Research on Effect of Steel Shot Blasting on Surface Integri
During the shot peening process, a large number of projectiles hit the surface of the part, causing the evolution of the microstructure, including the increase of surface roughness value, the increase of dislocation density, grain refinement, the increase of residual stress, the increase of microhardness, etc., which ficantly affects the surface of the part. performance. Appropriate shot peening parameters can cause grain refinement, dislocation density increase, and residual compressive stress on the surface of the material, which is beneficial to improve the fatigue resistance, wear resistance, and corrosion resistance of the material. Due to the repeated impact of the projectiles, the motion of twins and dislocations and their interactions lead to grain refinement and work hardening, which can suppress crack initiation. On the other hand, the existence of residual stress field can inhibit the propagation of fatigue cracks, thereby greatly improving the fatigue strength of materials. Karimbaev et al. pointed out that the surface of the sample treated by ultrasonic nano surface modification technology has smaller grain size, larger residual compressive stress, and higher fatigue resistance. Similar conclusions were also made by Salvati et al. During the fatigue process, the stability of residual stress is crucial. Gan Jin et al. pointed out that under cyclic loading, the stability of residual stress depends on the maximum residual compressive stress and the depth of the residual compressive stress layer. Due to grain refinement and work hardening, the hardness of the surface layer of the material is ficantly improved, and the wear resistance of the material can be improved at the same time. Chamgordani et al pointed out that the surface mechanical