The difference between aluminum alloy hard anodizing and ordi
1. The surface hardness of aluminum alloy after hard oxidation is up to HV500.
2. The thickness of the oxide film is 25-250 um.
3. Strong adhesion, according to the oxidation characteristics of hard oxidation: 50% of the oxide film formed penetrates into the aluminum alloy, and 50% adheres to the surface of the aluminum alloy (bidirectional growth).
4, good insulation: breakdown voltage up to 2000V (perfect sealing).
5. Good wear resistance: For aluminum alloys containing less than 2% copper, the maximum wear index is 3.5mg/1000 rpm. All other alloy wear indexes should not exceed 1.5 mg/1000 rpm.
6. Non-toxic: The oxide film and the electrochemical process used to produce the anodized film are harmless to the human body.
Therefore, in order to reduce the weight of the product, the convenience of machining, the environmental protection and low toxicity, some parts of the current products are replaced by aluminum alloy hard oxidized instead of stainless steel and electroplated hard chrome.
Second, the difference between aluminum alloy hard anodizing and ordinary anodizing:
50% of the hard oxidized oxide film penetrates into the interior of the aluminum alloy, and 50% adheres to the surface of the aluminum alloy. Therefore, the outer dimensions of the product become larger after the hard oxidation, and the inner pores become smaller.
