Анод на предварительно обожженном баке заменяется новым анодом после определенного периода использования, а часть, которая не израсходована, является остаточным анодом. Эти остаточные аноды возвращаются в систему производства анодов после отделения стальных захватов, очистки электролитом и дробления угольных блоков. Обратный остаточный электрод оказывает определенное влияние на механическую прочность, остаточную реакционную способность воздуха и остаточную реактивность углекислого газа предварительно обожженного анода. Соответствующие предварительно обожженные аноды с остаточными электродами хорошо влияют на снижение затрат на производство анодов, улучшение механических свойств анодов и стабилизацию качества производства анодов. Качество предварительно обожженных анодов с остатками высокого качества лучше, чем у предварительно обожженных анодов с низким содержанием остатков или без них. Однако в реальном производстве предприятия по производству алюминиевого электролитического углерода, которые переваривают остаточный электрод, имеют больше остатков электролита на поверхности остаточного электрода во время очистки, штабелирования, дробления, самоизмельчения и других процессов из-за ограничивающих факторов во всех аспектах производство, и очистка не является чистой. После измельчения электролит в виде золы напрямую подается в систему производства предварительно обожженных анодов.
Как уменьшить зольность остаточного анода?
Чтобы снизить содержание золы в остаточном столбе, каждое предприятие принимает различные меры для контроля остаточного содержания золы в соответствии с реальной ситуацией, в основном включая ручную очистку стальной щеткой, выброс мелких частиц остаточного столба и экспериментальные исследования остаточного столба. самоизмельчение и другие мероприятия по снижению остаточной зольности столба. Зола в остатке. В настоящее время установки для электролиза алюминия, которые возвращаются к остаточному электроду, в основном реализованы за счет контроля количества остаточного электрода, усиления очистки остаточного электрода и использования некоторых новых технологий и оборудования.
1. Используйте дробеструйную очистку остаточного столба, этот метод может частично решить проблему очистки поверхности остаточного столба, но количество стального песка, используемого в этом оборудовании, относительно велико, и стоимость одного только стального песка увеличивается более чем на 100 000 юаней за единицу. в месяц и требует работы специальных операторов, нагрузка на техническое обслуживание оборудования велика, оборудование часто выходит из строя, эксплуатационные расходы высоки, и они не используются в реальном производстве.
2. Обработайте с помощью цепного стропа и проволочной щетки, то есть добавьте цепной строп и проволочную щетку для обработки поверхности подвешенной остаточной опоры до того, как остаточная опора будет отделена от стальных когтей. Этот метод не годится для очистки нижней части остаточного столба. Внутри было много пыли, и окружающая среда была очень суровой. Многим производителям без специального обеспыливания пришлось отказаться от этой меры.
3. Улучшить просеивание производственного процесса, улучшить линию производства необработанных анодов и просеять остаточный электрод ниже Φ1 мм после того, как остаточный электрод будет измельчен, чтобы остаточный электрод Φ1 мм в производстве не попадал в производственную систему дозирования; специфическая оптимизация Метод процесса следующий: остаточный материал с крупными частицами непосредственно смешивается с производственной линией; для гранулированного материала после классификации виброситом делается специальный канал, строится наполнительный бункер для хранения гранулированного материала Φ1-6 мм, а для передачи гранулированного материала устанавливается винтовой конвейер. Материал транспортируется к внешнему трубопроводу и непосредственно в новый бункер, а порошок с остатками мелких частиц менее Φ1 мм выгружается непосредственно в бункер для пыли.
Ввиду проблем, существующих в оборудовании и методах очистки остаточного электрода, сначала пройдите промышленные испытания, такие как дробеструйная машина и очистка стальной щеткой на месте, в сочетании с фактической компоновкой существующего технологического оборудования производственной линии, замените экран в нижней части вибросита и удалите остаточный электрод ниже 1 мм. Выгрузка порошка может обеспечить автоматическое отделение порошка остаточного электрода в режиме онлайн, эффективно решить экологические проблемы, вызванные другими методами очистки остаточного электрода, и заложить хорошую сырьевую основу для производства высококачественных предварительно обожженных анодов и улучшения экономических и технических показателей. электролиза алюминия.
Как уменьшить зольность остаточного анода?
