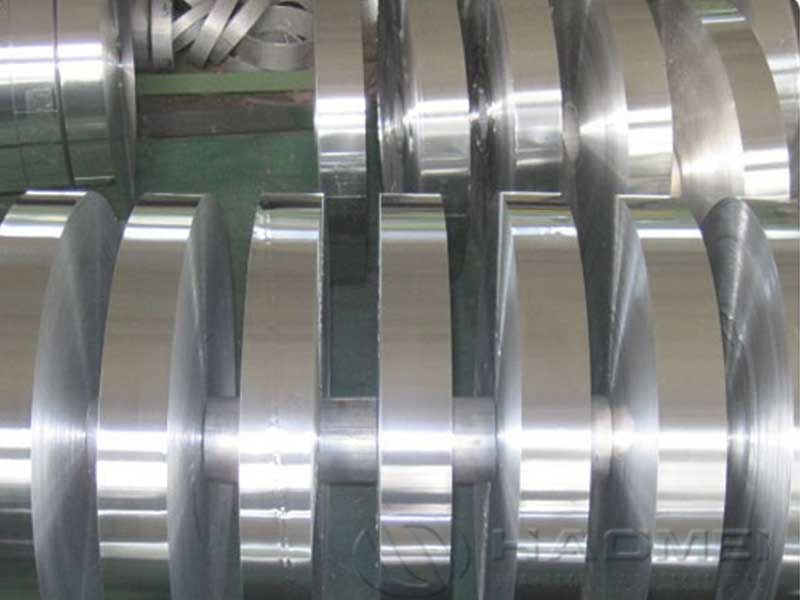
Aluminium Strips
View Details
Aluminium Circles
View Details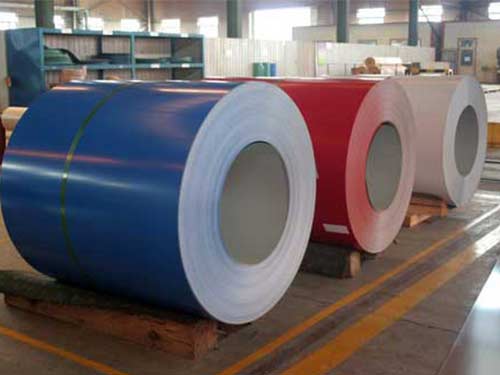
Coated Aluminium
View Details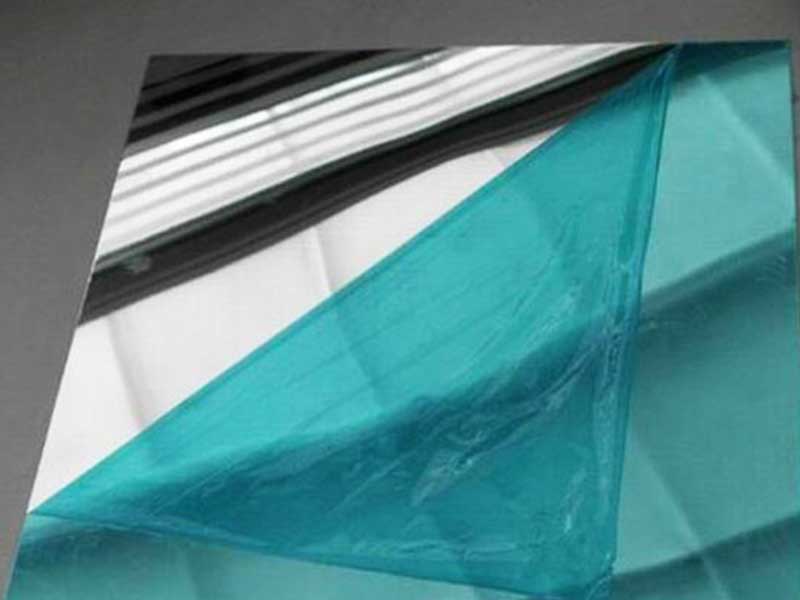
Mirror Aluminum
View Details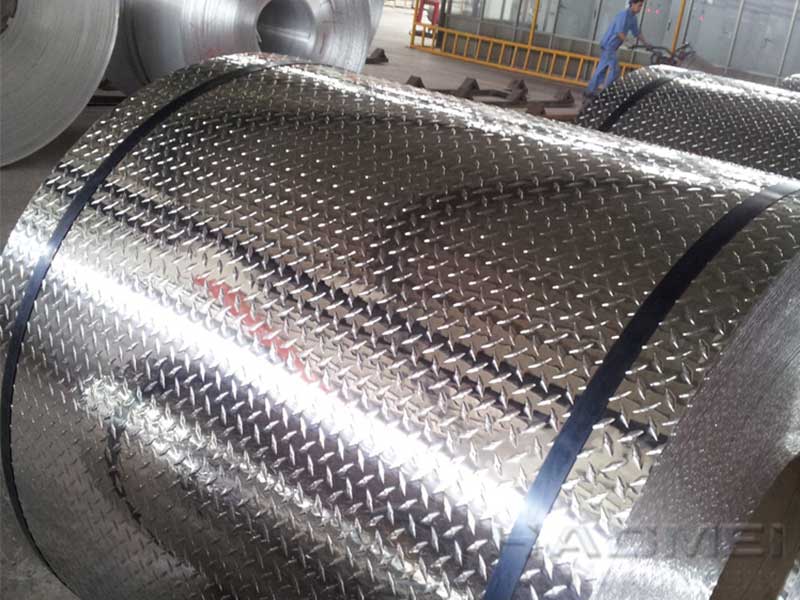
Stucco Embossed Aluminum
View DetailsAluminum
- Alloy 3105 Aluminum Plate
- Aluminum panel sheet
- Aluminium strip for transforme...
- Five Advantages of Energy Savi...
- Aluminum magnesium silicon ant...
- pipe insulation jacketing mate...
- 1060 CC aluminum transformer f...
- Aluminium anodised veneer cano...
- 1060 Aluminum tread plate
- Industrial aluminum plate seve...
- PVDF Aluminium veneer for exte...
- 5056 aluminum sheet plate bloc...
- embossed aluminum sheet and pa...
- 3005 Aluminum circle
- Cosmetic Aluminum Cap Strip Fo...
- Traffic aluminum number plate
- 6061 Aluminum Coil
- aluminium winding wire manufac...
- 1090 aluminum alloy for anodiz...
- Grade 1060 anodised aluminum p...