titanium clad copper rod bar
The titanium clad copper rod bar has been used in the electrolytic copper industry as a conductive rod, which improves the conductivity and current efficiency and reduces the power consumption after use. At the same time, the service life of the electrode is improved, and the maintenance cost is reduced. The composite rod produced by extrusion method has a large amount of deformation (generally more than 95%) and the metal is in a state of three-way compressive stress during extrusion. With huge deformation under high pressure, deep metallurgical bonding occurs at the titanium-copper interface. Broader composite waves and bands will be formed, and the composite strength will be higher. Especially for vacuum casting ingots, in the process of manufacturing composite ingots, titanium and copper have formed a metallurgical bond, which creates very good basic conditions for the manufacture of composite bars with good composite properties.
The advantages of producing titanium clad copper rod bar by extrusion method are that the composite rod has high composite strength and good composite fastness. When turning threads in electrode machining, the turning speed is fast, the amount of feed is large, and there is no separation of titanium and copper; production efficiency High, suitable for mass production. The disadvantage is that the surface roughness of the extruded bar is slightly worse and the bending resistance is low. After a certain amount of cold stretching of the extruded rod, the bending resistance of the composite rod is improved, the surface roughness is also improved, and the dimensional accuracy of the product is improved, and good results have been achieved. Very popular with users. Titanium clad copper rod bar currently available on the market is mainly produced by extrusion + stretching method. Welding copper rod and titanium tube to make ingot: In this billet-making method, the outer diameter of the titanium tube is generally Φ85 mm~Φ125 mm, the wall thickness is 6 mm~7 mm, the grade is TA1 or TA2, and the copper rod is T2 pure copper. When the billet is made, the rolled copper rod is put into the pipe, and then the titanium plate of the same grade is welded with the pipe end by argon arc welding to seal the two ends. Using this method to produce ingots requires thorough cleaning of the inner surface of the pipe and the surface of the copper rod. If there is residual dust, oil, or other foreign matter on the surface, it will affect the good combination of titanium and copper during extrusion, and make the composite performance change. damaged, and the electrical conductivity is reduced. The advantage of this method is that the process is simple and the equipment investment is low; The disadvantage is that the welding quality will directly affect the product quality and yield, because the extrusion deformation of the composite rod is very large, especially the front stress concentration.
The explosion method is to first put the copper rod into the titanium tube, distribute the explosive evenly outside the titanium tube, and use the detonator to detonate the explosive, so that the copper rod and the titanium tube form a compound under the action of the explosive force. Since the section size of the titanium-copper composite rod is generally small, the production efficiency of the explosion method is low, resulting in high cost. At present, almost no one adopts this method in industrial production. Explosion + rolling method is to use larger size titanium tube and copper rod, make billet by explosion method, and then use pass rolling method to produce finished composite rod. This method is For the direct explosion method, the advantage is that it can improve efficiency and reduce costs. The composite bars produced have good composite strength and other indicators. However, since the amount of rolling processing should not be too large, that is, the elongation coefficient is not large, it is not suitable for mass production. At the same time, for the rectangular composite rod, its corners are not easily filled. If the deformation amount of the pass is not well controlled, folds or ears may appear. Due to the hot rolling method of the finished product, the bending resistance of the composite rod is worse, which has an impact on the use. At present, only rectangular and flat bars are produced by this method, and further tests are needed for the suitability of producing other shapes of composite bars by rolling. At the same time, the industrial production of explosion + rolling method needs further exploration.
