1090 aluminum alloy for anodizing
The main processing flow of hard 1090 aluminum alloy for anodizing needs to go through ten main links: ingot casting, ingot sawing and milling, ingot homogenization and thermal processing, ingot cold processing, plate thick material cleaning, plate intermediate heat treatment, plate mirror processing, plate tension straightening and trimming, plate cleaning and coating, plate anodizing, etc. However, in terms of technical difficulty, the four links before mirror processing, such as plate ingot casting, plate ingot hot processing, plate ingot cold processing and intermediate heat treatment, are the core technologies of the whole industry, and these four links still have an internal relationship of mutual restriction and balance. Specifically, the typical technical route of hard 1090 products for anodizing is as follows:
Slab ingot casting slab ingot sawing and milling panel ingot homogenization hot milk cold milk intermediate annealing mirror milk stretch straightening cutting edge cleaning coated anodized finished product
The processing flow of soft 1090 aluminum alloy for anodizing products is different from that of hard products to a certain extent due to the obvious differences in use and usage. The most typical processing flow mainly includes: slab ingot casting, slab ingot sawing and milling, slab ingot hooking and hot processing, slab ingot cold processing, coil cleaning, coil annealing, coil opening, plate stamping The nine major links such as anodizing, the technical core of the whole industry, are still concentrated in several core links such as plate and ingot casting, plate and ingot homogenization and thermal processing, and plate and ingot surface treatment. Specifically, The typical technical route of soft 1090 aluminum alloy products for anodizing is as follows: plate ingot casting, plate ingot sawing and milling, panel ingot homogenization, hot emulsion cold emulsion cleaning, annealing, plate opening, stamping (or spinning) to form anodized products
The 1090 aluminum alloy for anodizing product has two very clear technical indicators, namely, high reflectance (known as brightness in the industry and characterized by mutually opposite specular reflectance and diffuse reflectance) and shading that does not affect the uniformity of reflectance after anodizing. The factors affecting the reflectance are mainly concentrated in five aspects: the grain size of plate ingot, the purity of plate ingot aluminum, the uniformity and density of oxide film after oxidation, the uniformity and consistency of rough surface and the control of interface state of mirror processing; The main factors affecting shading defects are concentrated in three aspects: surface and interface uniformity, raw material surface cleanliness and interface state control accuracy