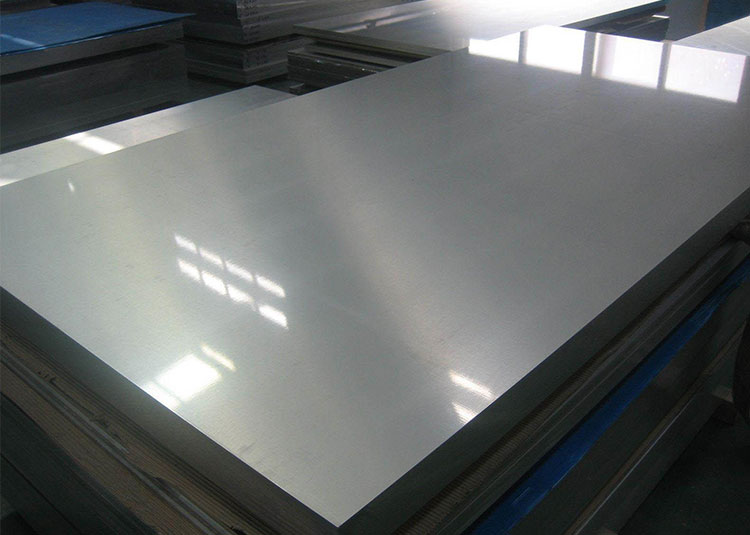
Алюминиевые листы
Посмотреть детали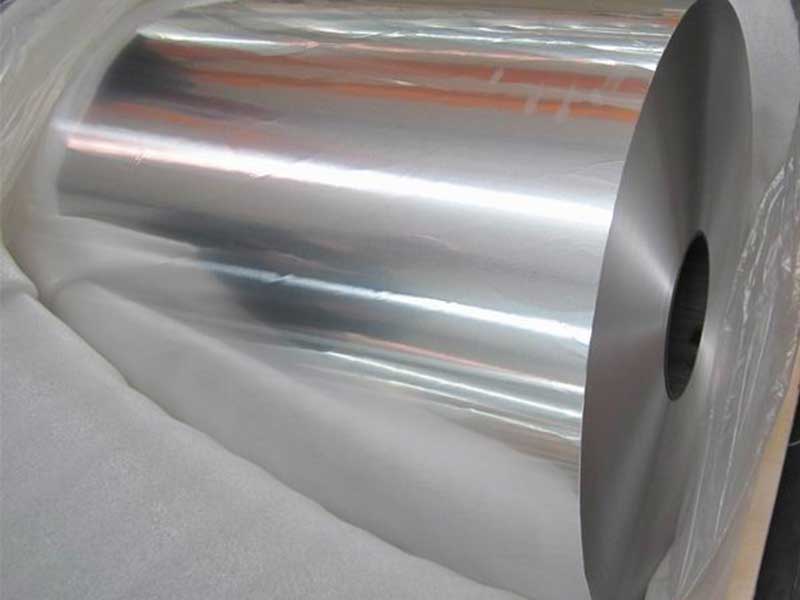
Алюминиевые катушки
Посмотреть детали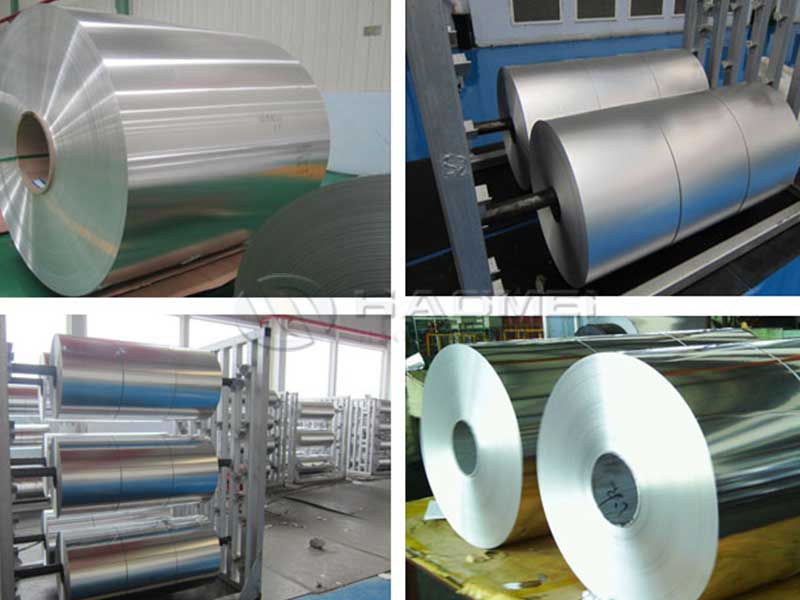
Алюминиевая фольга
Посмотреть детали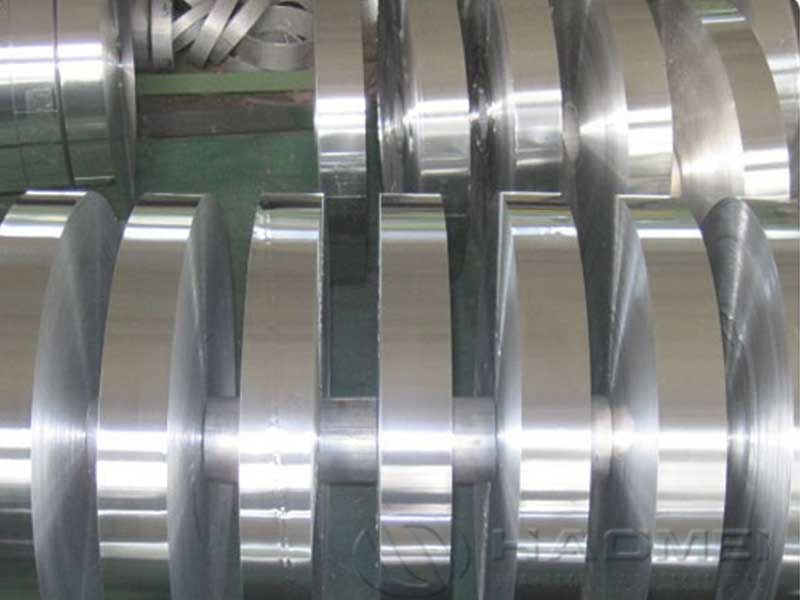
