Application of copper aluminum bus bar in low voltage equipment
In low-voltage complete sets of equipment, the main requirements for current carrying conductor are its current carrying capacity and mechanical strength. The specific assessment indicators are temperature rise and the ability to withstand short-circuit current. For the composite material, the interface bonding strength of the two materials must be ensured, and there is no delamination during the processing of shear, punching and bending processes. At the same time, it must be ensured that the composite material can withstand the stress generated by thermal expansion and cold contraction. In addition to meeting the temperature rise limit and dynamic thermal stability, the interface bonding strength between copper and aluminum must also meet the requirements of punching, bending and overcoming the stress caused by thermal expansion and cold contraction. The interface bonding strength is directly related to its manufacturing process. The interfacial bonding strength is different with different manufacturing methods.
The bonding strength of copper aluminum composite interface is the core key parameter of copper aluminum bus bar, which should be greater than the specified value of DL / t247 standard (35MPa). If it is less than the specified value, the stress generated by thermal expansion and cold contraction will destroy the bonding of copper aluminum interface, resulting in electrochemical corrosion. There are serious hidden troubles in operation, breakdown and short circuit, and even electrical fire. The volume ratio of copper layer is the key parameter of copper aluminum composite bar. In copper aluminum bus bar, the thicker the copper layer, the higher the conductivity, the greater the processing difficulty and the higher the cost. When it exceeds a certain thickness, the conductivity does not increase much, but the cost increases greatly. The electric power industry standard DL / t247 gives a volume ratio of 20%. When it reaches 20%, its current carrying capacity reaches 86% of T2 copper bar. If it is less than the standard value, it will reduce the current carrying capacity, increase the temperature rise of the complete set of electrical equipment, increase energy consumption and affect the use safety of the equipment. The interface bonding strength and the section ratio of copper layer determine the performance parameters of copper aluminum composite bus, which are the two key parameters of copper aluminum composite bus.
