aluminum stainless steel connector for cryogenic equipment
In 2009, it clearly stated that "hydrogen energy and fuel cells" should be regarded as a strategic focus. In the storage and transportation of the hydrogen industry chain, a large number of hydrogen storage tanks need to be used. In order to reduce the weight of the tank, the hydrogen storage tank adopts a double-layer design.
The outside of the body is made of stainless steel to ensure strength, and the inside of the tank is made of aluminum alloy to store gas or liquid hydrogen. The storage conditions are low temperature and high pressure. The inside and outside of the tank are connected by aluminum stainless steel connectors.
The service temperature of the high-performance aluminum stainless steel connector for liquid hydrogen storage tank is -269 ℃, and the aluminum end and stainless steel end are welded to the inside and outside of the storage tank respectively during use. The welding allowable temperature of the commonly used aluminum stainless steel connector is not higher than 350 °C. In order to ensure the reliability of the transition joint under actual working conditions, it is necessary to add aluminum, titanium and nickel as the transition layer in the design to control the oxide at the composite interface. And the generation of defects, the bonding interface is in a controllable state.
(1) The interface size and defect control of the aluminum/stainless steel five-layer composite plate with a width of 600 mm × 600 mm have reached an ideal state. Under the service condition of -269 °C, the pull-off strength is about 300. MPa, the leak rate of the airtightness of the connector is <1×10-9Pa·m3/s.
(2) The main risk point affecting the air tightness of the aluminum/stainless steel joint is the 5052/1060 interface. The ideal size of the interface ripple is: the wavelength is 2000 μm, the amplitude is 640 μm, and the wave amplitude ratio is 0.32.
(3) The airtightness of the aluminum/stainless steel connector exceeds the standard due to obvious microscopic cracks at the 5052/1060 interface. Such defects can be found at the interface after PT inspection.
(4) During the welding process of aluminum stainless steel connectors for low-temperature equipment, the interface temperature should be controlled below 350 °C, and the welding temperature should be further strictly controlled in practical applications.
(5) At present, the aluminum stainless steel connector for cryogenic equipment developed by Aluminum can basically meet the needs of localization. However, considering the further reduction of production costs and improvement of raw material utilization, the process plan of such products still needs to be subject to subsequent process optimization.
