What is rolling friction is the role?
(1) To ensure the realization of the process. In the rolling process, rolling is able to drag into the rolling inside the roll gap, plastic deformation, is back skating area as a result of frictional force, can not be achieved otherwise rolling natural bite.
(2) Changing the object stress state, resulting in metal deformation resistance and increased energy consumption. Due to the presence of friction within the rolling degeneration K object in a three-dimensional stress state, and more for two to compressive stress.
In this case the force required to deform U1) greatly exceeds the deforming force uneasily stress state; if the greater coefficient of friction between the contact surfaces, the greater the friction, i.e. the greater the hydrostatic pressure, along with the increase in the force required to deform large deformation work and thus consumption (energy consumption) increases.
(3) Causes deformation of the work piece and the uneven distribution of stress. When the cylinder compression, due to friction and contact surfaces, cylinders uneven deformation. The larger contact surface friction, the more difficult the flow of metal particle, there are often side turned flat metal particle phenomenon, the greater the contact area, the more serious rollover; away from the contact surface, due to the friction has little effect, particle flow faster the last piece into the drum. In addition, since the outer friction, pressure distribution on the contact surface unit’s uneven work piece gradually increased pressure from the edge to the center, and then contacting the midrace three strongest to compressive stress.
(4) Accelerated roll wear and reduce service life. Roll wear occurs on the one hand by the contact surface caused by sliding or adhesion; on the other hand is due to frictional heat generated between the contact pairs increased roll wear. In addition, due to the friction of the work piece inhomogeneous deformation and deformation force increases will accelerate the roll wear.
(5) The deterioration of product quality and increase metal consumption. Roll wear not only directly affect the surface quality of the rolled product, but also adversely affect the dimensional accuracy and organizational performance, such as uneven plate deformation caused by partial cracking, uneven organizational performance, thin plate-shaped variation, surface roughness gain.
(6) Reduce the operating rate, increase in production costs. Reduce drop roller life and product quality due to wear and tear caused by the direct impact on production costs, not only that, frequent replacement of the rolls of the rolling operation also led to decline in the rate.
