5183 aluminum magnesium alloy welding wire
Typical chemical composition of 5183 aluminum-magnesium alloy welding wire: Mg 5, Cr 0.10, (Fe + Si) 0.3, Cu ≤ 0.05, Zn 0.05, Mn 0.15, Ti 0.1, AL balance.
5183 aluminum-magnesium alloy welding wire uses: bicycles, aluminum scooters and other sports equipment, locomotive compartments, chemical pressure vessels, military production, shipbuilding, aviation and other industries.
5183 aluminum welding wire should be selected from
First, the crack sensitivity of the weld metal: choosing a filler metal with a melting temperature lower than the base metal can greatly reduce the tendency of intergranular cracks in the heat affected zone. Therefore, welding wire with an alloy content higher than that of the base material is used as the filler metal, which can generally prevent weld metal cracks.
2. Joint strength: The strength of the welded joint changes with the alloy element content of the welding wire. That is, the strength of weld joints of non-heat-treated alloys increases in the order of 1000 series, 4000 series, and 5000 series.
3. Color difference after anodizing treatment: In order to improve the corrosion resistance, anodizing treatment is often performed after welding. If the composition of the weld metal is ficantly different from the base metal, or the casting structure of the weld metal is different from the rolled structure of the base metal, Weld metal produces chromatic aberration after anodizing.
4. Mechanical properties and corrosion resistance of joints under high temperature: 5000 series welding wires (5654, 5356, 5556, 5183) containing more than 3% magnesium should be avoided in structures with a temperature above 65 degrees Celsius, because these alloys have stress corrosion Cracks are sensitive and stress corrosion cracking can occur in the above temperature and corrosive environment.
5. Workability of joints: Welded joints that require bending, generally workability is affected by plasticity, and plasticity decreases with increasing strength
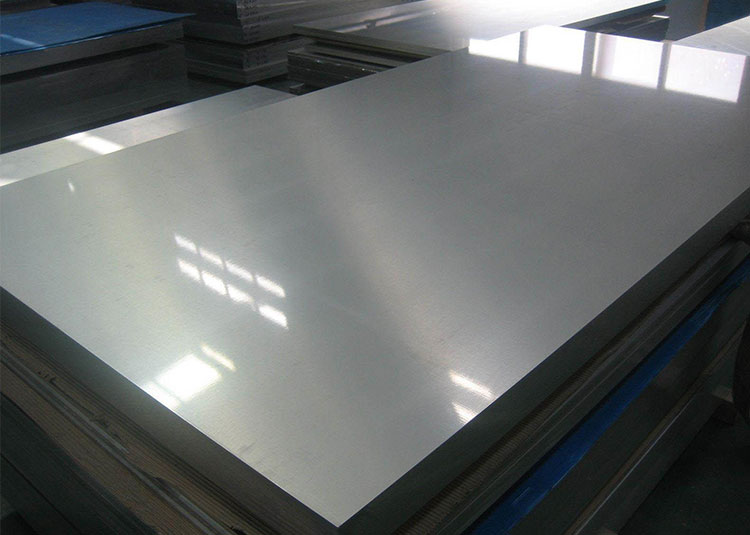
Aluminium Sheets
View Details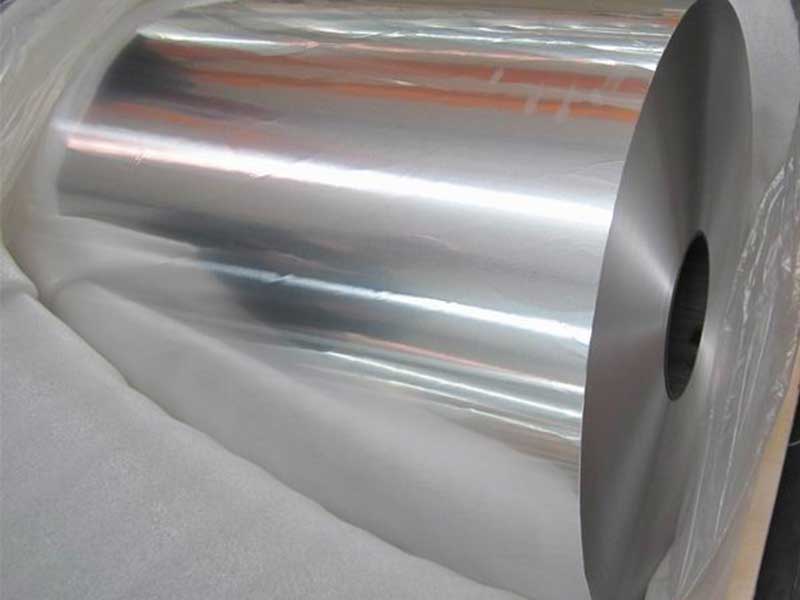
