В процессе электролитического производства алюминия между электролизерами используется последовательный режим. Катод электролизера использует углерод в качествекатод. Алюминиевая шинасоединение между электролитическими ячейками, алюминиевая шина соединена скатодный угольный блоккатодным стальным стержнем. В процессе электролитического производства нижний слой электролизера возле катода представляет собой жидкий алюминий толщиной 20-30 см, а верхний слой - электролит толщиной 15-22 см. Анод погружен в жидкость электролита, а среднее напряжение электролизера составляет: 3,9-4,3В от дна 4-5см0 до ладони электролизера. V эффект + V выравнивание шины соединения.
Потребляемая мощность постоянного тока в тоннах алюминия = 2980X среднее напряжение + КПД по току. Таким образом, единственный способ уменьшить потребляемую мощность постоянного тока в тоннах алюминия — это снизить среднее напряжение и повысить эффективность тока. В настоящее время конкуренция на рынке электролитического алюминия становится все более жесткой, и снижение энергопотребления стало ключевым фактором развития алюминиевого электролитического производства.катодный угольный блокв ремонтном баке стальной стержень был расплавлен, а токопроводящего соединителя не было, поэтому бак пришлось остановить на капитальный ремонт. С учетом этой ситуации был разработан электролитический алюминиевый катодный алюминиевый стержень.
Электролитические алюминиевые катодные стержнив среде с температурой выше, чем температура плавления 660 ° C, не плавятся. Во-первых, падение давления на дне может быть уменьшено, что позволяет сэкономить тонны потребляемой мощности алюминия; во-вторых, понять, что электролизер не будет вынужден останавливаться, потому что катод не