The Role of Rolling Friction
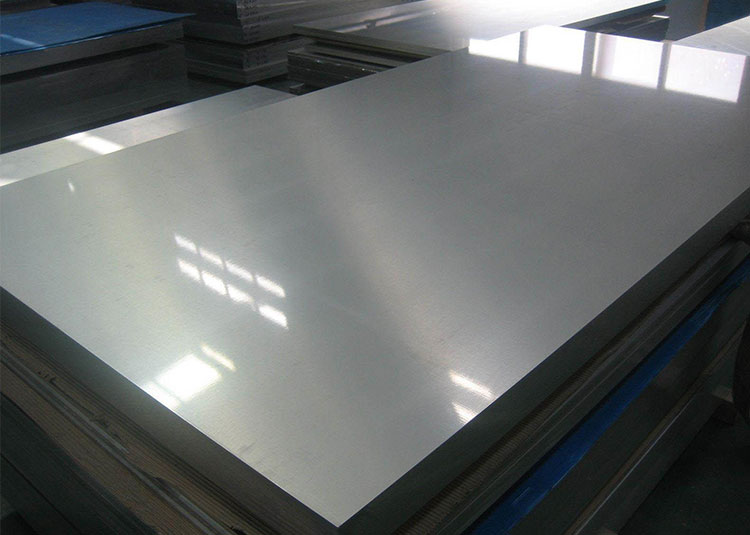
Aluminium Sheets
View Details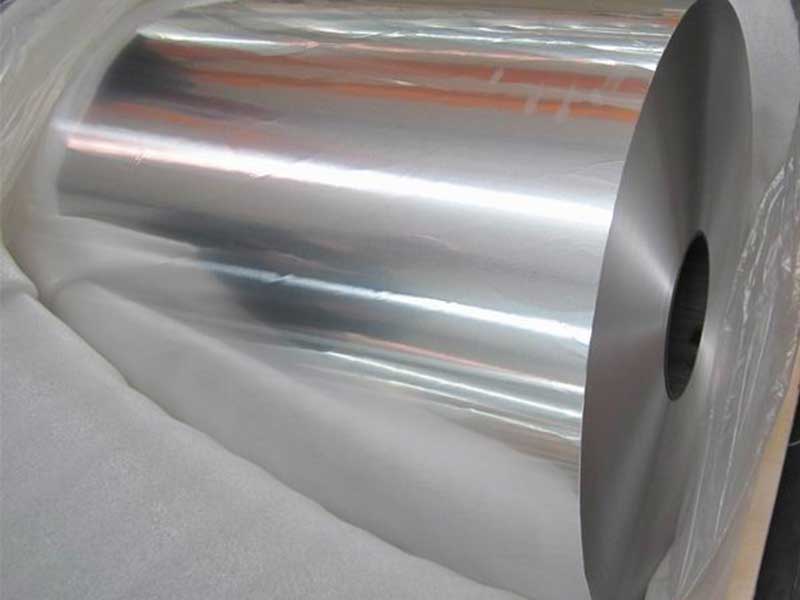
Aluminium Coils
View Details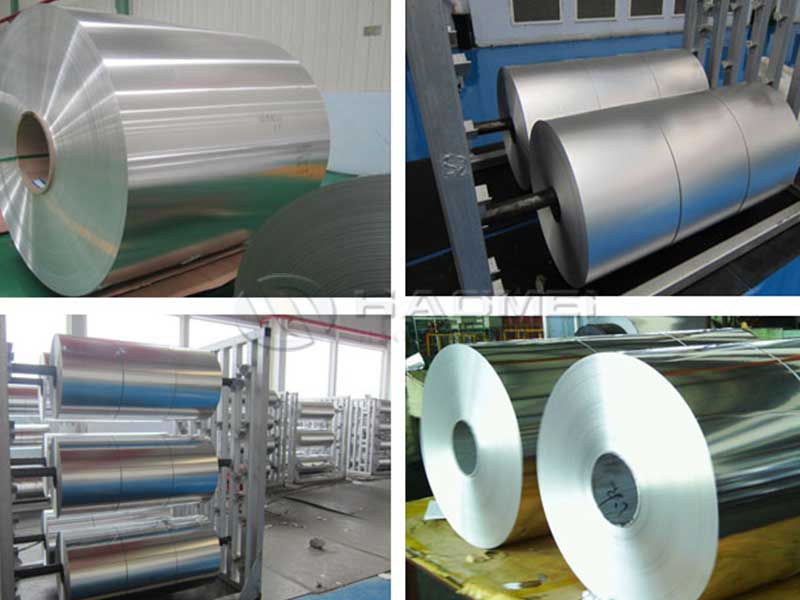
Aluminium Foils
View Details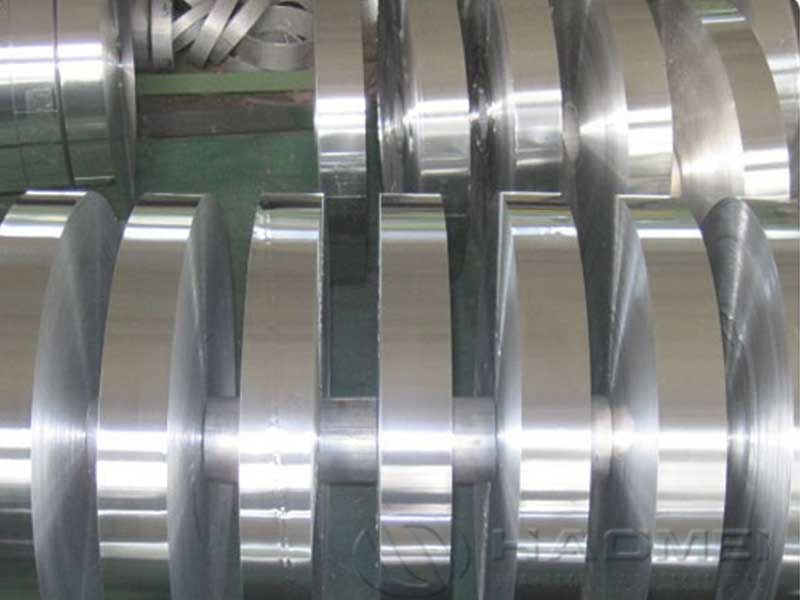
Aluminium Strips
View Details
Aluminium Circles
View Details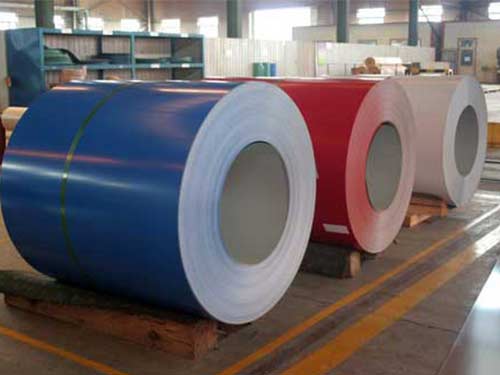
Coated Aluminium
View Details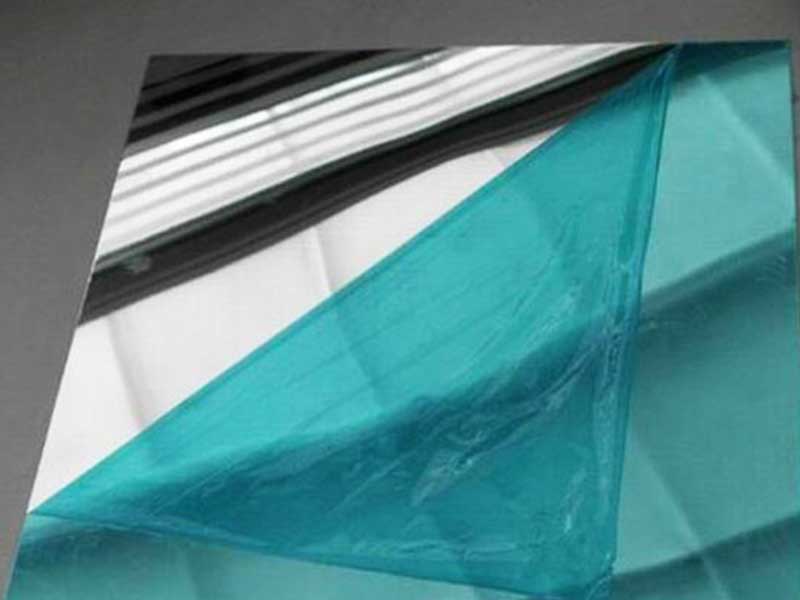
Mirror Aluminum
View Details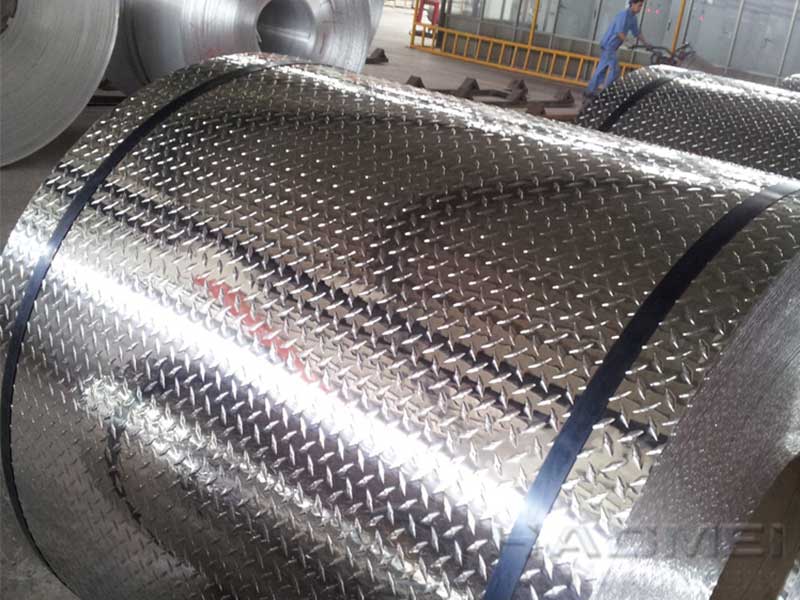
Stucco Embossed Aluminum
View DetailsAluminum
- Requirements for cathode carbo...
- Which aluminum wafer manufactu...
- Anode yoke bracket supplier
- Ultrawide & Thin Aluminium She...
- super enameled aluminum flat w...
- 1070 H18 battery grade alumini...
- 5052 Anodized Circle
- Aluminum voice coil wire
- large aluminum disc
- Aluminum discs blank
- aluminum pipe lagging
- 1050 aluminum square bar block...
- 8006 aluminium foil container
- 1060 Aluminum Block
- Decorative painting aluminum f...
- 2A11 mold aluminum plate mediu...
- 7175 aluminum
- aluminum profile photo frame
- Insulation aluminum coil roll...
- Comparison of anodized aluminu...