Introduction to the rolling process of aluminum foil
2.1 Control of rolling oil amount The thickness of residual oil on the surface of the double-zero aluminum foil in the hard temper is about 0.02 to 0.2 μm. The large amount of residual oil on the surface will cause difficulties in the refining and processing of aluminum foil such as compounding and printing. In actual production, the amount of oil on the surface of the aluminum foil on the outlet side of the rolling mill should be closely monitored, and no visible white oil traces are allowed. Line parameters, etc.
2.2 Control of rolling speed If the rolling speed is too fast, the oil film on the surface of the aluminum foil will thicken, the amount of oil on the surface of the aluminum foil will increase, and the gloss of the surface of the aluminum foil will become darker, which will cause difficulties in the annealing and degreasing process. The finish rolling speed of double zero foil is not easy to exceed 500m/min, and the pass reduction rate is also controlled at about 50%.
2.3 Physical and chemical properties of rolling oil and additives In addition to cooling and lubrication, aluminum foil rolling oil should also be able to ensure that the surface of the aluminum foil is bright, volatile during annealing, rolling to a certain reduction rate, good oxidation stability, and no unpleasant smell smell, etc. The rolling oil is generally based on mineral oil, the viscosity is (1.5 ~ 3.0) × 10-6m2/s, and the additives are higher fatty acids, higher fats and higher