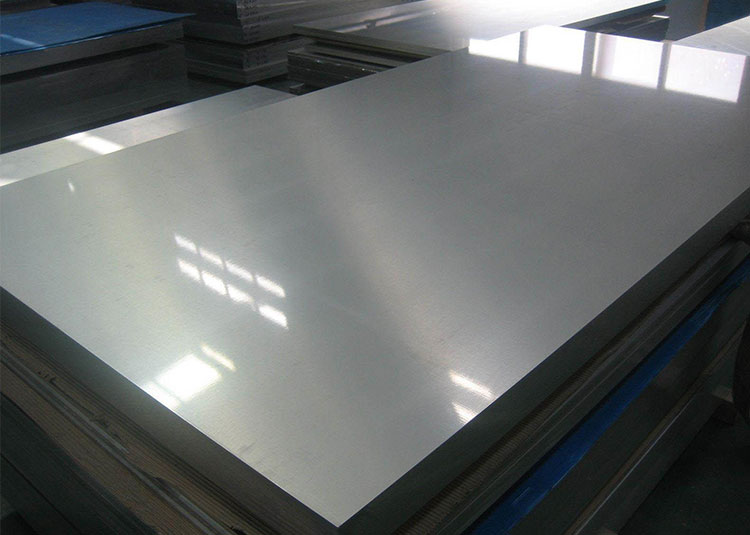
Aluminium Sheets
View Details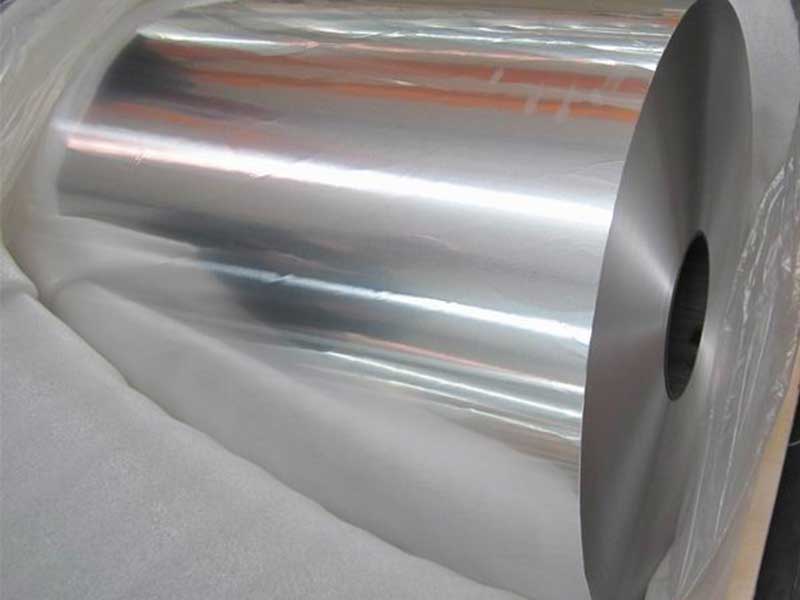
Aluminium Coils
View Details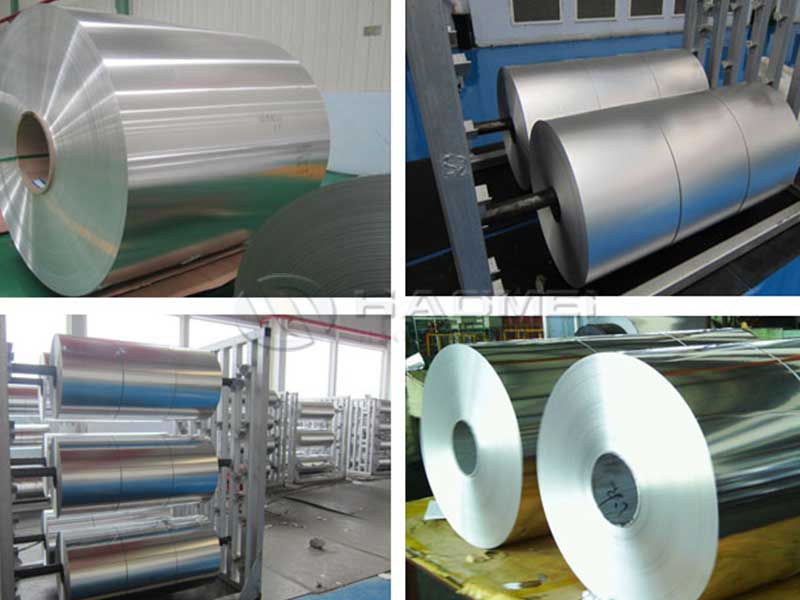
Aluminium Foils
View Details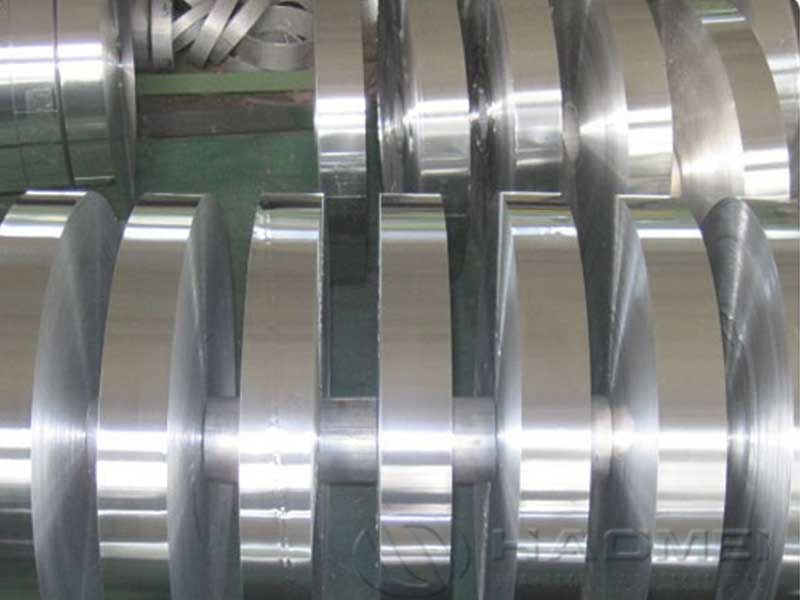
Aluminium Strips
View Details
Aluminium Circles
View Details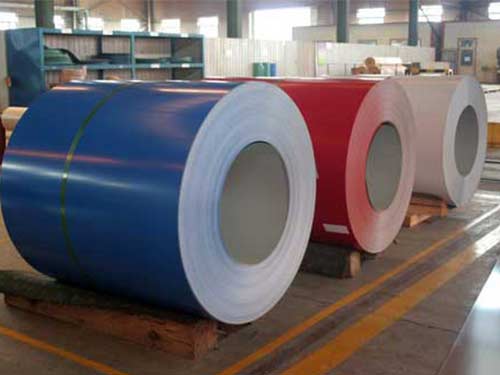
Coated Aluminium
View Details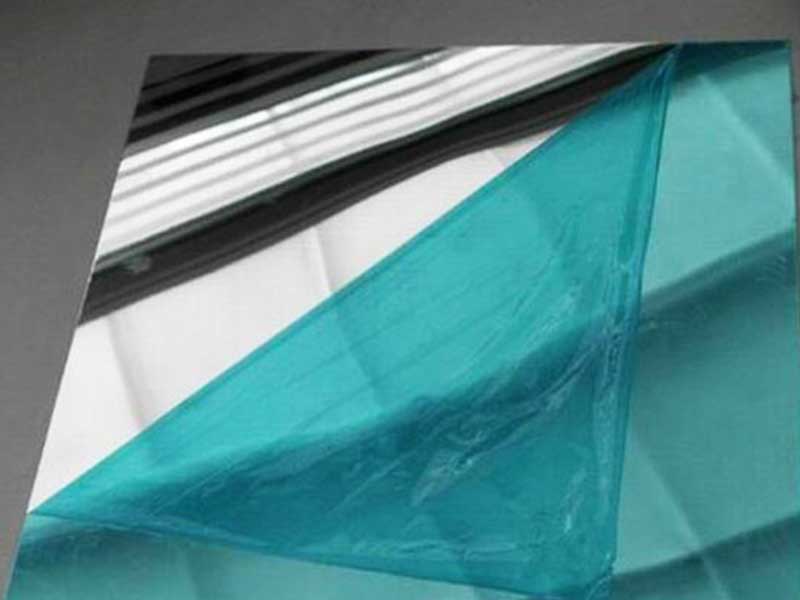
Mirror Aluminum
View Details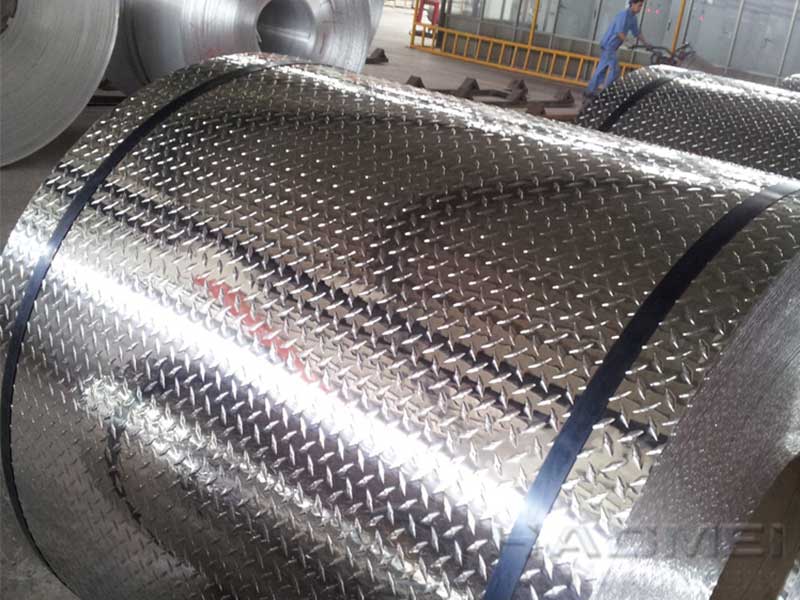
Stucco Embossed Aluminum
View DetailsCopper
- Copper clad aluminum coil shee...
- high conductivity c1100 copper...
- copper cladding sheets
- copper aluminum bimetallic tra...
- AgCu silver copper bimetal str...
- copper-alu-copper clad tree-la...
- Copper clad aluminum enamelled...
- Aluminum Copper Bimetal Connec...
- Energy-saving copper - aluminu...
- Copper-aluminum composite radi...
- copper-aluminium bimetal clad...
- Copper clad aluminum sheet for...
- Copper braided wire soft conne...
- Copper Composite Shingle Wall...
- titanium clad copper rod bar
- which winding is better copper...
- Tinned Copper Braid Wire Strip...
- Copper and aluminum busbar’s r...
- Copper-aluminum composite radi...
- Energy-saving copper - aluminu...