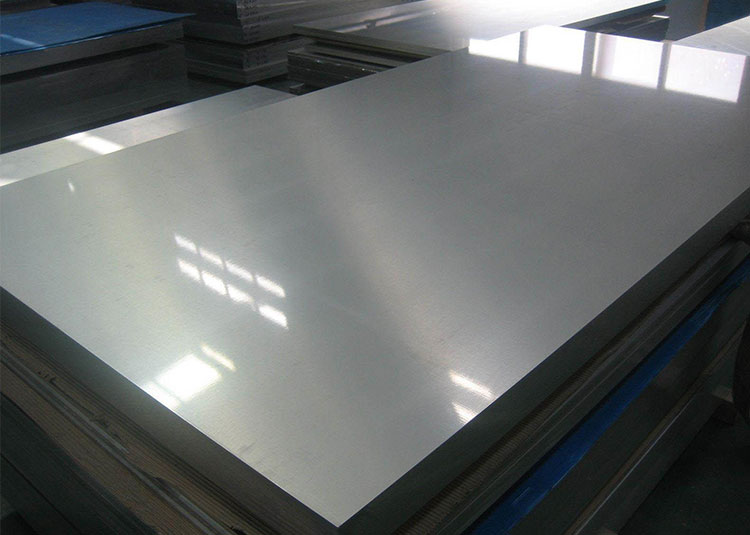
Aluminium Sheets
View Details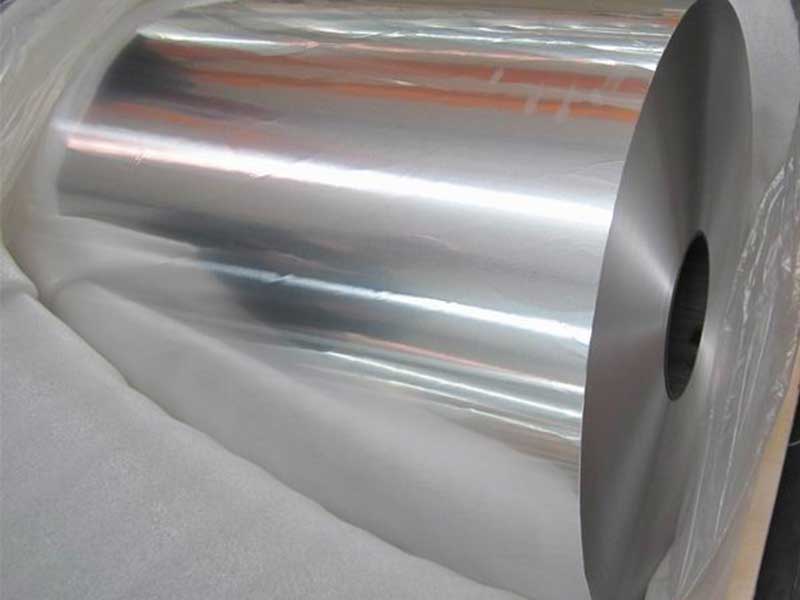
Aluminium Coils
View Details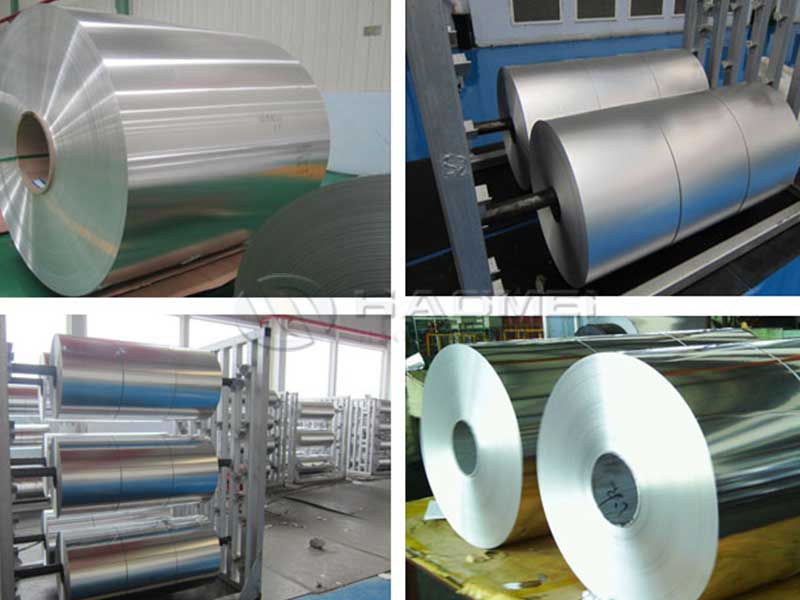
Aluminium Foils
View Details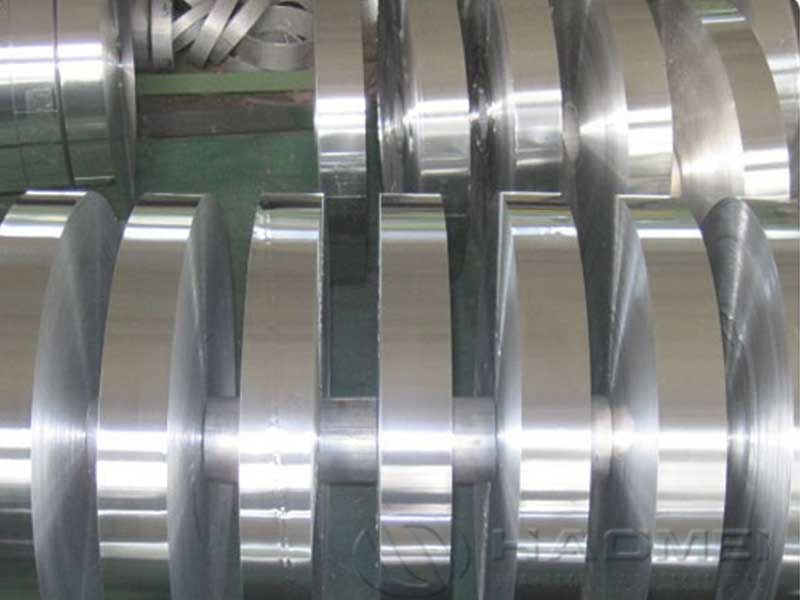
Aluminium Strips
View Details
Aluminium Circles
View Details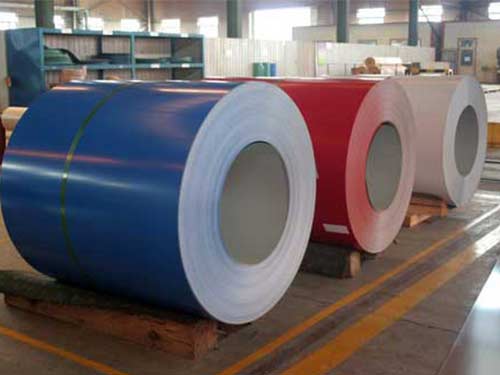
Coated Aluminium
View Details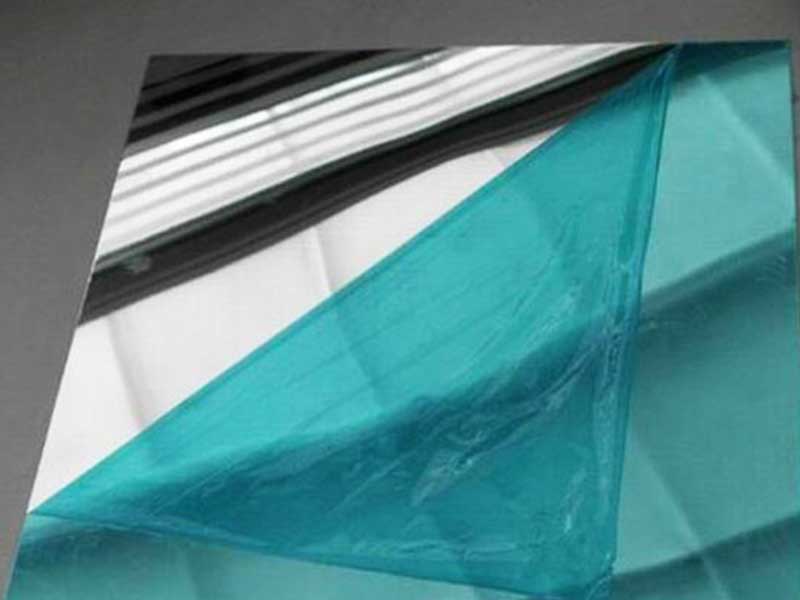
Mirror Aluminum
View Details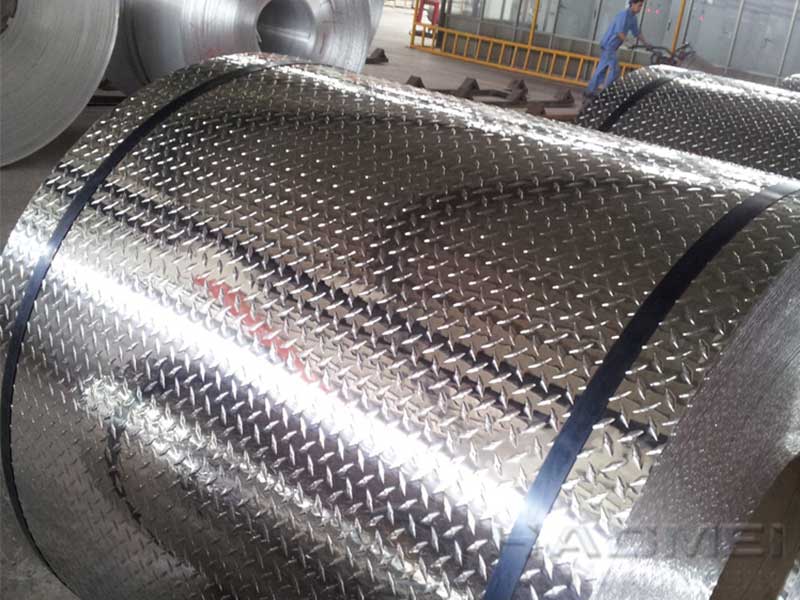
Stucco Embossed Aluminum
View DetailsSteel
- Copper clad stainless steel pl...
- Copper steel explosion bonded...
- Explosion welding aluminum ste...
- Brass copper clad steel sheet...
- explosion welding aluminum ste...
- Stainless steel clad plate
- Titanium aluminum stainless st...
- Copper clad steel plate for co...
- Explosion welding titanium ste...
- Copper-steel clad sheet plate
- Characteristics of explosive c...
- Aluminimun and steel bi metal...
- aluminum clad steel coil strip
- aluminum stainless steel conne...
- Research on Effect of Steel Sh...
- Steel Yokes Bracket for Anode...
- stainless steel clad copper ba...
- Why is the anode steel claw re...
- Application of anode steel cla...
- Titanium aluminum steel clad p...