during mirror processing. The interface state control accuracy during mirror processing is concentrated in three technical indexes that affect and balance each other: absolute reduction control, plate type control and lubrication state control.
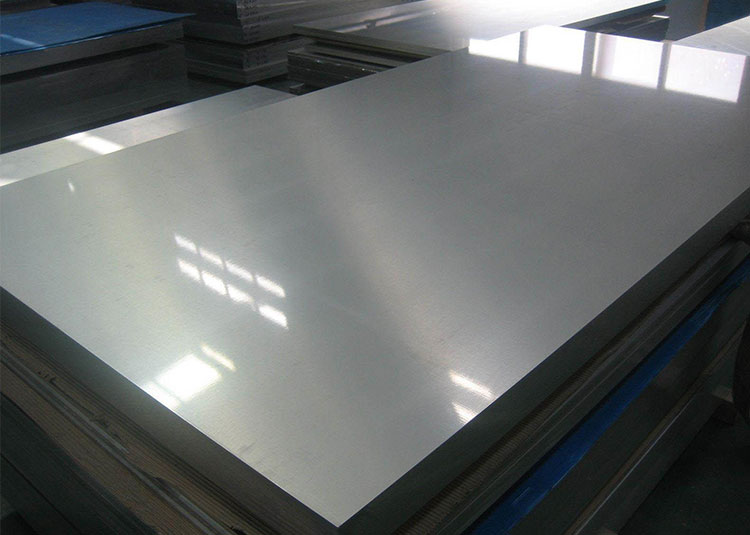
Aluminium Sheets
View Details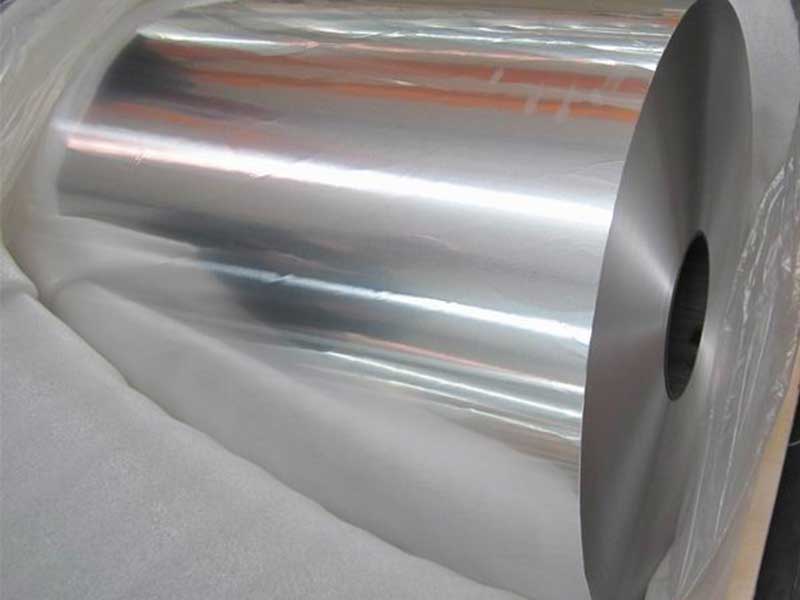
Aluminium Coils
View Details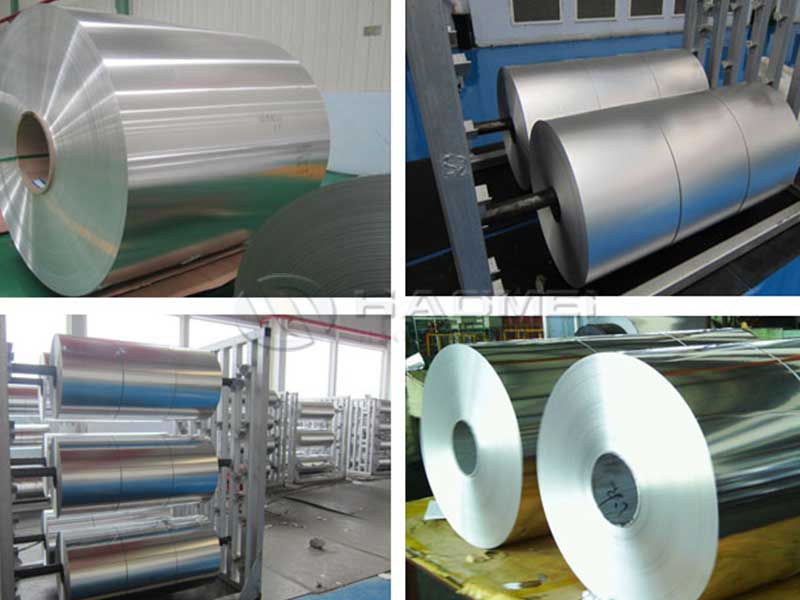
Aluminium Foils
View Details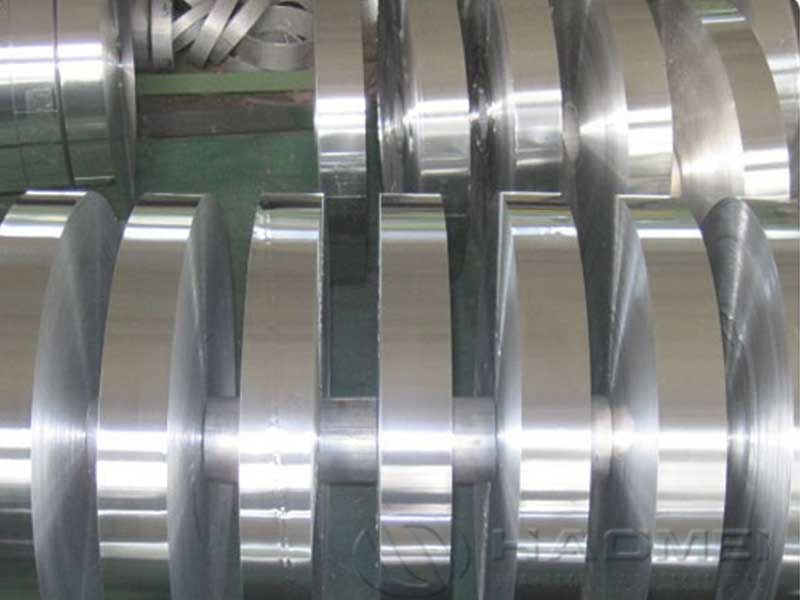
Aluminium Strips
View Details
Aluminium Circles
View Details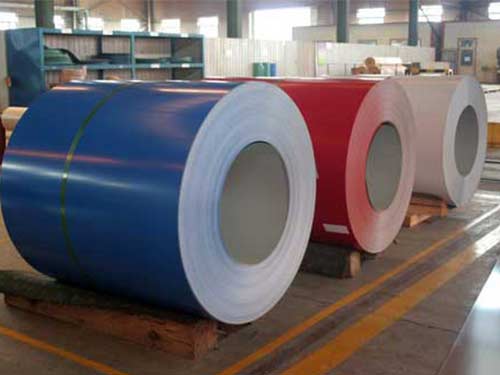
Coated Aluminium
View Details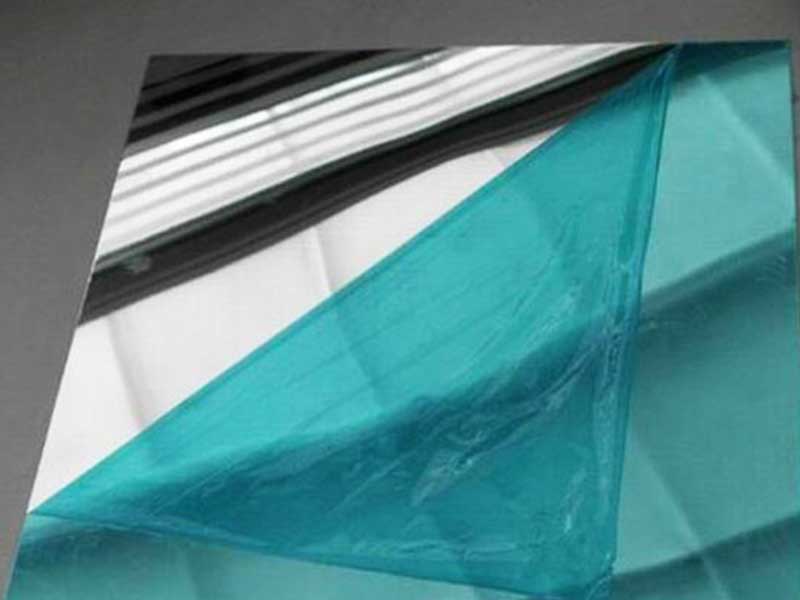
Mirror Aluminum
View Details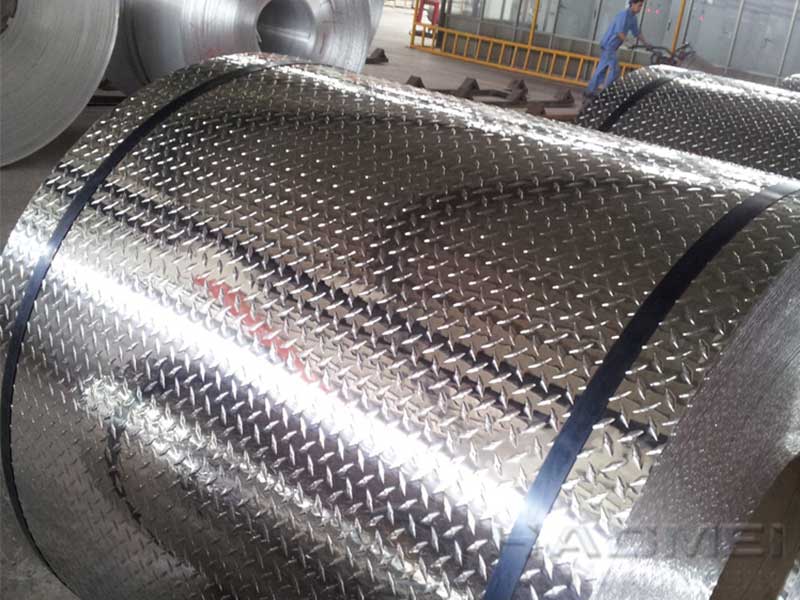
Stucco Embossed Aluminum
View DetailsAluminum
- Mirror quality anodized alumin...
- Aluminum insulation coil jacke...
- 3003 Aluminum Circle/Aluminium...
- aluminum foil for hair colorin...
- Deep blanking material
- Aluminum Chrome Phosphate Tech...
- Aluminum Disc with hole
- 1050 1060 1100 3003 Aluminum c...
- 5052 Anodized aluminum plate s...
- 7010 aluminum block
- metal jacket pipe insulation
- Decoration Anodized Strip
- 1100 Aluminium coil
- Oil Tanker Aluminum Plate
- 3000 Series Aluminium coil All...
- pipe insulation jacketing mate...
- Aluminum 2014 Forged Block
- What are the advantages of a g...
- Aluminum jacketing for ductwor...
- Insulation aluminum coil roll...