grinding treatment can improve the surface hardness of the material, ficantly reduce the friction factor and reduce the wear rate. Yin Meigui et al. pointed out that the impact wear resistance of TC4 titanium alloy samples was ficantly improved after laser shot peening. The same rule is also shown in the AZ31 magnesium alloy after ultrasonic shot peening. It is worth noting that the refined grains provide a large number of grain boundaries, which become active sites for passive film formation and enhance the corrosion resistance of the material. The materials after laser shot peening, ultrasonic shot peening and surface mechanical grinding all showed lower corrosion current density. Under inappropriate shot peening parameters, excessive roughness value and excessive cracks on the surface of the material will also have a negative impact on the material properties. At higher strain amplitudes, the surface roughness and microcracks are the main factors affecting the fatigue life of materials. Excessive surface roughness values will also reduce the wear and corrosion resistance of the material. Silva et al. pointed out that the large rough surface of the material caused by shot peening reduces the wear resistance of the material, and after the rough surface is properly removed, the wear resistance of the material can be improved. Peral et al. also pointed out that the surface roughness can affect the corrosion resistance of the material, and the corrosion rate of the shot peened surface is ficantly reduced after electropolishing. It can be seen that the microstructure evolution of the surface material caused by shot peening has a very important influence on the properties of the Aluminium Alloy Blocks 2024 T352.
