Aluminium sheet anodizing, chemical oxidation and differences
1 ★ The role of anodizing:
☆ protective
☆ decorative
☆Insulation
☆ Improve the bonding with organic layers.
☆ Improve the bonding with inorganic coating
☆Other functions in development
2. Chemical conversion film treatment of aluminum alloy (chemical oxidation, passivation, chromization)
★ The chemical conversion film of aluminum alloy is obtained by chemical oxidation, and can be referred to the US military standard MIL-C-5541.
★ Why do you need to carry out chemical conversion film treatment of aluminum alloy?
☆ Strengthen the anti-rust ability of aluminum alloy.
☆ can play a role in stable contact with electricity. (A customer's product required conductive oxidation, the purpose is to stabilize contact resistance and conduction)
☆The conversion film is thin (about 0.5~4um), soft, conductive, porous, and has good adsorption capacity, usually used as the bottom layer of paint or other coatings.
☆ Does not change the mechanical properties of the material.
☆ Simple equipment, easy operation and low price.
☆ Does not affect the workpiece size.
★Conversion film thickness
The chemical conversion coating on the surface of the aluminum alloy is about 0.5~4um thinner. The conversion coating is a kind of gel. It is difficult to measure directly. Usually, the weight of the workpiece before and after chemical oxidation is measured, or the surface color and salt spray test are used to judge the oxidation. The corrosion resistance of the film.