Алюминиевые полосы
Посмотреть детали
Алюминиевые круги
Посмотреть детали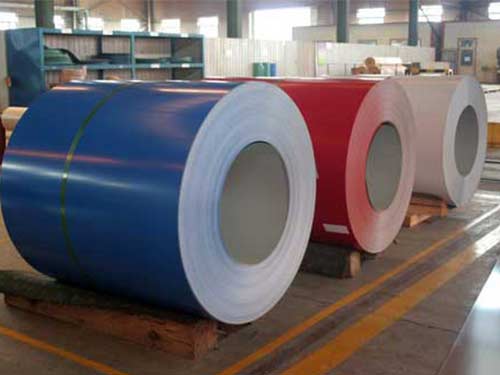
Алюминий с покрытием
Посмотреть детали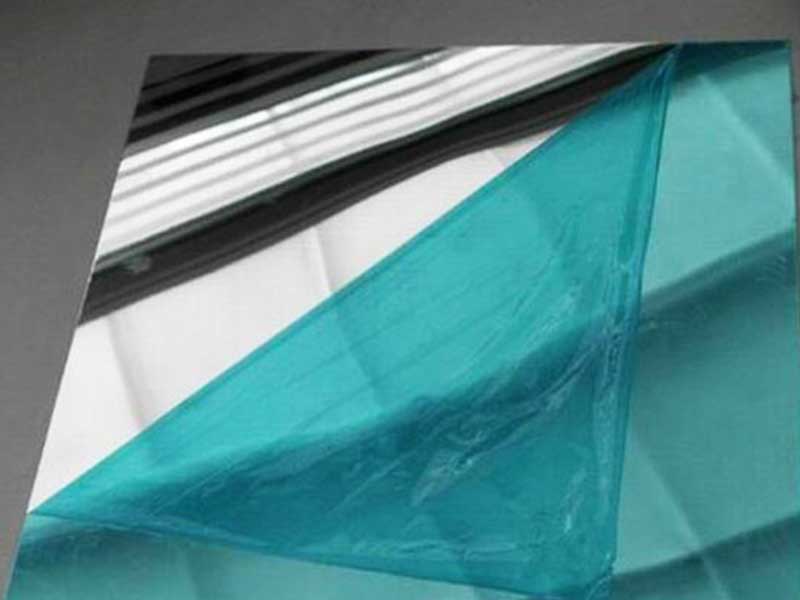
Зеркальный алюминий
Посмотреть детали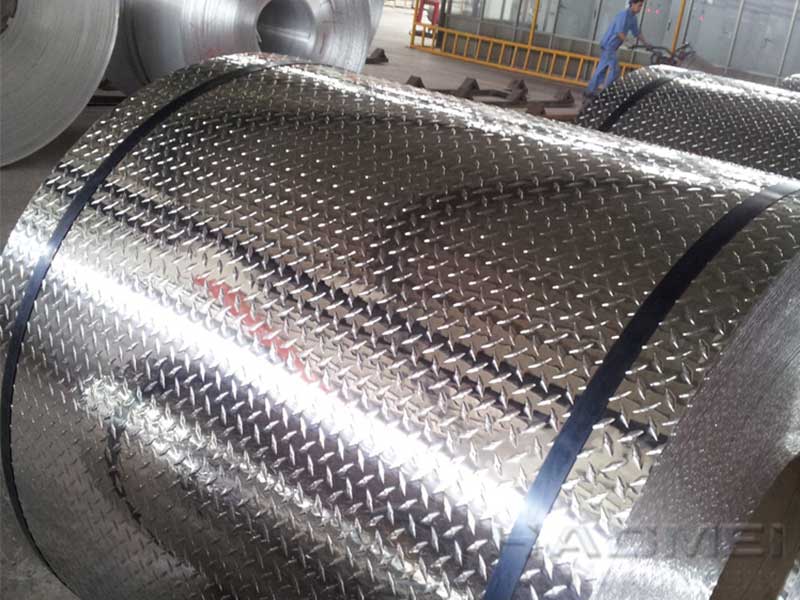