aluminum conductors in transformer
Copper transformers are no longer advocated and manufactured. The reasons are as follows: firstly, it is considered that the resistivity of aluminum is high and the conductivity is only 60% of that of copper. Under the same voltage level, capacity and loss, the volume of aluminum conductor transformer is larger; Second, it is considered that the mechanical strength and thermal shock resistance of aluminum are far inferior to copper, so it is considered that the dynamic and thermal stability of aluminum instead of copper transformer is poor; In addition, the problem of copper aluminum welding has not been well solved, which also restricts the development of aluminum winding transformer. However, because the production of copper has been difficult to meet the growing demand, aluminum winding transformers have been gradually developed all over the world. At present, aluminum conductors in transformer the production technology has been very mature and widely used. At the same time, due to the violent fluctuation of copper price in recent years, the development of aluminum winding epoxy resin cast dry-type transformer has gradually formed a consensus among domestic dry-type transformer manufacturers and is manufactured in large quantities.
The resin cast dry-type transformer with aluminum foil wound high and low voltage is an early variety of resin cast dry-type transformer in China. In the early 1990s, this kind of transformer experienced a period of high accident incidence. Through analysis, the main causes of the accident are the quality and process of aluminum foil
And tooling. With the development of raw material industry and the continuous improvement of dry-type transformer pouring equipment, the product quality produced by some domestic manufacturers after appropriate process improvement of this technology has been very stable. Compared with other types of resin cast dry-type transformer, this type of product has the following advantages.
(1) Compared with wire wound winding, the production efficiency of foil wound winding is ficantly improved, and the tooling and die are simple, which is conducive to organizing large-scale production.
(2) When wire winding is used for high and low voltage, the reactance height of the two windings often varies greatly, especially for products with large capacity. Due to the large low-voltage current, multiple wires need to be wound together, and the ampere turn distribution between high and low voltage is uneven, which will produce great transverse magnetic leakage during transformer operation, which is not conducive to the dynamic and thermal stability of the transformer. The winding made of foil conductor can easily solve this problem.
(3) The interlaminar voltage of foil winding is the turn to turn voltage, while the interlaminar voltage of wire wound winding is equal to the product of turn voltage and number of turns
From the point of view of strength, the interlaminar field strength of wire wound winding is much higher, and it is much simpler to deal with the interlaminar insulation of foil wound winding.
(4) The eddy current loss of transformer winding is directly proportional to the 4th power of the radial thickness of conductor, and foil wound winding, especially low-voltage winding,
Due to the thin foil, the eddy current loss of the winding can be effectively reduced. Compared with wire wound winding, the eddy current loss of foil wound winding is reduced by about 40%.
(5) When multi-stage foil winding is adopted for high-voltage winding, due to the large longitudinal series capacitance of winding, the voltage gradient distribution of dry-type transformer under lightning impulse is greatly improved, and it has strong lightning impulse resistance. It is precisely because the high and low pressure are all made of aluminum foil
Type transformer has the above five advantages. This type of transformer has been greatly recognized and developed well in Europe. At the same time, this type of resin cast dry-type transformer also occupies a considerable market share in China. The author believes that domestic manufacturers can give priority to this type of aluminum winding transformer when manufacturing aluminum conductor transformer.
From the above discussion, it can be seen that aluminum conductors in transformer, especially the resin cast dry-type transformer with aluminum foil for high and low voltage windings, is no worse than the copper winding dry-type transformer in terms of technical performance, dynamic and thermal stability. At the same time, the excellent economic and technical indexes of aluminum winding transformer are the energy-saving products urgently needed to be developed in China. In fact, due to the increasingly prominent contradiction between supply and demand of copper materials and the violent fluctuation of copper price in recent years, many transformer manufacturers have to use aluminum conductor to replace copper conductor. These aluminum winding transformers that have operated safely for several years have well proved the reliability of aluminum winding transformers, indicating that aluminum winding resin cast dry-type transformers are worthy of vigorous promotion.