имеет проводящего стержня, что значительно продлевает срок службы электролитической ячейки, снижает инвестиции, экономит затраты и повышает эффективность. Третий не повлияет на качество первичной алюминиевой жидкости, поскольку исходный стальной стержень расплавлен.
Электролитический алюминиевый катодный алюминиевый стержень
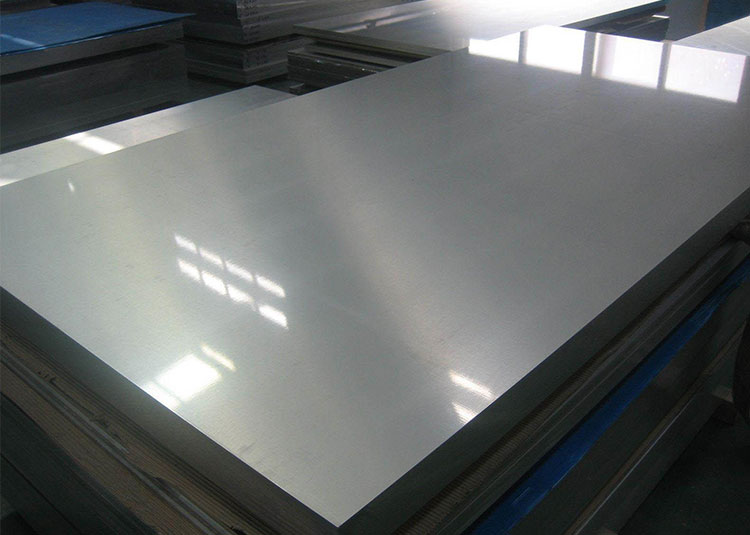
Алюминиевые листы
Посмотреть детали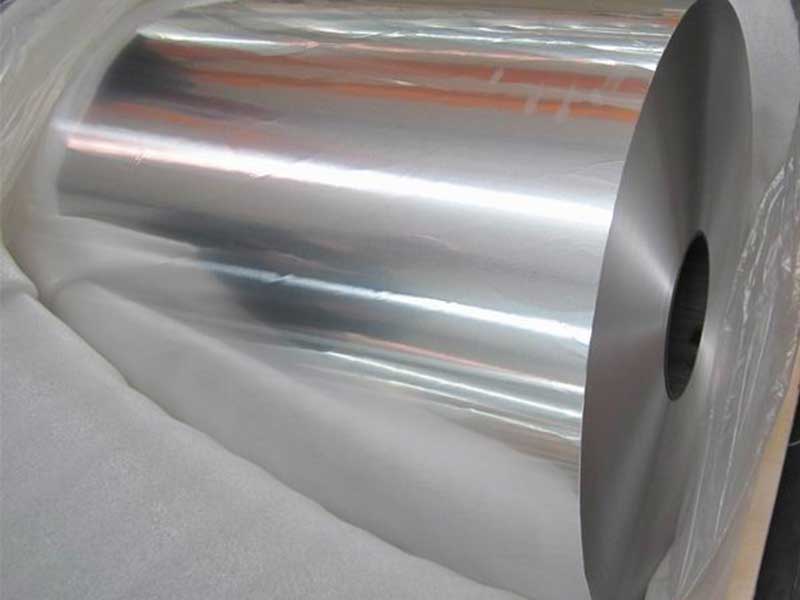
Алюминиевые катушки
Посмотреть детали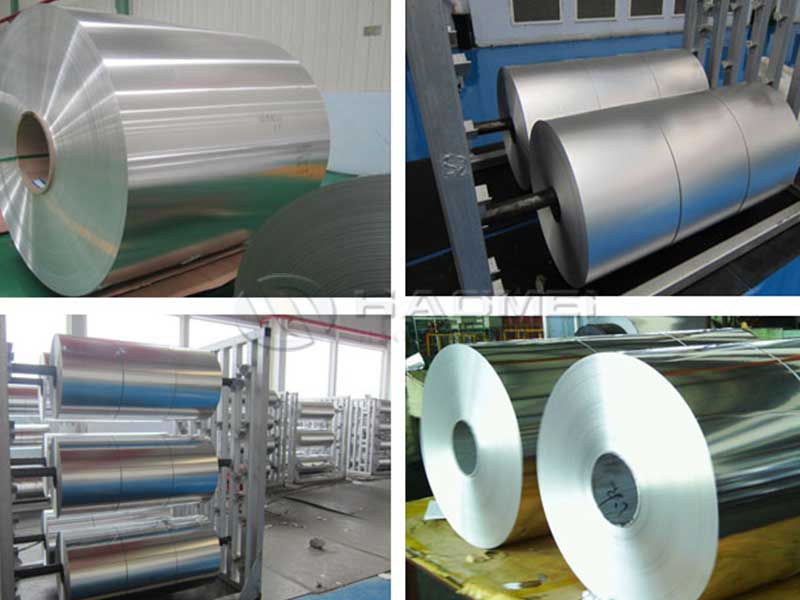
Алюминиевая фольга
Посмотреть детали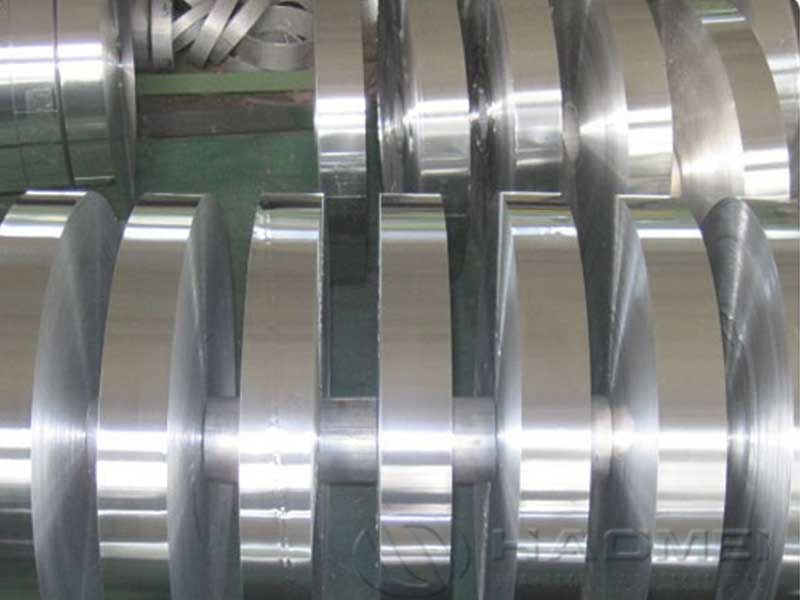
Алюминиевые полосы
Посмотреть детали
Алюминиевые круги
Посмотреть детали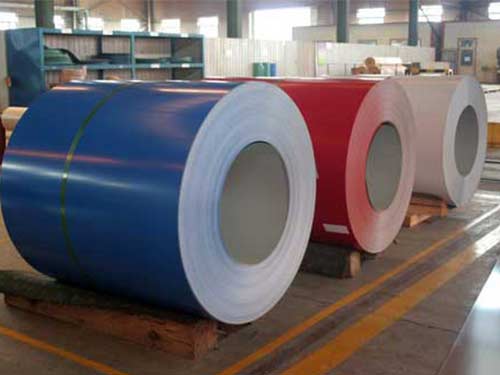
Алюминий с покрытием
Посмотреть детали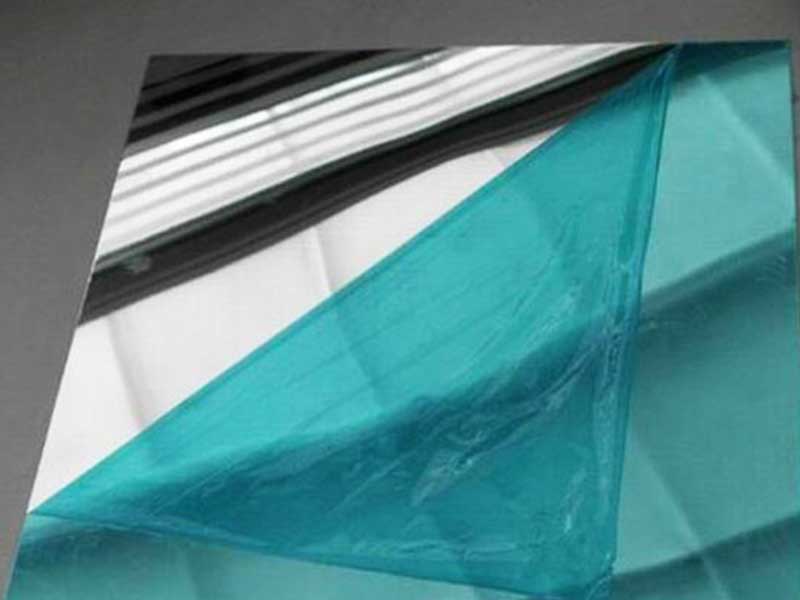
Зеркальный алюминий
Посмотреть детали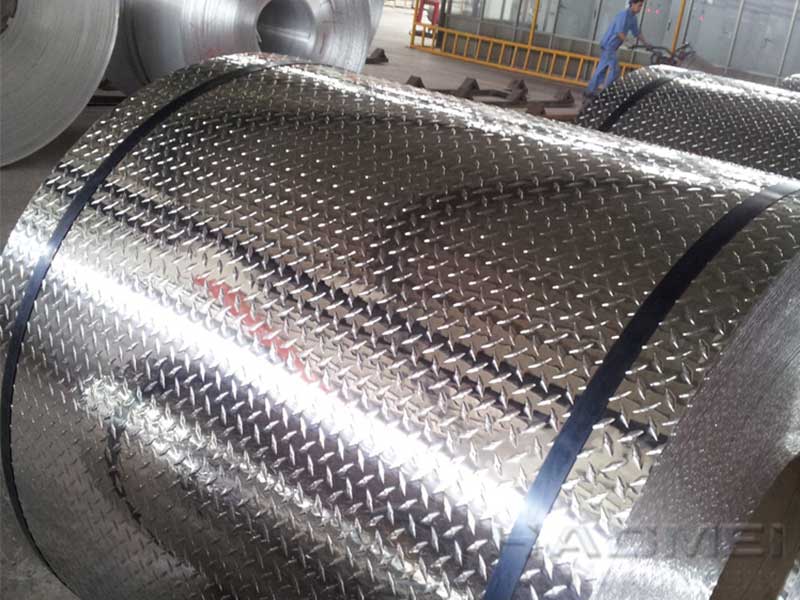