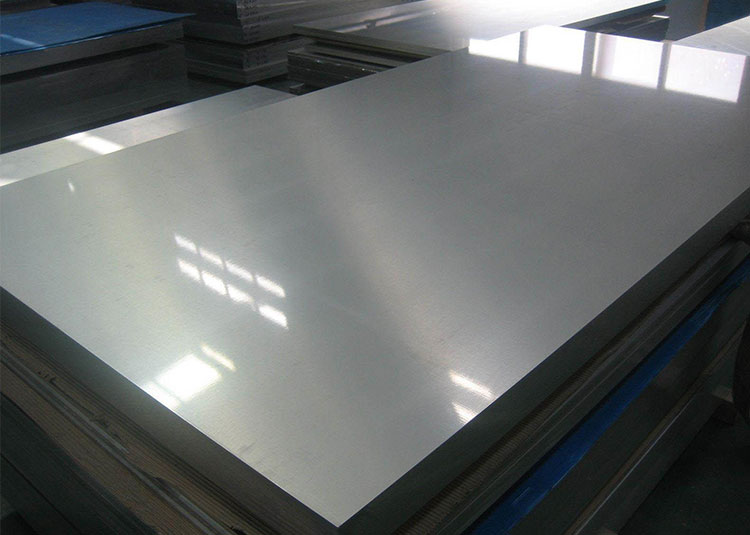
Aluminium Sheets
View Details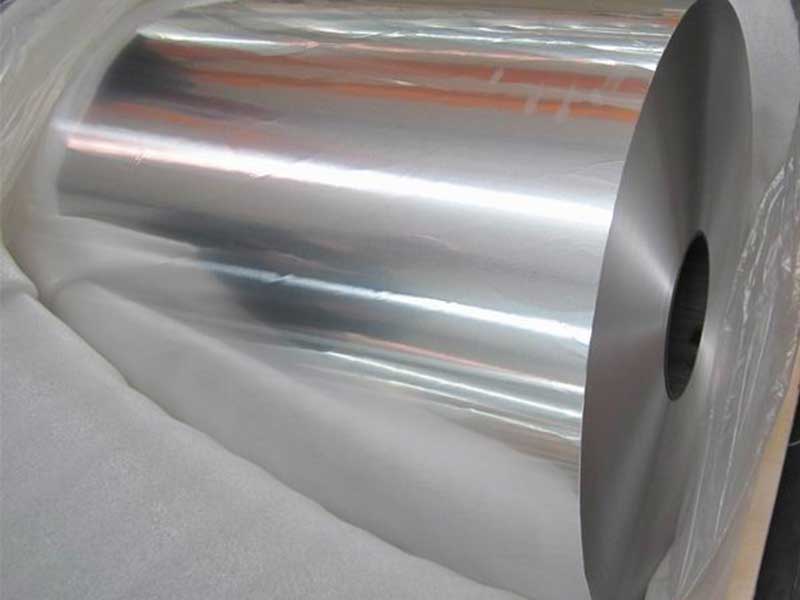
Aluminium Coils
View Details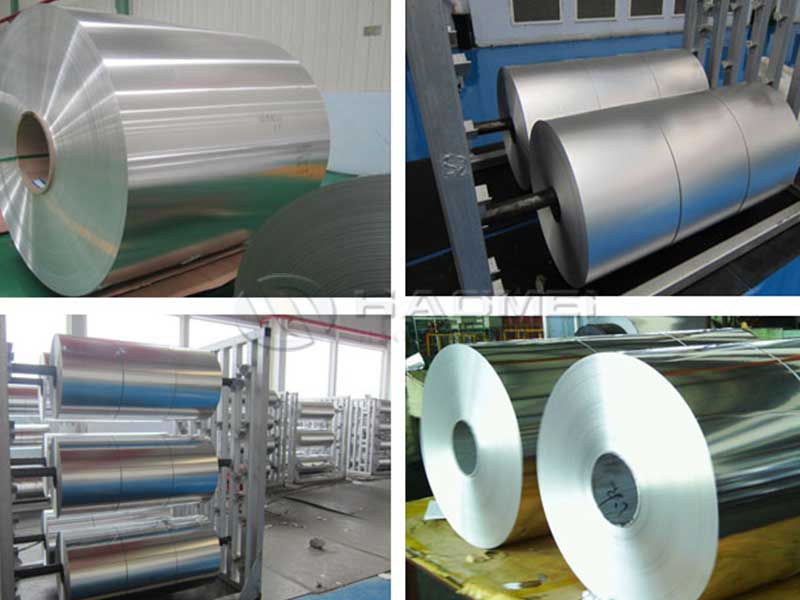
Aluminium Foils
View Details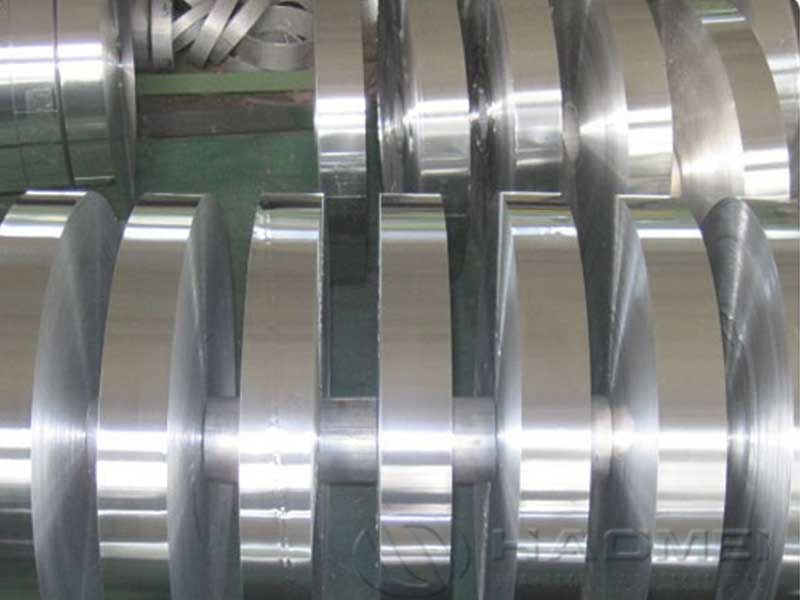
Aluminium Strips
View Details
Aluminium Circles
View Details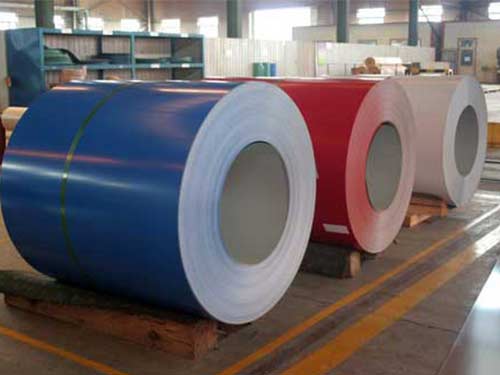
Coated Aluminium
View Details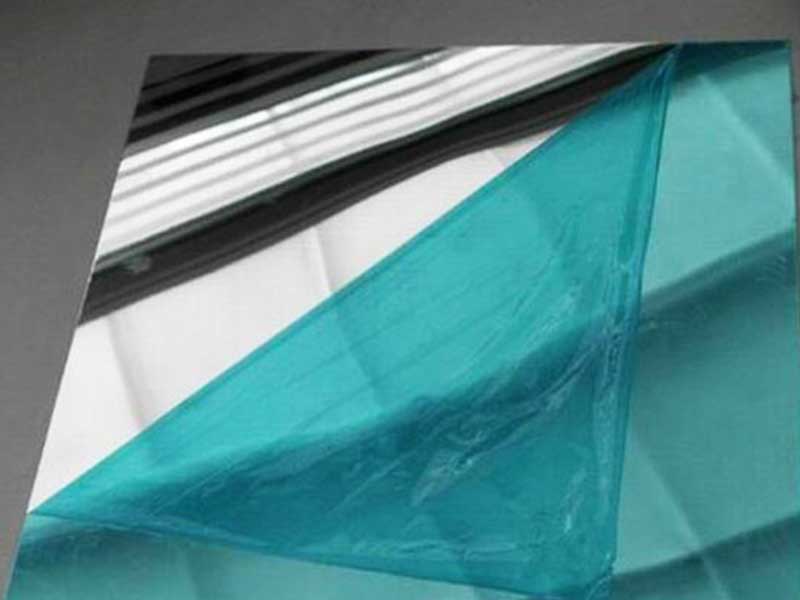
Mirror Aluminum
View Details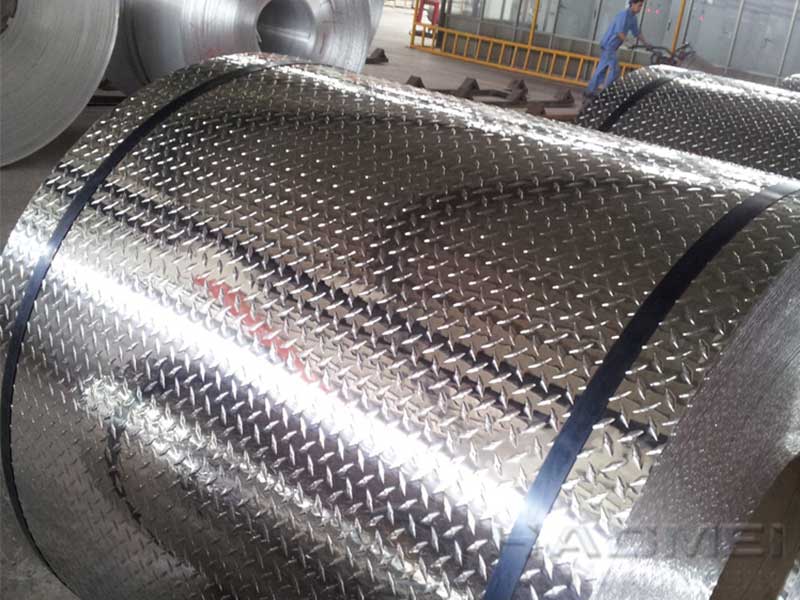
Stucco Embossed Aluminum
View DetailsCopper
- copper aluminum alloy sheet
- Silver plated copper clad alum...
- Copper clad aluminum plate she...
- Difference between copper wind...
- copper clad aluminum bus bars
- Copper Flexible Soft Connector...
- Copper-Aluminium Bimetal Clad...
- nickel clad copper aluminum Ni...
- Copper-Aluminium Bimetal Clad...
- Application of Copper clad alu...
- Cu Clad Al washer Copper alum...
- Copper clad aluminum wire CCA...
- Copper foil soft connection ma...
- copper coated aluminum busbar
- Copper aluminum clad block ter...
- copper washer on aluminum
- Copper clad aluminum coil shee...
- copper coated aluminium busbar
- Tinned Copper Braid Wire Strip...
- aluminium copper bi metal term...