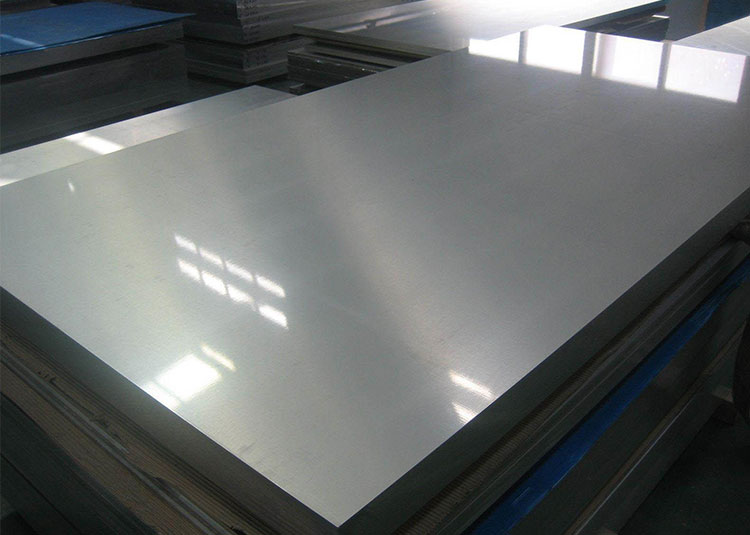
Aluminium Sheets
View Details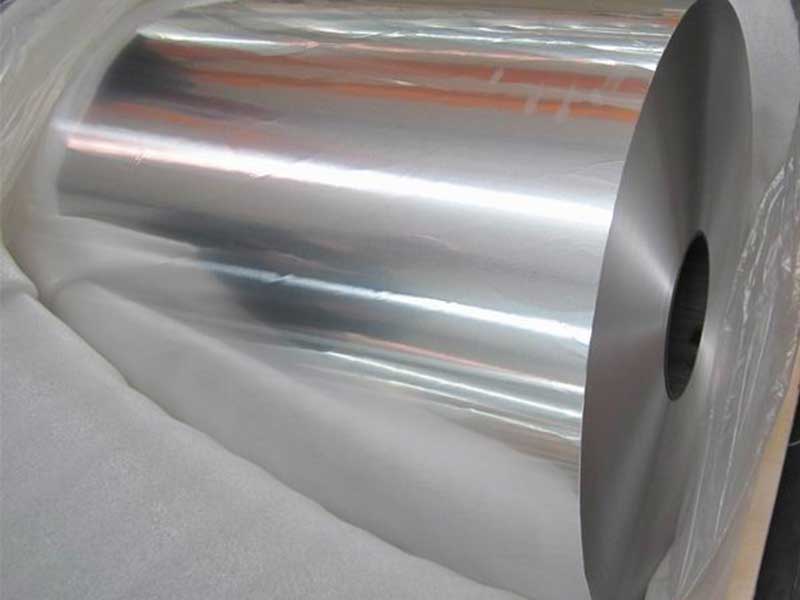
Aluminium Coils
View Details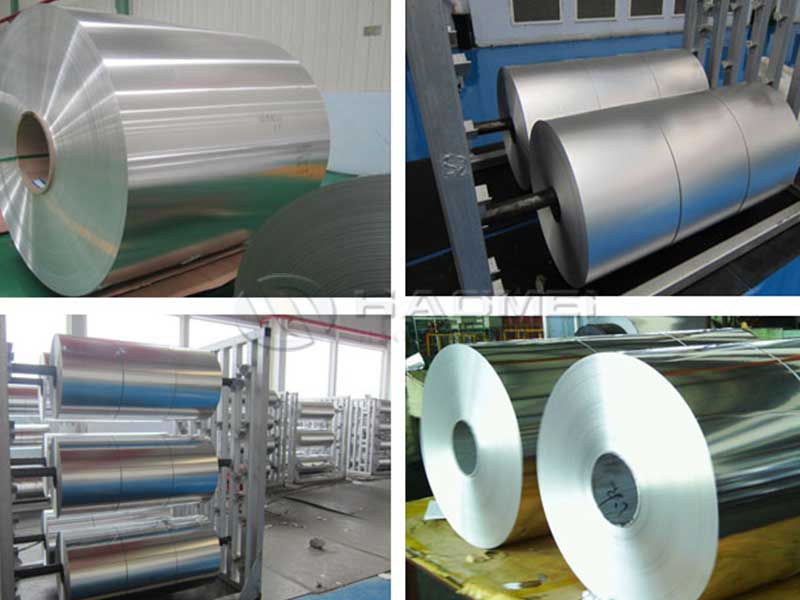
Aluminium Foils
View Details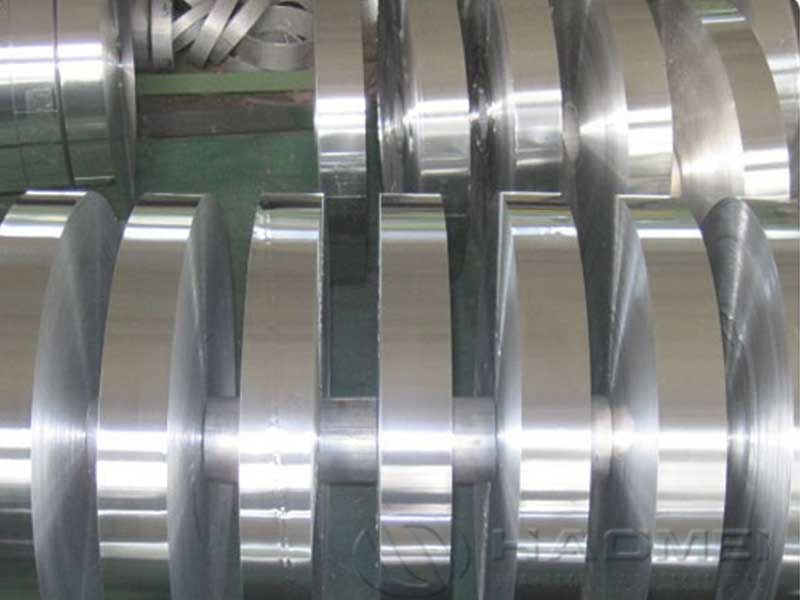
Aluminium Strips
View Details
Aluminium Circles
View Details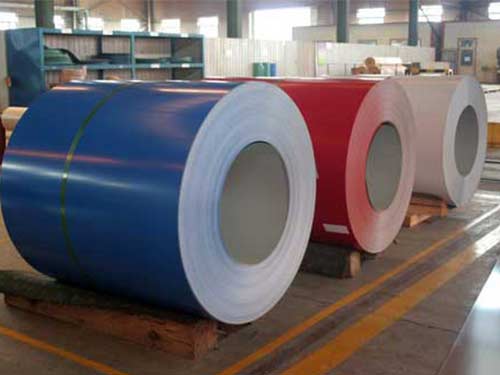
Coated Aluminium
View Details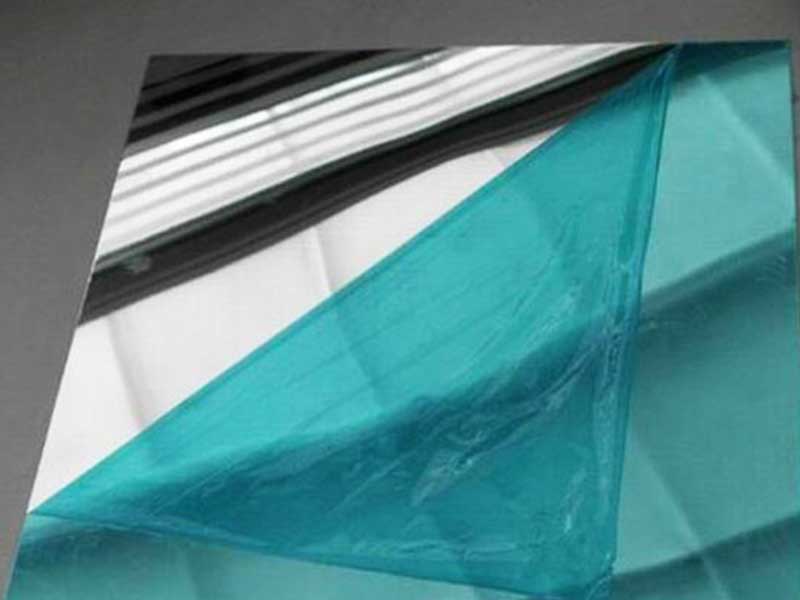
Mirror Aluminum
View Details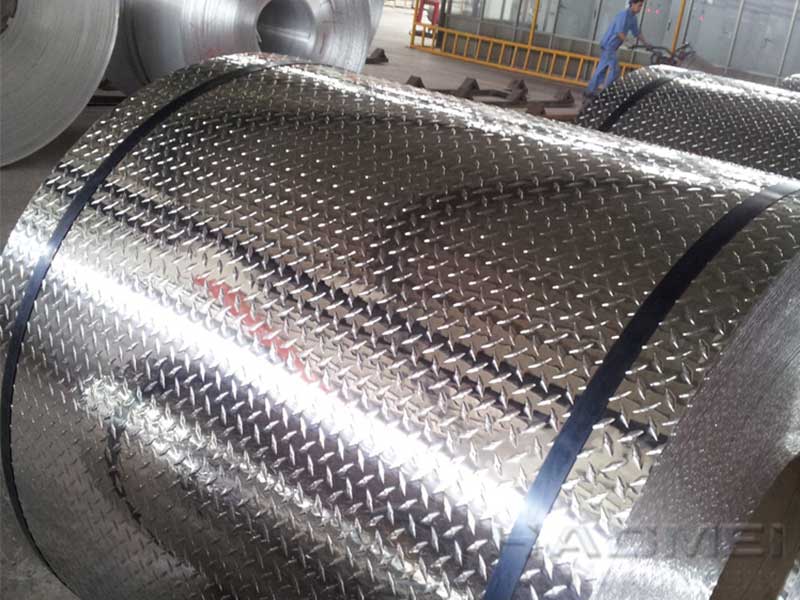
Stucco Embossed Aluminum
View DetailsAluminum
- 1100 Anodised Coil Sheet
- Aluminum Foil for Cigarette Pa...
- 3102 H22 H18 aluminium foil fo...
- Anodized aluminium sheet rolls
- 6063 high precision aluminum b...
- Maintenance method of aluminum...
- PET-ALU-PE
- 1050 Aluminium Flat Bus Bar
- Stucco Embossed Aluminum Sheet
- Introduction to aluminum foil
- Coated Aluminum Roll Jacketing...
- Advantages of anodized aluminu...
- 5554 aluminum alloy welding wi...
- Fireproof Aluminum Composite P...
- Precision aluminum circle plat...
- 3004 3105 Aluminum Cap Strip F...
- 5052 Anodised Coil
- reflective aluminum sheet for...
- 6101 Aluminum Sheet
- 8079 Aluminium coil