aluminum clad steel plate
M. Soltan Ali Nezhad prepared a aluminum clad steel plate with an initial total thickness of 1.9mm. The peeling experiment showed that the best bonding strength reached the strength of the aluminum matrix. The influence of deformation and temperature on the bonding strength of the interface is analyzed, and it is pointed out that the influence of deformation on the bonding strength of the interface is greater than that of the rolling temperature. Yin Lin et al. used A3030 aluminum alloy (4mm) and SUS304 stainless steel (1.2mm) to prepare aluminum clad steel plate by hot rolling. They mainly studied the effects of rolling parameters on bonding properties and the effects of interfacial compounds at different annealing temperatures and times. Growth behavior. HR Akramifard et al. prepared an Al/304L/Al three-layer aluminum clad steel plate by cold rolling using a steel plate with an initial thickness of 1.2mm and an aluminum plate with a thickness of 1mm. The reduction rate is
10% or less.
When the reduction rate is 38%, the bonding strength between the aluminum clad steel plate has reached the strength of the aluminum matrix. The bonding mechanism between steel/aluminum composite panels is that fresh metal at the interface is extruded from the cracks and embedded in the steel matrix. During the heat treatment process, it was found that the interface formed an intermediate layer composed of Al13Fe4, Fe C and Al8Si C7, and the formation of the intermediate layer reduced the bonding strength between the aluminum clad steel plate. On the basis of the initial total thickness of 2mm, Li Minquan et al. used the bending method to explore the influence of rolling process parameters on the bonding strength of the interface and conducted a certain study on the deformation law of the two components of the composite plate. The Xiao Hong team of Yanshan University used induction heating to heat the steel plate to above its recrystallization temperature and prepared an aluminum clad steel plate through the different temperature rolling method. Compared with cold-rolled composites that require a single-pass reduction ratio of more than 50% to achieve a reliable combination of aluminum clad steel plate, when the reduction ratio of the different temperature rolling method is 45%, the interfacial shear strength of the composite plates is already It reaches 85MPa, which is much higher than the interface bonding strength of the aluminum clad steel plate prepared by the cold rolling method under the same reduction rate.