Aluminium Coils
View Details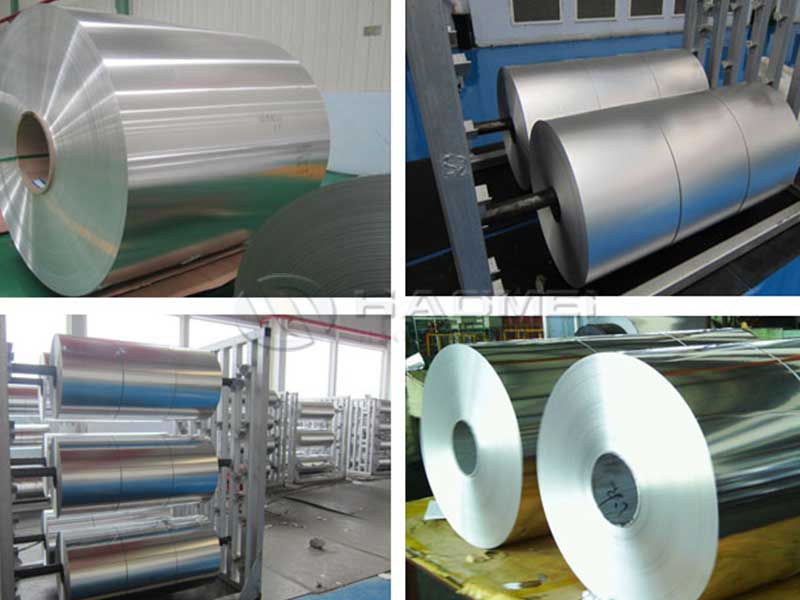
Aluminium Foils
View Details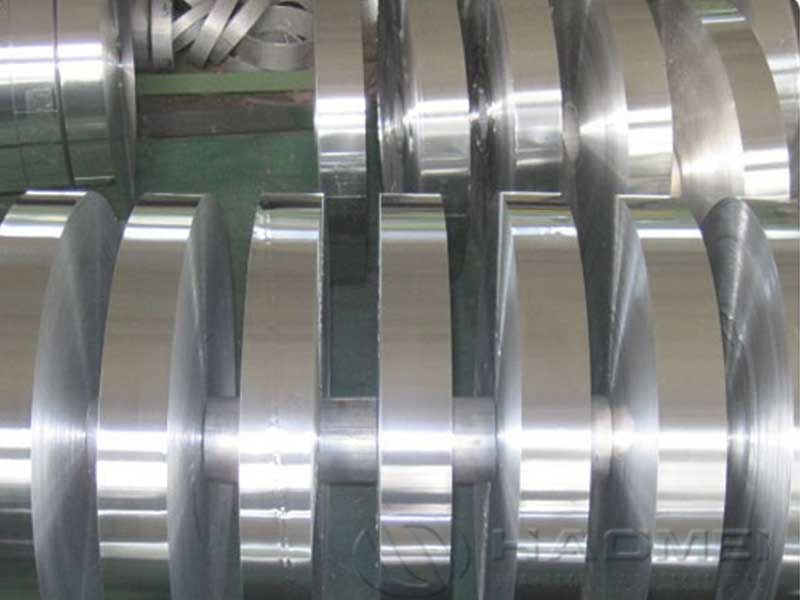
Aluminium Strips
View Details
Aluminium Circles
View Details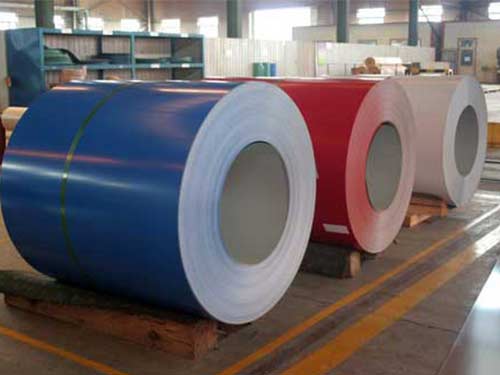
Coated Aluminium
View Details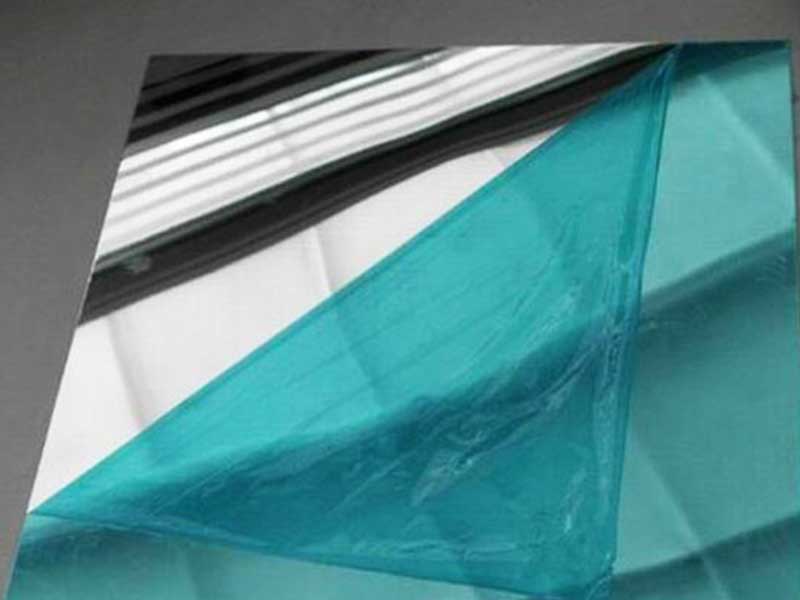
Mirror Aluminum
View Details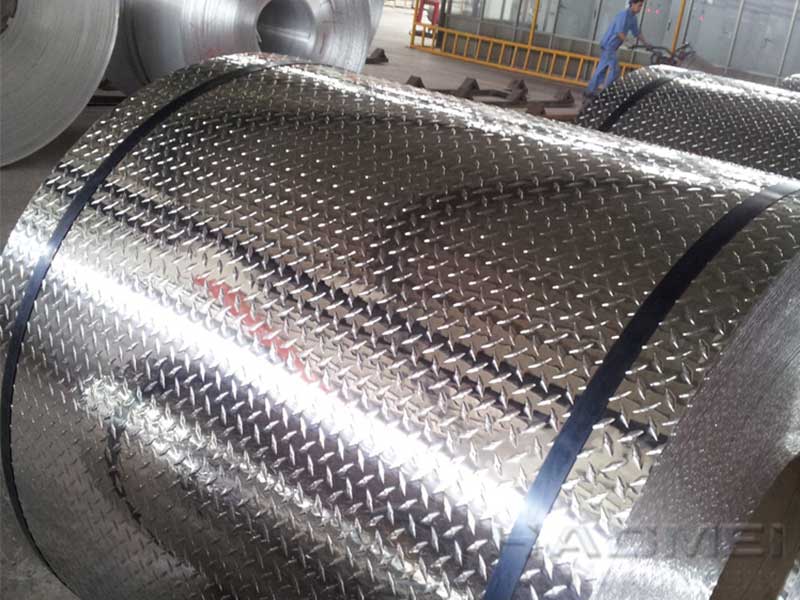
Stucco Embossed Aluminum
View DetailsAluminum
- aluminium frame manufacturers
- Aluminum Sign Blanks Sheet
- metal aluminum jacketing
- Stucco Embossed Aluminum Sheet
- 6618 T8 Pb-free free -cutting...
- Aluminum Conductor in Resin Ca...
- 5 Bar 5754 Aluminum Tread Chec...
- Main Characteristics of Alumin...
- large aluminum disc
- 6061 aluminum block
- Brief Introduction of 2014 alu...
- Stamping drawing aluminum disc
- 2618 Aluminium Block Bar
- Aluminum alloy plate in civil...
- 1060 Aluminum Sheet
- Common aluminum plate surface...
- The Development Process of Med...
- Brush aluminum plastic composi...
- Mirror finish aluminum sheet p...
- 8000 Series Aluminium coil (80...