es ampliamente utilizado en los campos de la aviación y aeroespacial debido a sus excelentes propiedades mecánicas y alta resistencia a la corrosión. El fallo de las piezas por corrosión, desgaste y fatiga suele originarse en la superficie del material, por lo que es necesario utilizar técnicas adecuadas de preparación de la superficie. El granallado puede causar cambios en la microestructura de la superficie del material, lo que puede mejorar de manera efectiva las propiedades superficiales de las piezas.
Durante el proceso de granallado, una gran cantidad de proyectiles golpean la superficie de la pieza, provocando la evolución de la microestructura, incluido el aumento del valor de rugosidad de la superficie, el aumento de la densidad de dislocación, el refinamiento del grano, el aumento de la tensión residual, el aumento de microdureza, etc., que afecta de forma importante a la superficie de la pieza. actuación. Los parámetros de granallado adecuados pueden provocar el refinamiento del grano, el aumento de la densidad de dislocaciones y la tensión de compresión residual en la superficie del material, lo que es beneficioso para mejorar la resistencia a la fatiga, al desgaste y a la corrosión del material. Debido al impacto repetido de los proyectiles, el movimiento de los gemelos y las dislocaciones y sus interacciones conducen al refinamiento del grano y al endurecimiento por trabajo, lo que puede suprimir el inicio de grietas. Por otro lado, la existencia de un campo de tensión residual puede inhibir la propagación de grietas por fatiga, mejorando así en gran medida la resistencia a la fatiga de los materiales. Karimbaev et al. señaló que la superficie de la muestra tratada con la tecnología de modificación ultrasónica de nano superficie tiene un tamaño de grano más pequeño, una mayor tensión de compresión residual y una mayor resistencia a la fatiga. Salvati et al. también llegaron a conclusiones similares. Durante el proceso de fatiga, la estabilidad de la tensión residual es crucial. Gan Jin et al. señaló que bajo carga cíclica, la estabilidad de la tensión residual depende de la tensión de compresión residual máxima y la profundidad de la capa de tensión de compresión residual. Debido al refinamiento del grano y al endurecimiento por trabajo, la dureza de la capa superficial del material mejora significativamente y, al mismo tiempo, se puede mejorar la resistencia al desgaste del material. Chamgordani et al señalaron que el tratamiento de rectificado mecánico de la superficie puede mejorar la dureza de la superficie del material, reducir significativamente el factor de fricción y reducir la tasa de desgaste. Yin Meigui et al. señaló que la resistencia al desgaste por impacto de las muestras de aleación de titanio TC4 mejoró significativamente después del granallado con láser. La misma regla también se muestra en la aleación de magnesio AZ31 después del granallado ultrasónico. Vale la pena señalar que los granos refinados proporcionan una gran cantidad de límites de grano, que se convierten en sitios activos para la formación de películas pasivas y mejoran la resistencia a la corrosión del material. Los materiales después del granallado por láser, el granallado ultrasónico y el rectificado mecánico superficial mostraron una menor densidad de corriente de corrosión. Bajo parámetros de granallado inadecuados, un valor de rugosidad excesivo y grietas excesivas en la superficie del material también tendrán un impacto negativo en las propiedades del material. A amplitudes de deformación más altas, la rugosidad de la superficie y las microfisuras son los principales factores que afectan la vida de fatiga de los materiales. Los valores excesivos de rugosidad superficial también reducirán la resistencia al desgaste y la corrosión del material. Silva et al. señaló que la gran superficie áspera del material causada por el granallado reduce la resistencia al desgaste del material, y después de eliminar adecuadamente la superficie áspera, se puede mejorar la resistencia al desgaste del material. Peral et al. También señaló que la rugosidad de la superficie puede afectar la resistencia a la corrosión del material, y la tasa de corrosión de la superficie granallada se reduce considerablemente después del electropulido. Se puede observar que la evolución de la microestructura del material superficial provocada por el granallado tiene una influencia muy importante en las propiedades delBloques de aleación de aluminio 2024 T352.