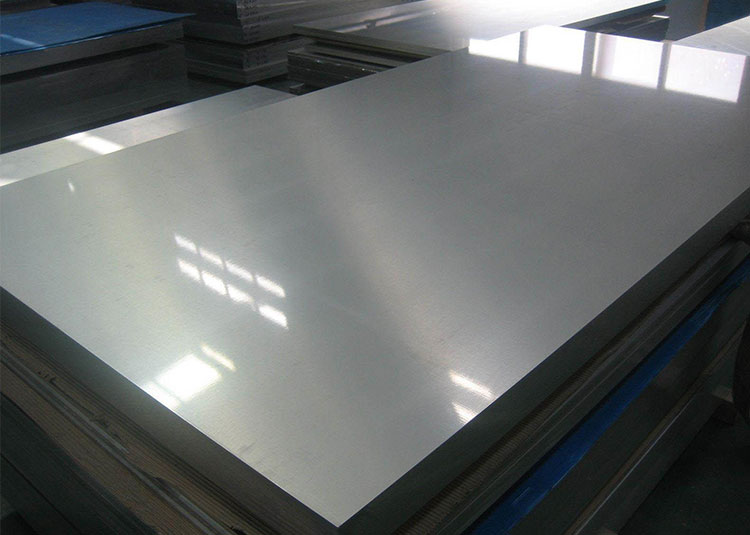
Aluminium Sheets
View Details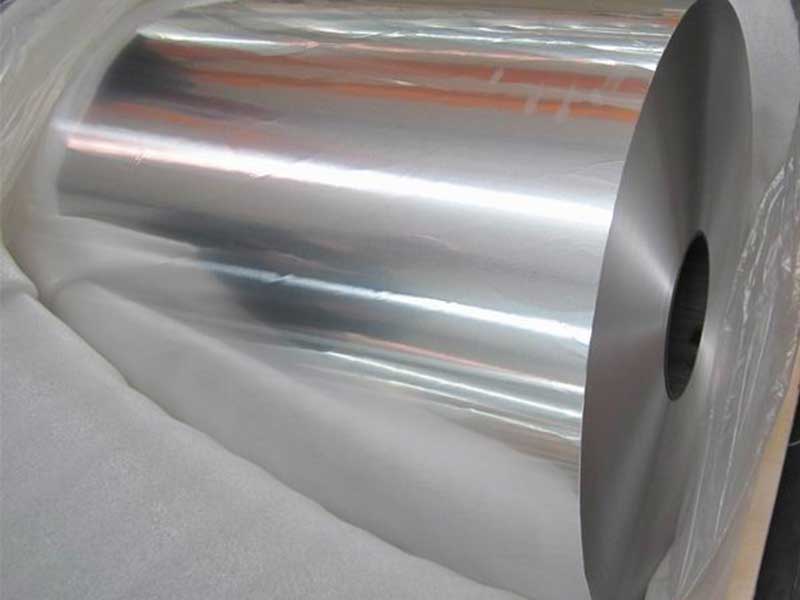
Aluminium Coils
View Details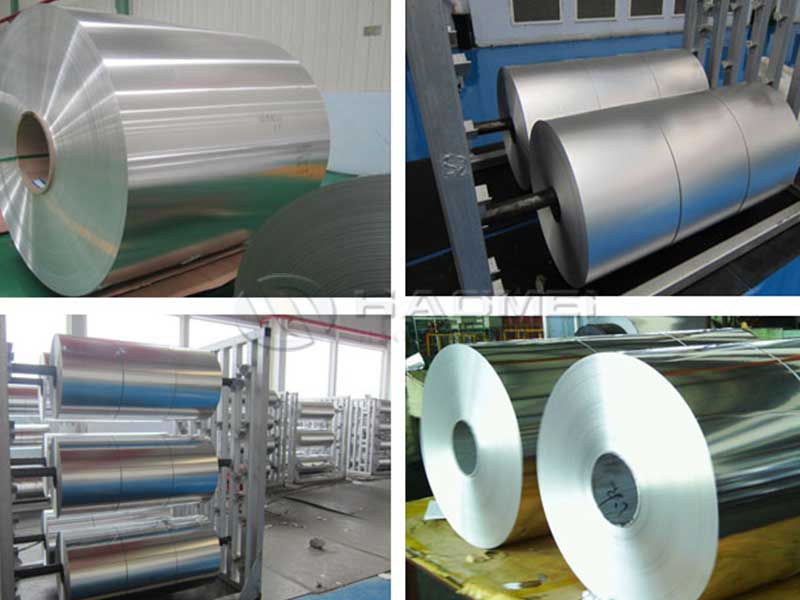
Aluminium Foils
View Details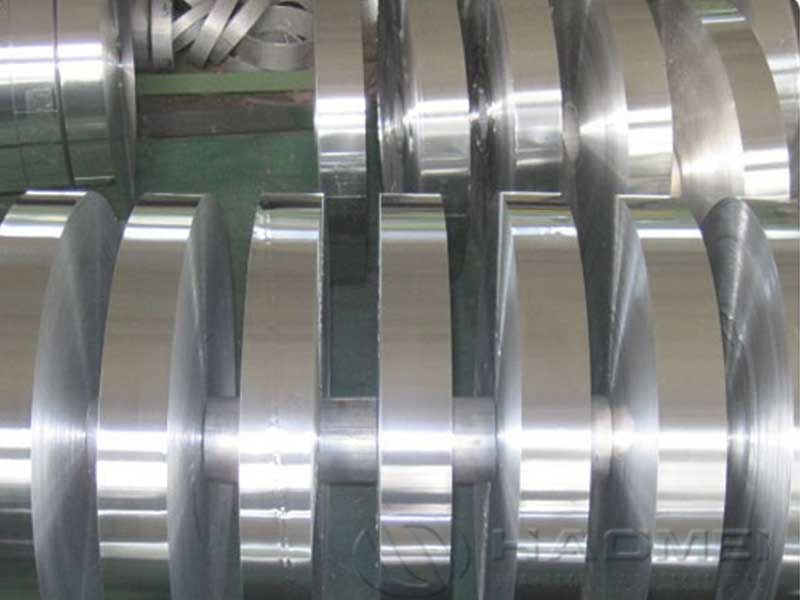
Aluminium Strips
View Details
Aluminium Circles
View Details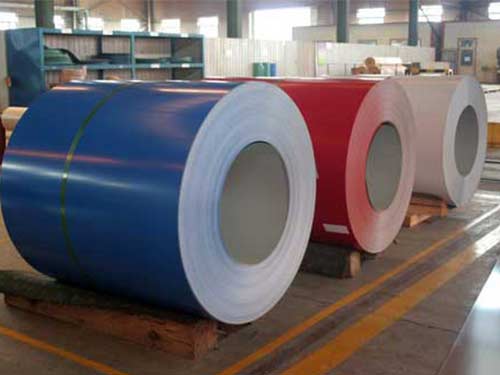
Coated Aluminium
View Details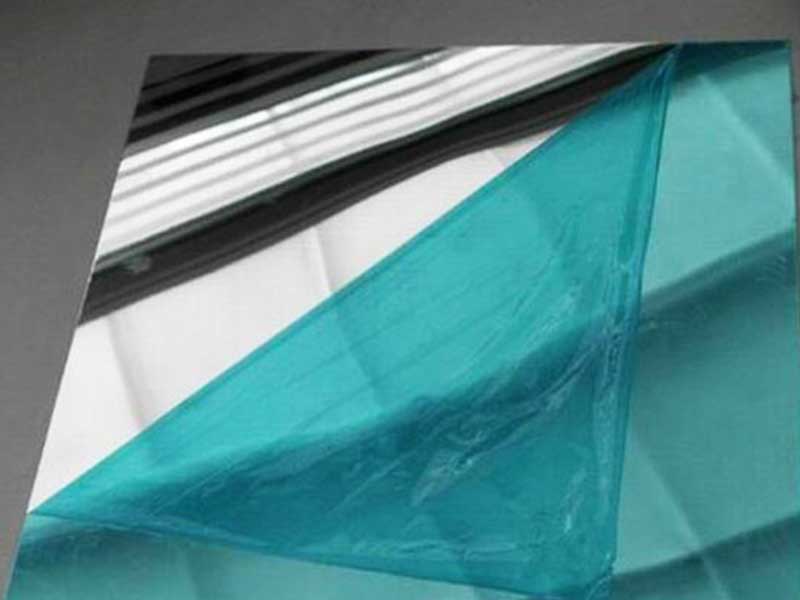
Mirror Aluminum
View Details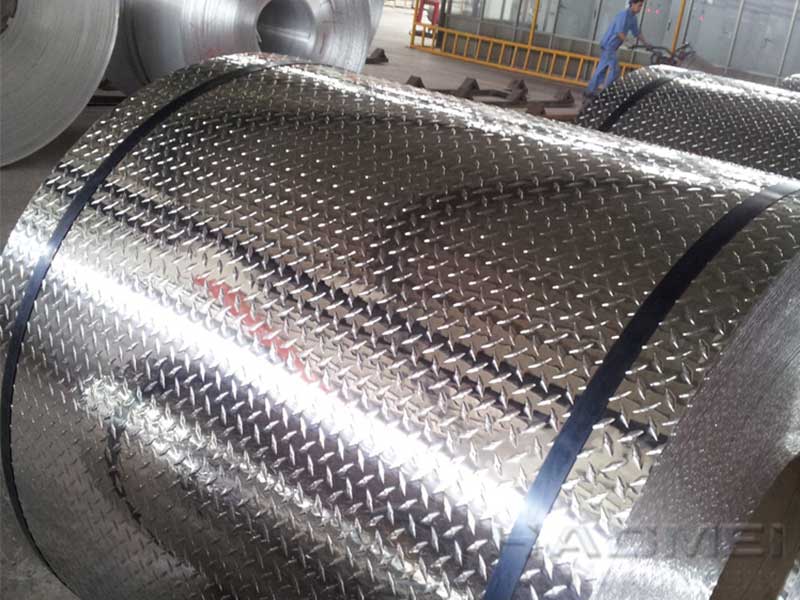
Stucco Embossed Aluminum
View DetailsSteel
- Aluminum laminated stainless...
- Explosion welding aluminum ste...
- aluminum steel bimetal coil st...
- Aluminum Clad Steel Bimetal
- 5083 SS400 aluminum steel stru...
- Brass steel bimetal coil strip
- Requirements for production of...
- aluminum steel triclad transit...
- cast steel anode yoke
- Copper steel explosion bonded...
- Stainless steel clad plate
- stainless steel copper aluminu...
- Aluminimun and steel bi metal...
- 5005A H14 imitation stainless...
- Titanium aluminum stainless st...
- aluminum stainless steel conne...
- Titanium Clad Steel Plate Shee...
- Characteristics of explosive c...
- Research on Effect of Steel Sh...
- aluminum clad steel coil strip