(1) Differences in operating conditions:
1, the temperature is different: ordinary oxidation 18-22 ° C or so, there are additives can go to 30 ° C, the temperature is too high, easy to appear powder or crack; hard oxidation is generally below 5 ° C, relatively speaking, the lower the temperature, the higher the hardness.
2, the difference in concentration: ordinary oxidation is generally about 20%; hard oxidation is generally 15% or lower.
3, current / voltage difference: ordinary oxidation current density is generally: 1-1.5A / dm2; and hard oxidation: 1.5-5A / dm2; ordinary oxidation voltage ≤ 18V, hard oxidation sometimes as high as 120V.
(2) Differences in film properties:
1. Thickness of the film: The thickness of the common oxide film is relatively thin; the thickness of the hard oxide is generally >15μm, which is too low to meet the requirement of hardness ≥300HV.
2. Surface state: The ordinary oxidized surface is smooth, while the hard oxidized surface is rough (microscopic, related to the surface roughness of the substrate).
3. Porosity is different: ordinary oxidized porosity is high; and hard oxidized porosity is low.
4. Ordinary oxidation is basically a transparent film; hard oxidation is an opaque film due to film thickness.
5. Applicable occasions: ordinary oxidation is suitable for decoration; while hard oxidation is mainly used for function, generally used for wear-resistant and electric-resistant occasions.
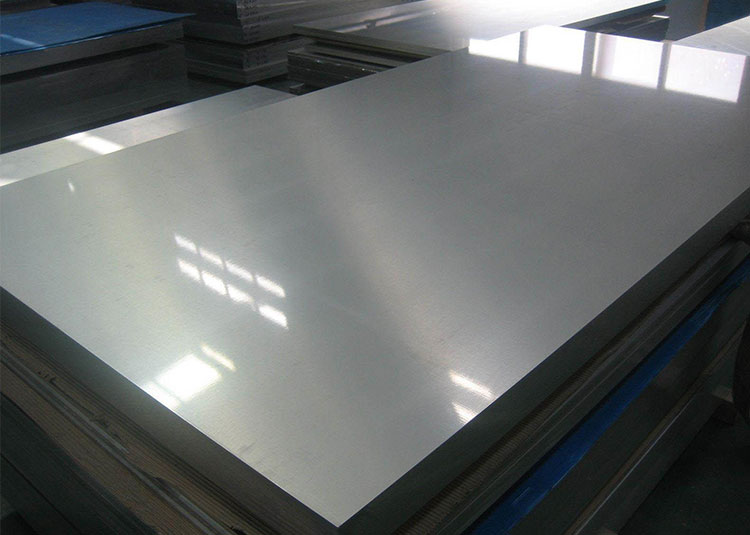
Aluminium Sheets
View Details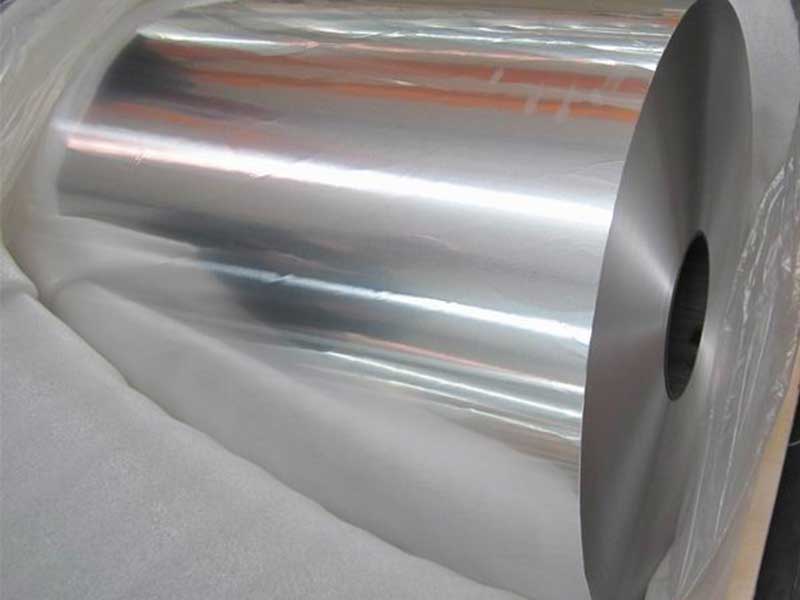
Aluminium Coils
View Details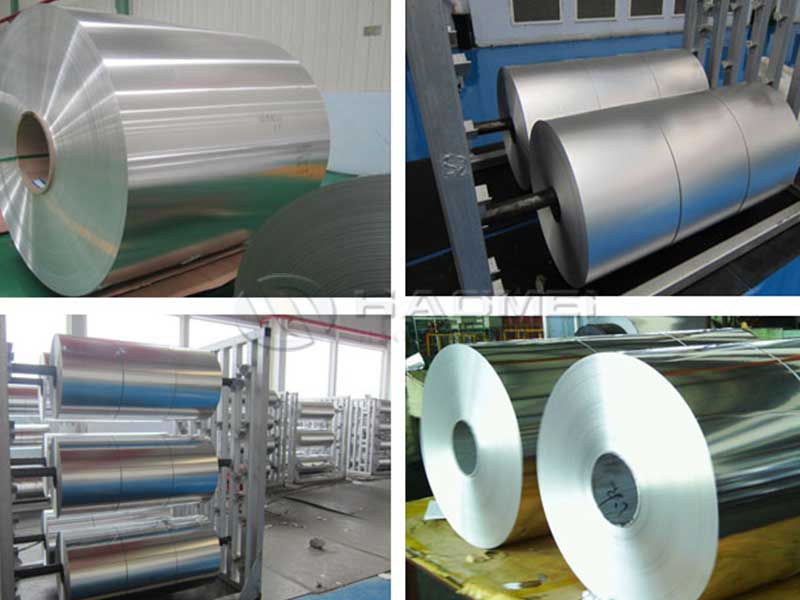
Aluminium Foils
View Details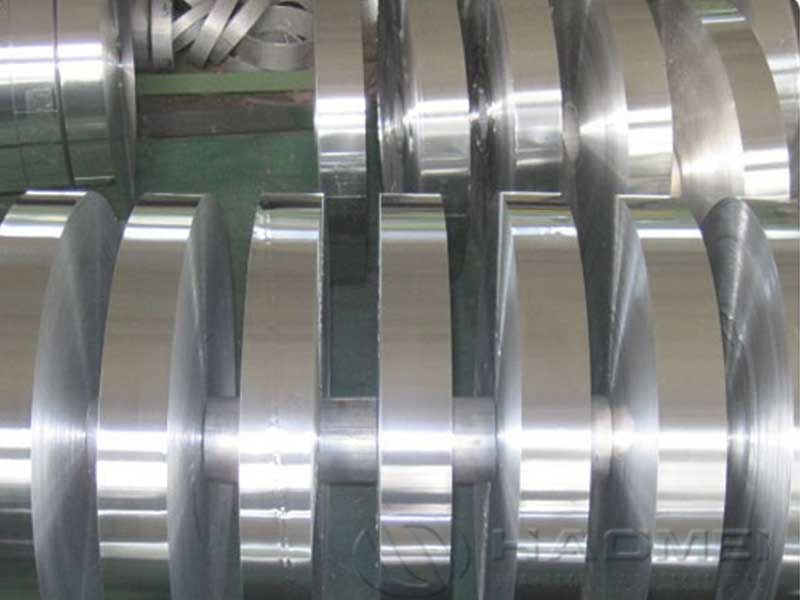
Aluminium Strips
View Details
Aluminium Circles
View Details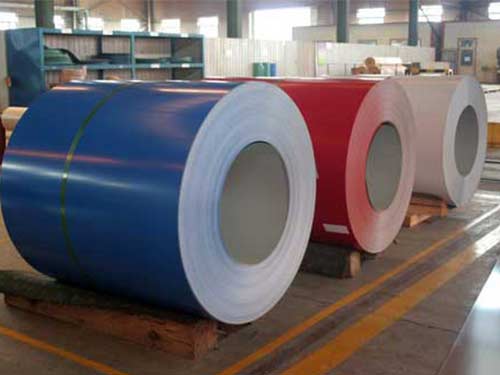
Coated Aluminium
View Details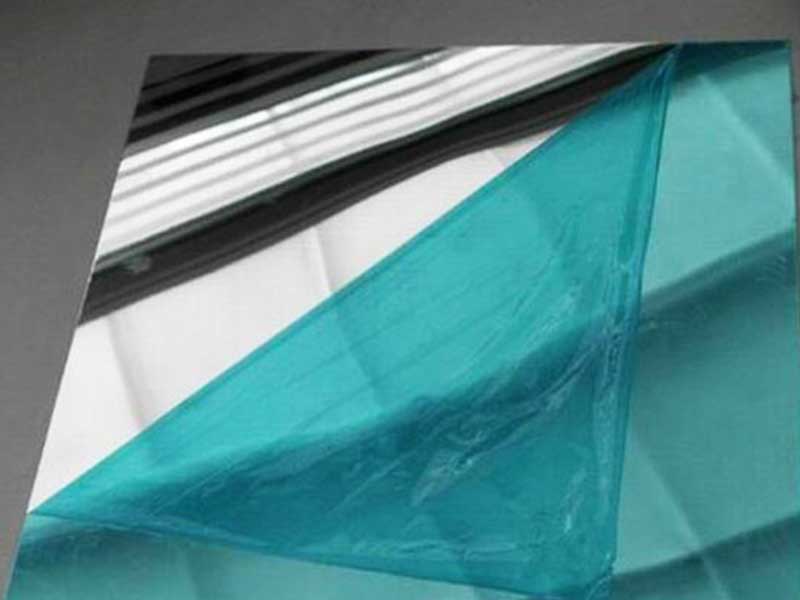
Mirror Aluminum
View Details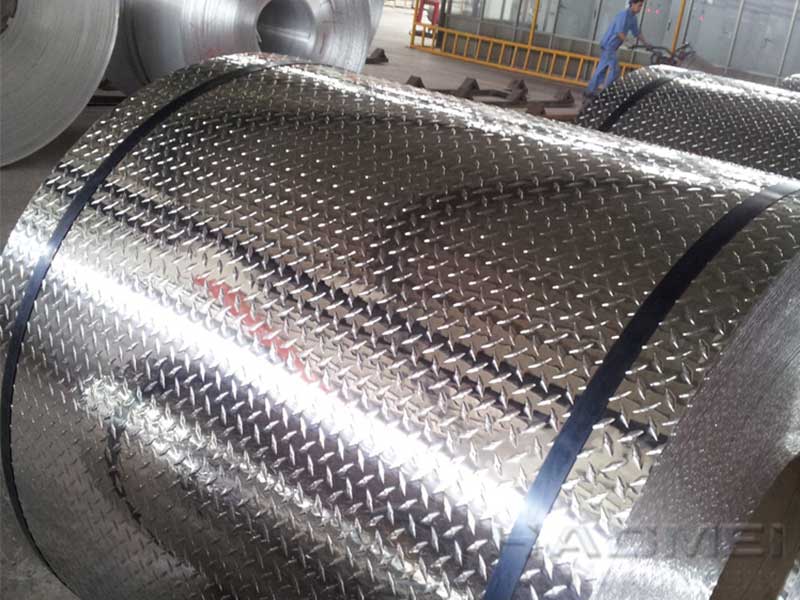
Stucco Embossed Aluminum
View DetailsAluminum
- aluminum profile for sliding d...
- 6000 Series Aluminum Plate,606...
- reflective aluminum sheet for...
- Corrosion Resistant Aluminum r...
- How to choose aluminum roll ja...
- metal jacket pipe insulation
- 5754 Aluminum Sign Blanks Shee...
- Aluminium foil for medicine me...
- aluminum honeycomb core foil
- Fireproof material Anodized al...
- 1100 Aluminum Sign Blanks Shee...
- 8 Series Alloy Aluminum Wire
- 5005 Aluminum plate
- Titanium aluminum explosive we...
- Aluminum circle alloy 4006
- PP CAP Aluminum Foil
- 1060 1100 Color Coated Alumini...
- Colour coated aluminum coils f...
- Aluminium strip for transforme...
- Stucco Embossed Finish Coated...