Aunque se han establecido las respectivas leyes generales de las técnicas de granallado, no existe una comparación efectiva de los efectos de diferentes métodos de granallado sobre la microestructura superficial de los materiales bajo la misma intensidad de granallado. Por lo tanto, para aclarar aún más el efecto del método de granallado en el material de la superficie bajo la misma intensidad de granallado, el autor tomó laBloques de aleación de aluminio 2024 T352como objeto de investigación, bajo la intensidad de granallado de la probeta Armin tipo A con una altura de arco nominal de 0,15 mm, para evaluar los efectos del granallado ultrasónico y granallado neumático en la morfología superficial, microestructura, tensión residual y microdureza de los materiales.
Investigación sobre el efecto del granallado de acero en la integridad de la superficie
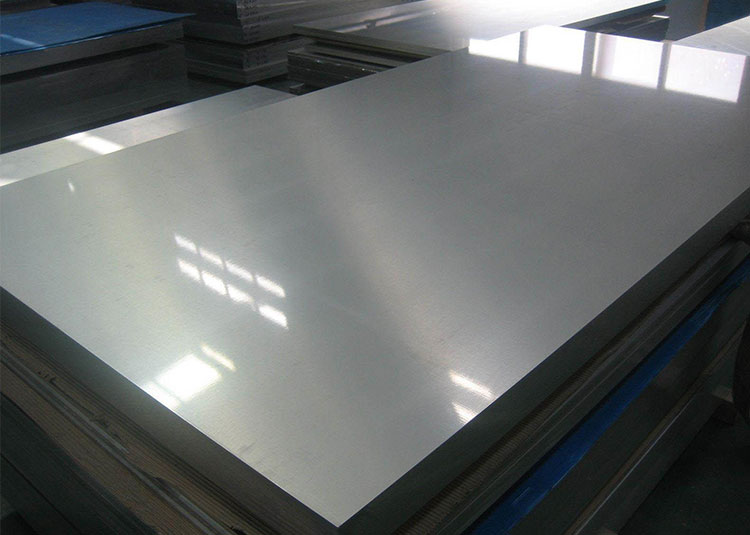
Hojas de aluminio
Ver detalles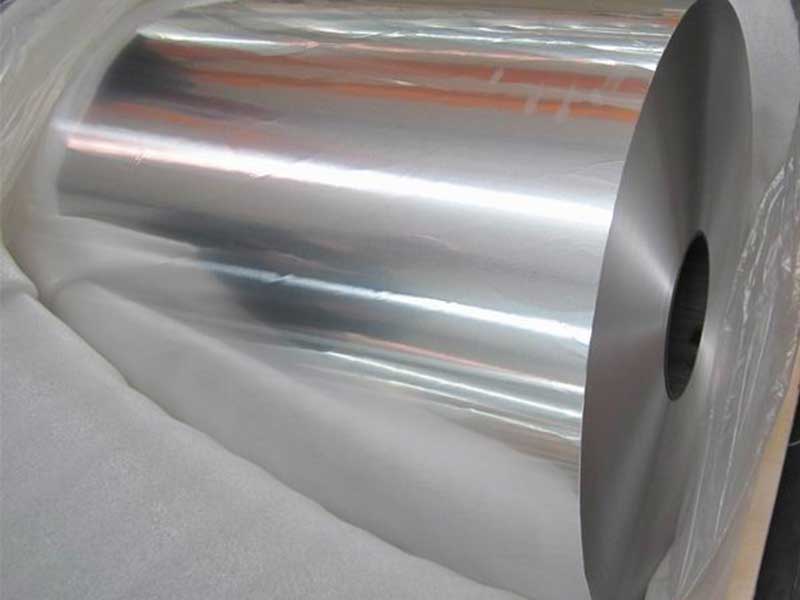
Bobinas de aluminio
Ver detalles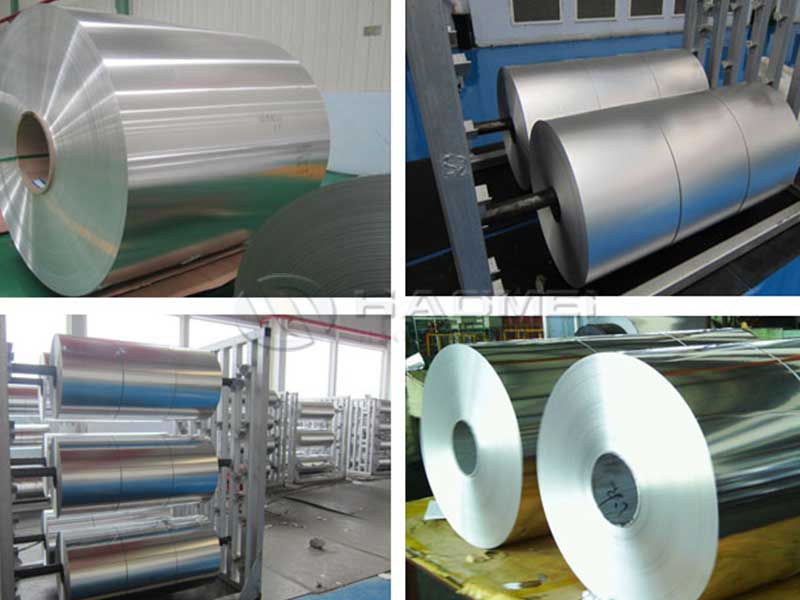
Láminas de aluminio
Ver detalles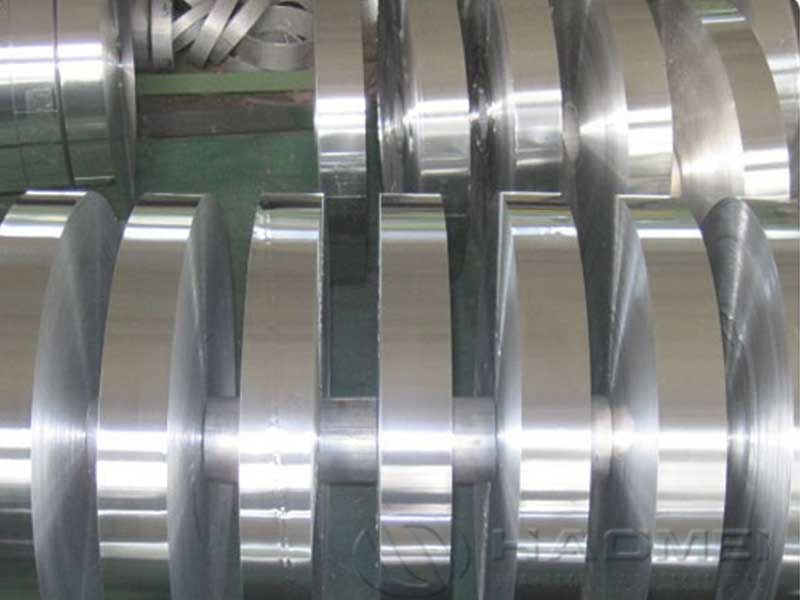
Tiras de aluminio
Ver detalles
círculos de aluminio
Ver detalles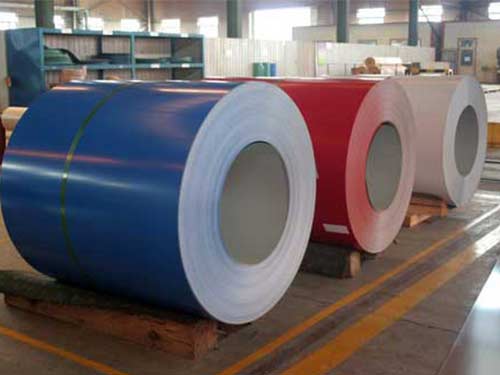
Aluminio revestido
Ver detalles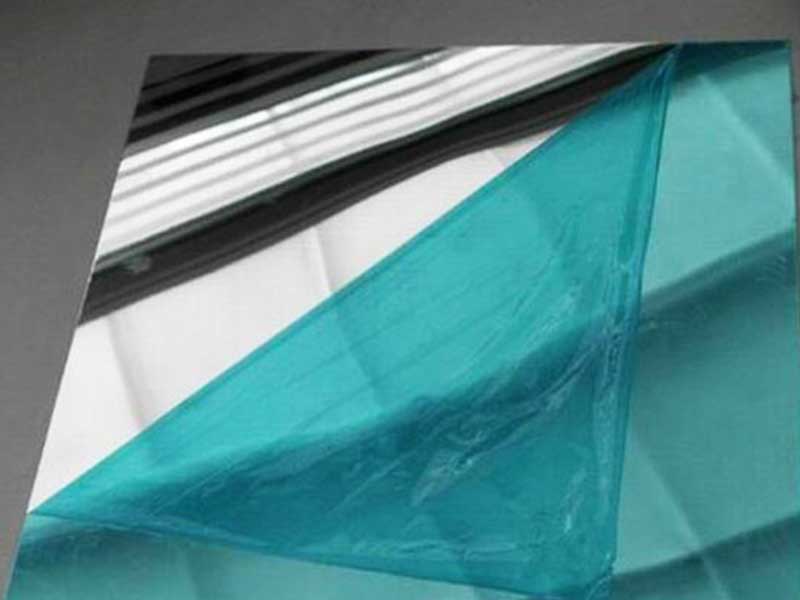
Espejo Aluminio
Ver detalles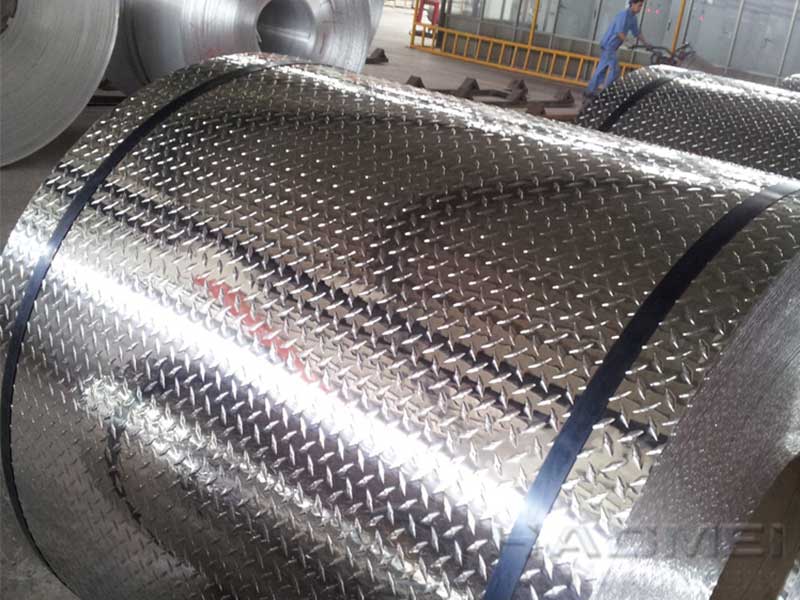
Aluminio Repujado Estuco
Ver detallesAcero
- Placa de acero inoxidable reve...
- Investigación sobre el...
- Placa de chapa revestida de co...
- Barra de varilla revestida bim...
- Bimetal de acero revestido de...
- Placa revestida de acero de ti...
- Círculo triplemente rev...
- Bloque de soldadura explosiva...
- tira de bobina de acero revest...
- Mordaza de acero anodizado par...
- barra de cobre revestida de ac...
- círculo revestido de al...
- Aplicación de garra de...
- El semirremolque se realizar&a...
- tubo de acero inoxidable titan...
- Tira de bobina revestida de ac...
- círculo revestido de al...
- Placa revestida de acero al ca...
- Garra de acero electrolí...
- Placa revestida de acero titan...