★ Anti-corrosion function after scratching
The chemical conversion film on the surface of the aluminum alloy is a gel. The colloid can move after the conversion film is scratched, and the gel around the scratch will move to the scratched surface, and together, continue to block the corrosion of the aluminum alloy. Still have anti-corrosion function.
★ color
The color of the aluminum alloy chemical conversion film is gray, white, grass green, golden yellow, rainbow color, and the final color of the conversion film is related to the conversion film syrup used and the operating process conditions.
3. The difference between anodizing and conductive oxidation
1). Anodizing is carried out under high voltage, it is an electrochemical reaction process; conductive oxidation (also called chemical oxidation) does not require electricity, but only needs to be soaked in the syrup, it is A purification reaction.
2). The time required for anodizing is very long, often takes several tens of minutes, and conductive oxidation requires only a few tens of seconds.
3). The film formed by anodization has a few micrometers to several tens of micrometers, and is hard and wear resistant, and the film formed by conductive oxidation is only about 0.01 to 0.15 micrometers. The wear resistance is not very good, but it is both electrically conductive and resistant to atmospheric corrosion, which is its advantage.
4). The oxide film is inherently non-conductive, but because the film formed by conductive oxidation is really thin, it is electrically conductive.
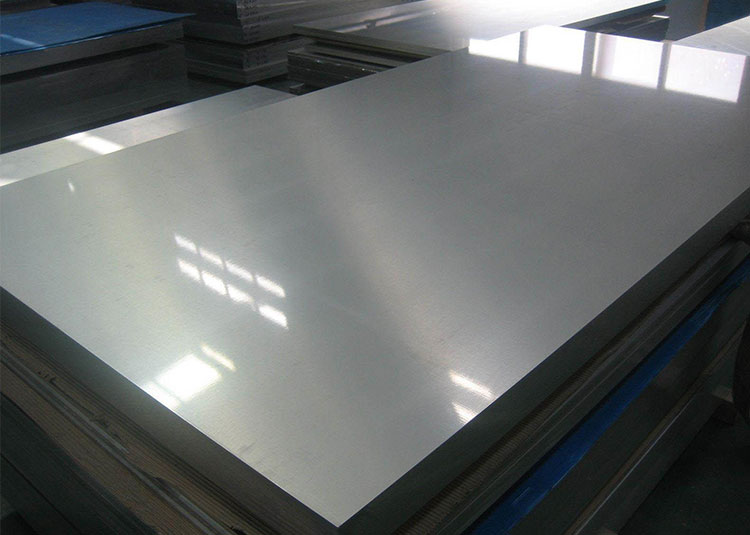
Aluminium Sheets
View Details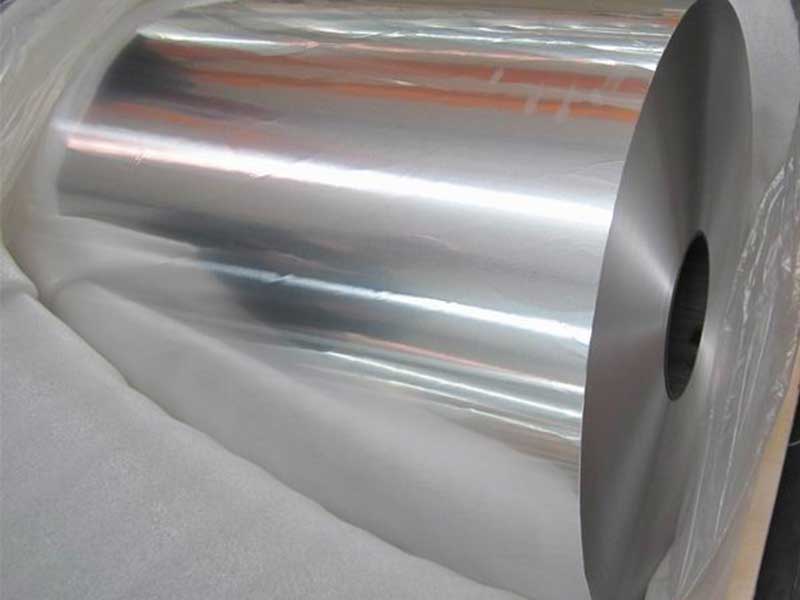
Aluminium Coils
View Details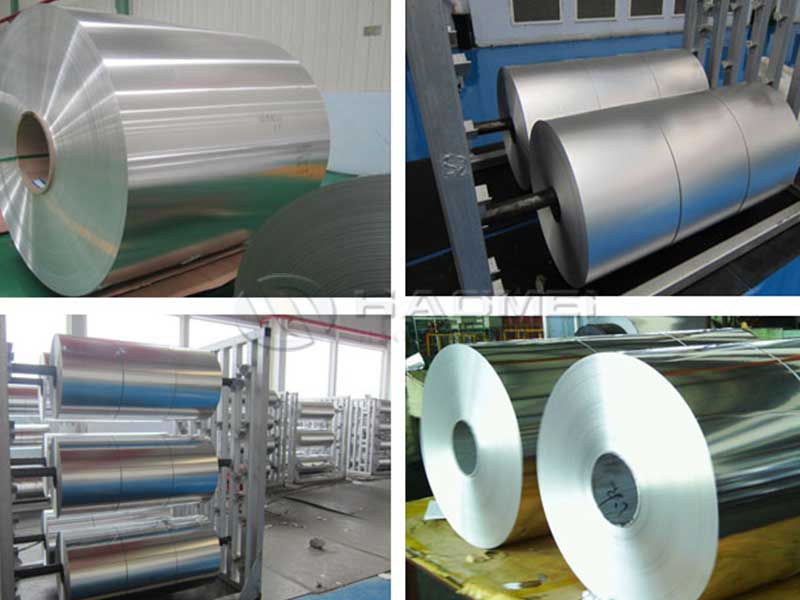
Aluminium Foils
View Details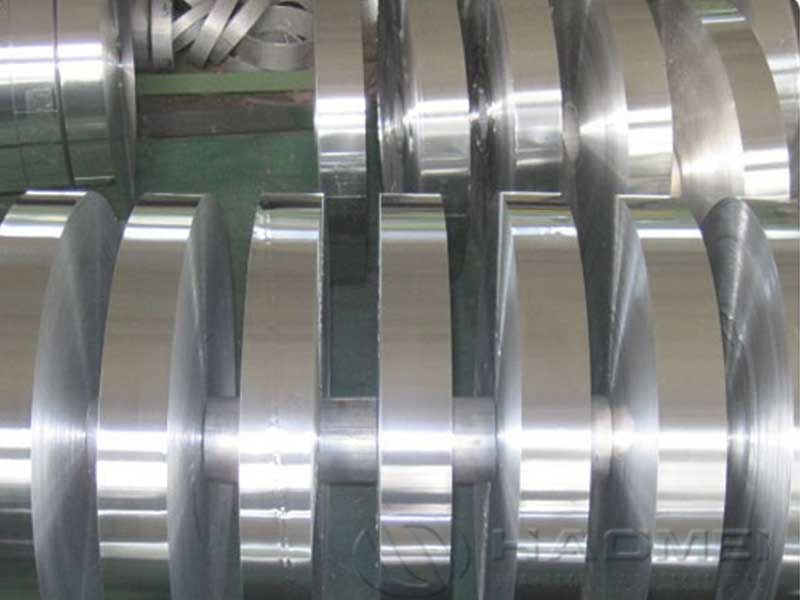
Aluminium Strips
View Details
Aluminium Circles
View Details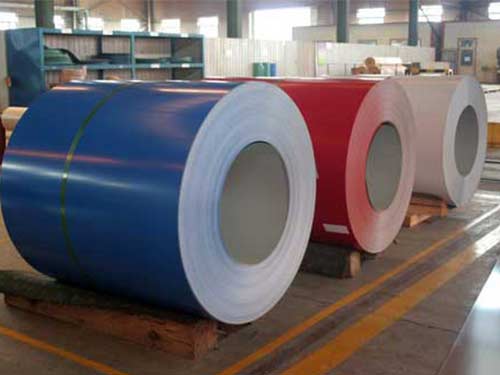
Coated Aluminium
View Details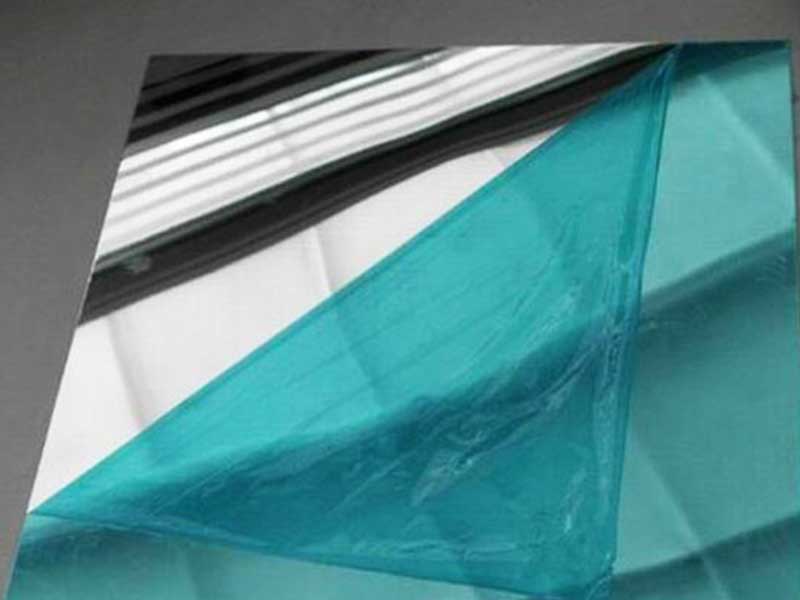
Mirror Aluminum
View Details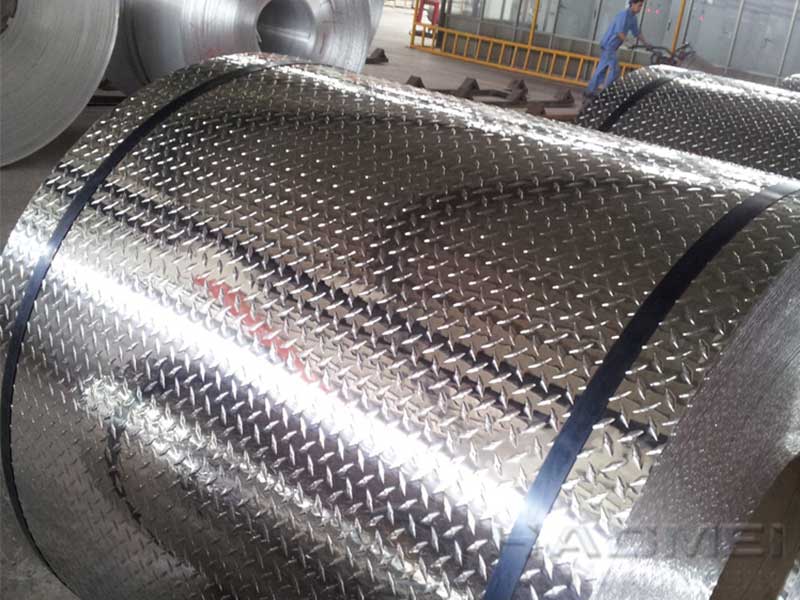
Stucco Embossed Aluminum
View DetailsAluminum
- anodized aluminum discs
- Anodized Aluminum Packaging
- 6082 Aluminium Flat Bus Bar
- AL1060, 1050, 1070, 1350 anodi...
- aluminum discs blank
- Hot rolled aluminium circle sh...
- aluminium 7075 t6 plate block
- aluminum circles supplier
- China aluminum anode component...
- 1100 Aluminum tread plate
- Aluminium anodised veneer cano...
- Technical Features of Aluminiu...
- Ultrafine Rectangular Aluminum...
- 6082 aluminium deoxidation hot...
- What is Brushed Aluminum Plate
- 1100 1145 1235 Aluminum Insula...
- Aluminium checker plate,alumin...
- mirror finish anodized aluminu...
- solid metal circle
- 5754 Aluminum plate