Although the respective general laws of shot peening techniques have been established, there is no effective comparison of the effects of different shot peening methods on the surface microstructure of materials under the same shot peening intensity. Therefore, in order to further clarify the effect of the shot peening method on the surface material under the same shot peening intensity, the author took the Aluminium Alloy Blocks 2024 T352 as the research object, under the shot peening intensity of the A-type Armin test piece with a nominal arc height of 0.15 mm , to evaluate the effects of ultrasonic shot peening and pneumatic shot peening on the surface morphology, microstructure, residual stress, and microhardness of materials.
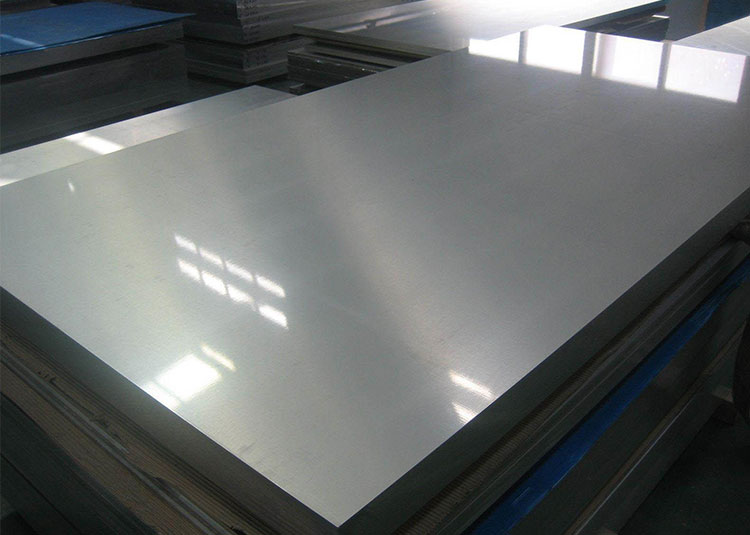
Aluminium Sheets
View Details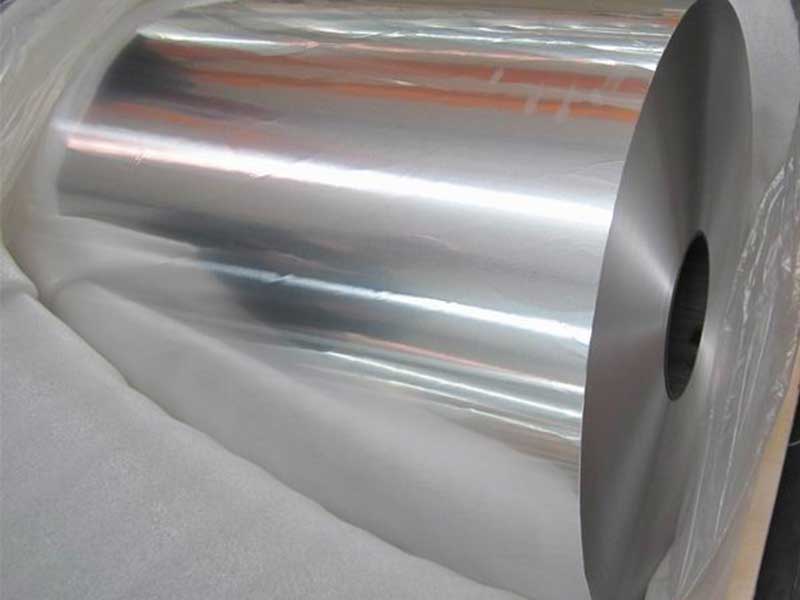
Aluminium Coils
View Details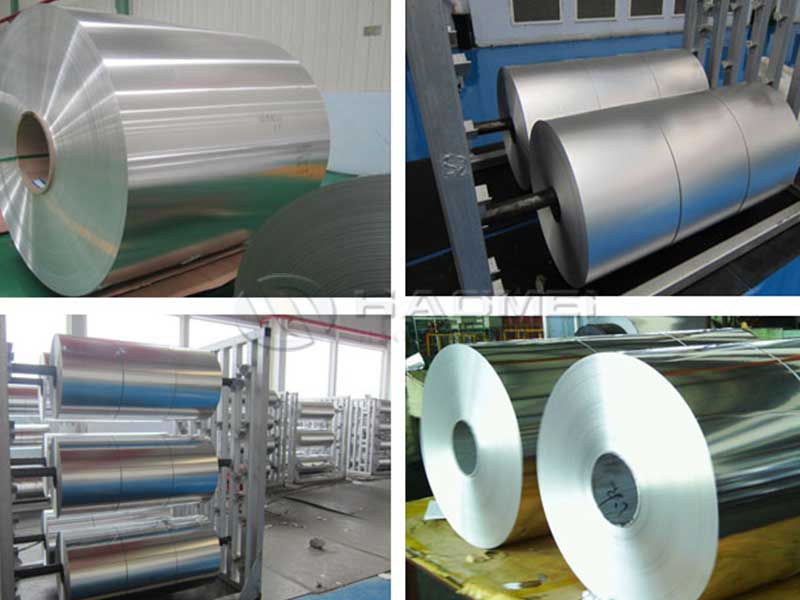
Aluminium Foils
View Details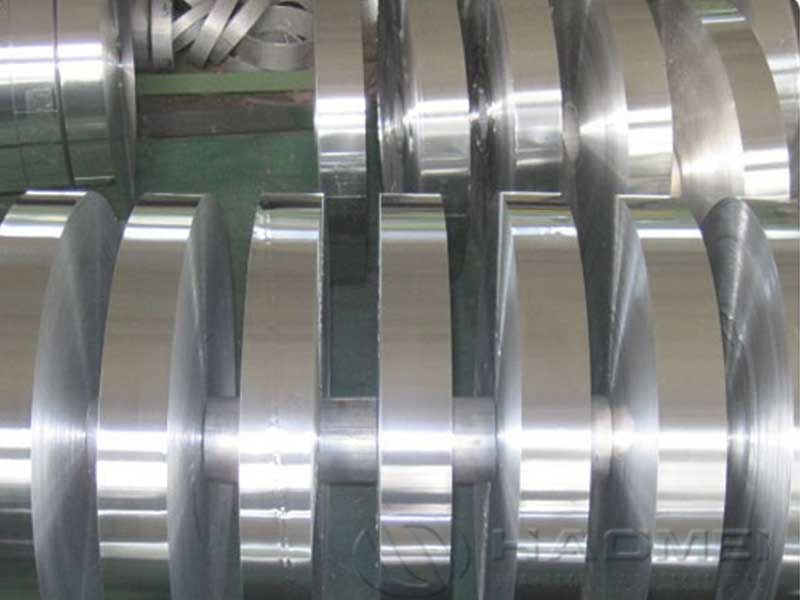
Aluminium Strips
View Details
Aluminium Circles
View Details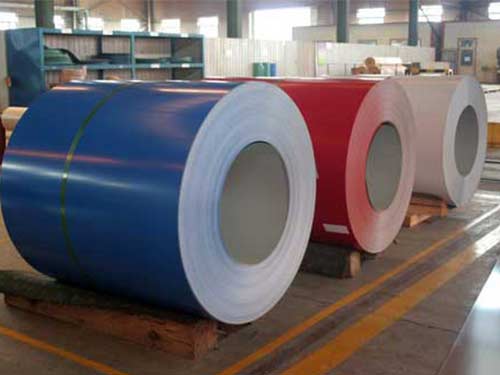
Coated Aluminium
View Details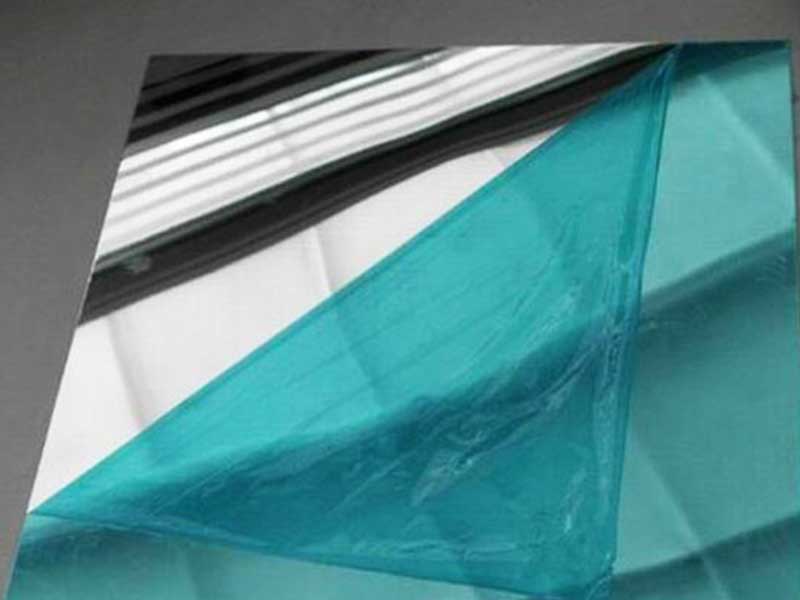
Mirror Aluminum
View Details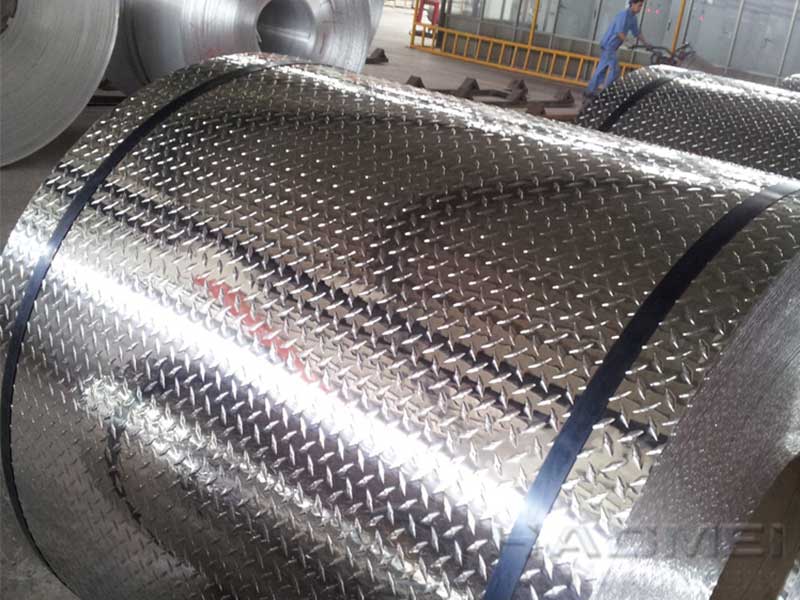
Stucco Embossed Aluminum
View DetailsSteel
- stainless steel Titanium zirco...
- Copper steel explosive bonded...
- Aluminum steel explosion weldi...
- Titanium clad steel plate for...
- Explosive production process o...
- The anode steel claw
- Aluminum / Titanium / Carbon S...
- Aluminum rod for Steel Plant D...
- Aluminium -Chromium-Steel Mult...
- carbon steel aluminum sheets
- Titanium Clad Steel Plate Shee...
- stainless steel copper aluminu...
- stainless steel aluminum tri p...
- aluminum steel transition join...
- Aluminum steel transition bloc...
- Monel carbon steel clad plate
- Research on Effect of Steel Sh...
- Anode steel claws
- Ti Titanium clad steel plate
- echnical Requirements For Clad...