alcohols. The acid molecules have strong polarity and form a relatively firm adsorption film with the surface of the aluminum foil. At a higher annealing temperature, the decomposition and oxidation of the carbon chain of the oil film occurs, causing pollution of the aluminum foil and causing yellow-brown oil spots. Since the minimum concentration of oleic acid saturated adsorption is 1%, adding a small amount of oleic acid to the rolling oil can form a relatively firm chemical adsorption film on the surface of the aluminum foil. It is prone to oxidative deterioration, so it is not desirable to use it in large quantities. The control of rolling oil temperature is very important. With the increase of the rolling oil temperature, the thinning of the rolling oil may cause poor lubrication, resulting in a rapid increase in the rolling load, an increase in the rolling speed, serious oil rejection in the rolling mill, and an increase in the phenomenon of sticking to aluminum. When fatty acids are used, the generation of fine powder is faster than that of alcohol or fat. Based on this, the excessive use of oleic acid should also be limited.
3. Slitting process control
The surface oil removal quality of aluminum foil is not only related to the quality control of the rolling process and annealing process, but also related to the tightness of the slitting process. Since the aluminum foil coil is surrounded by hot air in the annealing furnace, the rolling oil between the foil layers needs to escape through a certain gap and volatilize into gas. If the aluminum foil coil is too tightly rolled, the rolling oil will evaporate. becomes difficult. In production, it is very important to control the void ratio of the double zero foil. In the slitting operation, according to different material widths, the taper tension of slitting is adjusted between 6% and 32%, and a good oil removal effect is achieved.
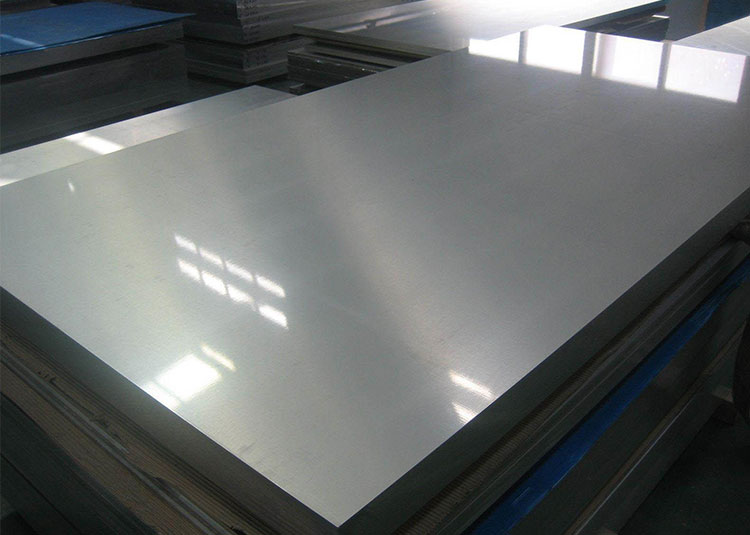
Aluminium Sheets
View Details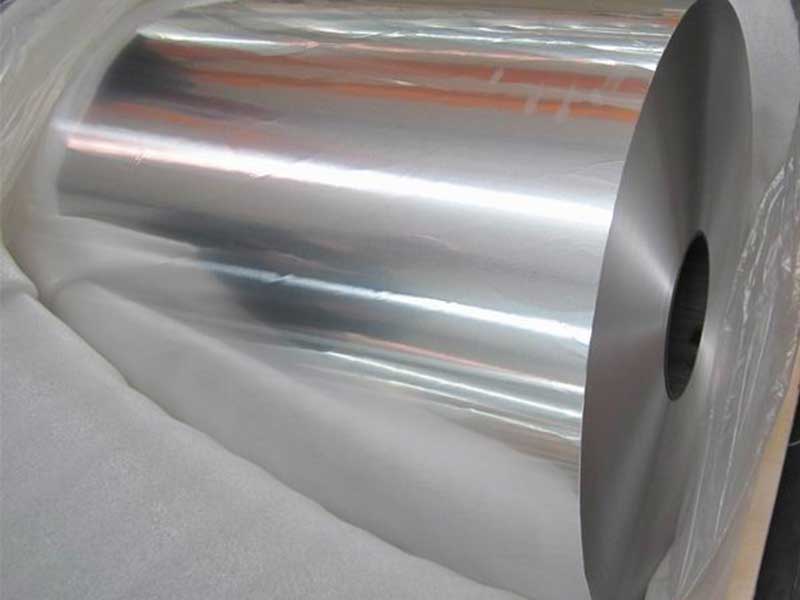
Aluminium Coils
View Details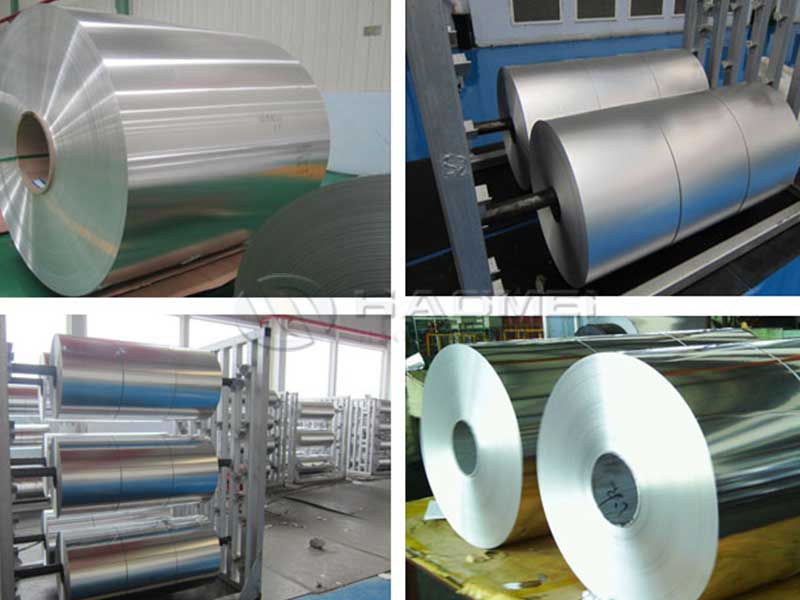
Aluminium Foils
View Details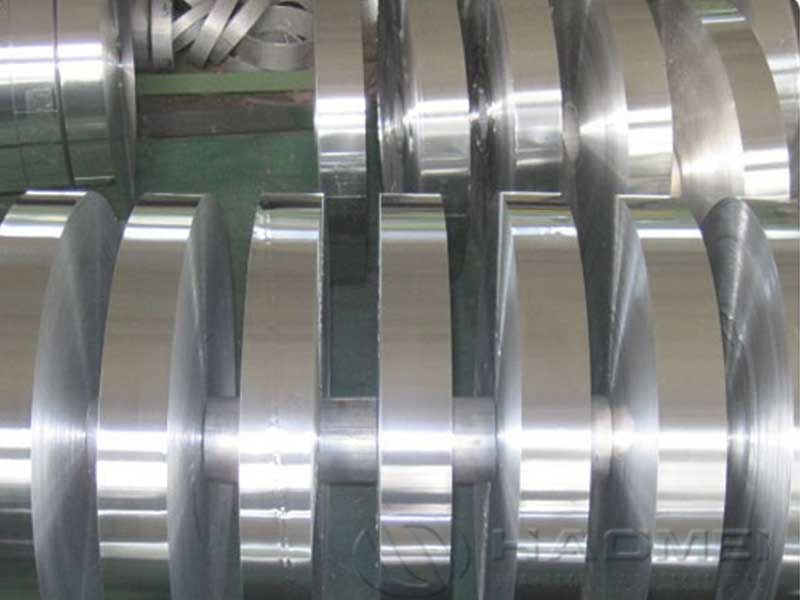
Aluminium Strips
View Details
Aluminium Circles
View Details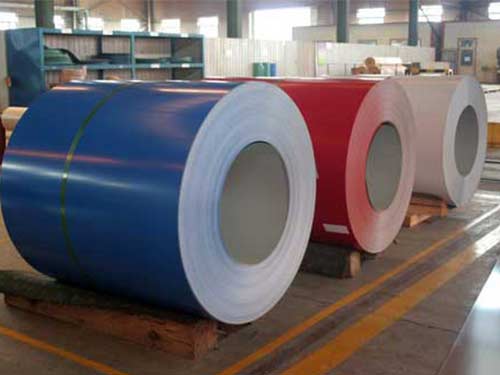
Coated Aluminium
View Details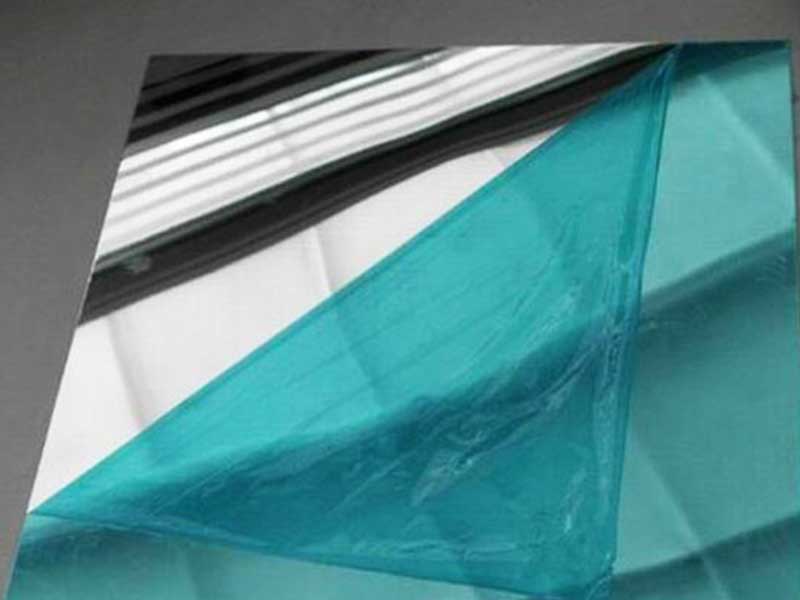
Mirror Aluminum
View Details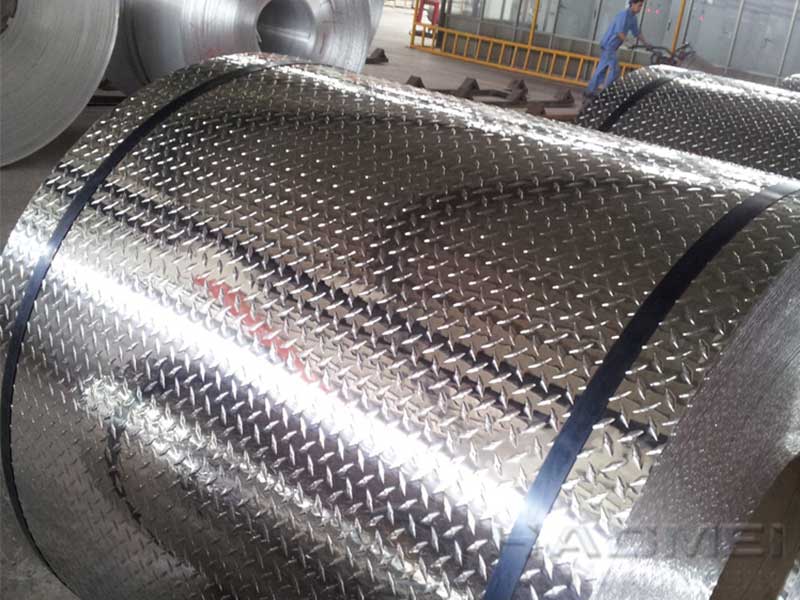
Stucco Embossed Aluminum
View DetailsAluminum
- transformer with aluminum wind...
- mirror finish aluminum sheet m...
- 6 inch round aluminum sheet
- 1060 anodized aluminum curtain...
- Extruded aluminum window frame...
- large aluminum disc
- 7022 round aluminum bar rod
- Cell Noise and Anode Rod Curre...
- 5005 h34 aluminum plate
- Insulation aluminum plate
- 6061 aluminum alloy edge strip
- 2024 -T352 ALUMINIUM SQUARE BA...
- cu al bimetal sheet
- heat resistance Electrical Alu...
- Pure aluminum plate
- what is mirror aluminum sheet
- Advantages of mirror anodized...
- Elimination of Residual Stress...
- 2618 Aluminium Block Bar
- Maintenance of aluminum insula...